Researchers at the Department of Energy’s Oak Ridge National Laboratory have developed a robotic disassembly system for spent electric vehicle battery packs to safely and efficiently recycle and reuse critical materials while reducing toxic waste.
With the anticipated growth in EVs over the next two decades comes the issue of how to recycle the large lithium-ion battery packs that power them. ORNL engineers put together a demonstration to show that robots can accelerate disassembly and make the process safer for workers while greatly increasing throughput.
Only a small percentage of lithium-ion vehicle batteries are recycled today, and the majority of the processes used to do so are not automated, said Tim McIntyre, principal investigator in ORNL’s Electrification and Energy Infrastructures Division.
Whether a recycler simply wants to get through the outer housing to access batteries and replace worn components, or completely recycle battery stacks for recovery of cobalt, lithium, metal foils and other materials, the first step is battery diagnostics for safe and efficient handling and disassembly.
“With our system, when the robot picks up the battery pack and puts it on the production line, it marks the last time a human will touch it until it’s in pieces and parts,” McIntyre said.
Limiting human interaction is important for both safety and efficiency. The robots swiftly remove bolts and other housing regardless of any remaining charge, whereas human operators must undertake an exacting, lengthy process to discharge used batteries before breaking them down manually. Automated disassembly reduces human exposure to toxic chemicals found inside the batteries and high power levels that are approaching the 900-volt level in some newer vehicles.
The automated system, developed as part of DOE’s Critical Materials Institute, or CMI, can be easily reconfigured to any type of battery stack. It can be programmed to access just the individual battery modules for refurbishment or reuse as stationary energy storage, or the batteries can be taken apart down to the cell level for separation and materials recovery.
The work builds on expertise developed in previous ORNL projects for the CMI that focused on robotic disassembly of hard drives for recovery of rare-earth magnets. Engineers also proved that those magnets can be directly reused in electric motors.
“Automatic disassembly of components containing critical materials not only eliminates labor-intensive manual disassembly, but provides for an efficient process to separate the components into higher value streams where the critical materials are concentrated into individual feedstocks for recycle processing,” said CMI Director Tom Lograsso. “This added value is an important part of establishing an economically viable process.”
The researchers follow the same protocol each time: breaking down the used component manually and collecting data on that process to create the robotic tools and controls needed to drive an automated system, said ORNL project team member Jonathan Harter.
“Industry is not limited on the amount of batteries they can take into this process. There is a significant backlog already accumulated. The limiting factor is the time it takes to perform the electrical discharge and perform disassembly manually,” Harter said. He estimated that in the time it takes in some processes to disassemble 12 battery stacks by hand, the automated system could handle 100 or more.
The next step could be building the process up to commercial scale, and McIntyre’s team also see opportunities to apply the same kind of disassembly system to electric vehicle drive trains for recovery of materials such as rare earth magnets, copper, steel and intact power electronics. To make recycling more economically feasible, it must be done at high throughput and be flexible enough to process multiple consumer products in a single facility, Harter said.
“If the electric vehicle market accelerates as expected in the next 10 to 20 years, we will need to address the waste stream issue and view these spent vehicles and batteries as central to the supply chain for manufacturing materials,” he said.
The system was developed and demonstrated at ORNL’s Grid Research Integration and Deployment Center.
The Critical Materials Institute is a Department of Energy Innovation Hub led by DOE’s Ames Laboratory and supported by the Office of Energy Efficiency and Renewable Energy’s Advanced Manufacturing Office, which works to catalyze research, development, and adoption of energy-related advanced manufacturing technologies and practices to drive U.S. economic competitiveness and energy productivity. CMI seeks to accelerate innovative scientific and technological solutions to develop resilient and secure supply chains for rare-earth metals and other materials critical to the success of clean energy technologies.
UT-Battelle manages ORNL for Department of Energy’s Office of Science, the single largest supporter of basic research in the physical sciences in the United States. The Office of Science is working to address some of the most pressing challenges of our time. For more information, please visit energy.gov/science.
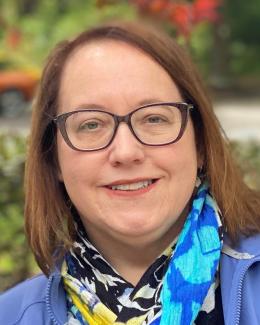