Filter News
Area of Research
- (-) Advanced Manufacturing (3)
- (-) Isotope Development and Production (1)
- Biological Systems (1)
- Biology and Environment (108)
- Biology and Soft Matter (1)
- Building Technologies (3)
- Clean Energy (112)
- Computational Biology (1)
- Computational Engineering (1)
- Computer Science (3)
- Electricity and Smart Grid (2)
- Energy Sciences (1)
- Fuel Cycle Science and Technology (1)
- Functional Materials for Energy (2)
- Fusion and Fission (34)
- Fusion Energy (3)
- Isotopes (18)
- Materials (119)
- Materials Characterization (2)
- Materials for Computing (6)
- Materials Under Extremes (1)
- National Security (51)
- Neutron Science (46)
- Nuclear Science and Technology (2)
- Renewable Energy (1)
- Supercomputing (112)
News Type
Media Contacts
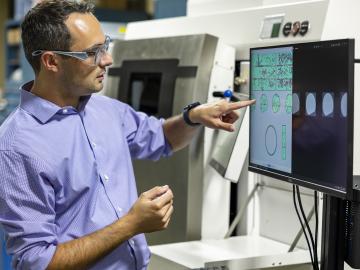
Researchers at the Department of Energy’s Oak Ridge National Laboratory have improved flaw detection to increase confidence in metal parts that are 3D-printed using laser powder bed fusion.
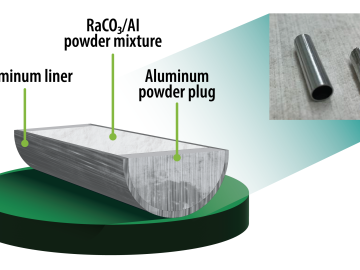
Oak Ridge National Laboratory researchers have developed a method to simplify one step of radioisotope production — and it’s faster and safer.
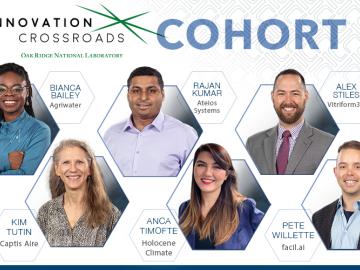
Oak Ridge National Laboratory’s Innovation Crossroads program welcomes six new science and technology innovators from across the United States to the sixth cohort.
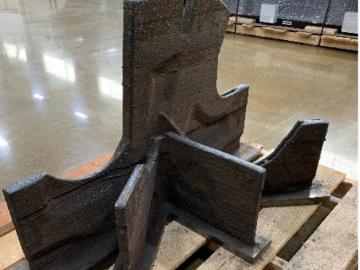
Oak Ridge National Laboratory researchers recently used large-scale additive manufacturing with metal to produce a full-strength steel component for a wind turbine, proving the technique as a viable alternative to