This newly manufactured fixed guide vane of a hydropower turbine system was printed at the DOE Manufacturing Demonstration Facility at ORNL. Credit: Genevieve Martin/ORNL, U.S Dept. of Energy
Over 100 years ago, the hydropower industry, which today generates 32% of all U.S. renewable energy, was built using traditional manufacturing processes. But surging energy demand, higher material costs, and supply chain hurdles have led researchers to rethink the manufacturing of hydropower equipment.
A new report published by Oak Ridge National Laboratory assessed how advanced manufacturing and materials, such as 3D printing and novel component coatings, could offer solutions to modernize the existing fleet and design new approaches to hydropower.

For the assessment, ORNL brought together representatives from the hydropower industry, advanced manufacturing industries, research institutions and groups committed to environmental stewardship.
Their collaboration identified existing infrastructure challenges and ways in which advanced manufacturing could enhance new design capabilities, improve system and component performance, reduce reliance on foreign manufacturing and better address environmental concerns.
“Hydropower has enormous potential in securing a cleaner, more sustainable energy future,” said ORNL’s Mirko Musa. “We can build upon its success, layer by layer.” — Mimi McHale
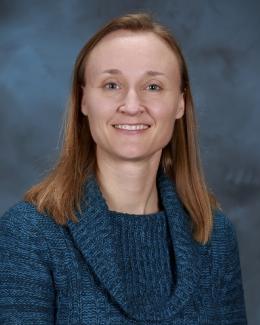