Filter News
Area of Research
News Topics
- (-) Fossil Energy (4)
- (-) Transformational Challenge Reactor (3)
- 3-D Printing/Advanced Manufacturing (34)
- Advanced Reactors (8)
- Artificial Intelligence (43)
- Big Data (21)
- Bioenergy (48)
- Biology (56)
- Biomedical (28)
- Biotechnology (10)
- Buildings (17)
- Chemical Sciences (21)
- Clean Water (14)
- Climate Change (46)
- Composites (5)
- Computer Science (80)
- Coronavirus (17)
- Critical Materials (1)
- Cybersecurity (14)
- Decarbonization (43)
- Education (1)
- Emergency (2)
- Energy Storage (28)
- Environment (100)
- Exascale Computing (24)
- Frontier (23)
- Fusion (28)
- Grid (23)
- High-Performance Computing (42)
- Hydropower (5)
- Isotopes (25)
- ITER (2)
- Machine Learning (21)
- Materials (39)
- Materials Science (41)
- Mathematics (5)
- Mercury (7)
- Microelectronics (2)
- Microscopy (20)
- Molten Salt (1)
- Nanotechnology (16)
- National Security (33)
- Net Zero (8)
- Neutron Science (46)
- Nuclear Energy (52)
- Partnerships (13)
- Physics (26)
- Polymers (7)
- Quantum Computing (17)
- Quantum Science (27)
- Renewable Energy (1)
- Security (10)
- Simulation (29)
- Software (1)
- Space Exploration (12)
- Summit (30)
- Sustainable Energy (42)
- Transportation (27)
Media Contacts
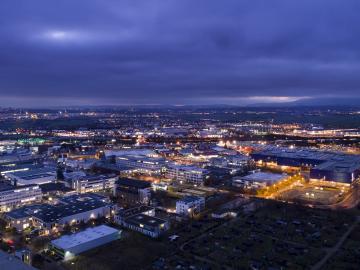
Scientists at Oak Ridge National Laboratory and six other Department of Energy national laboratories have developed a United States-based perspective for achieving net-zero carbon emissions.

SkyNano, an Innovation Crossroads alumnus, held a ribbon-cutting for their new facility. SkyNano exemplifies using DOE resources to build a successful clean energy company, making valuable carbon nanotubes from waste CO2.
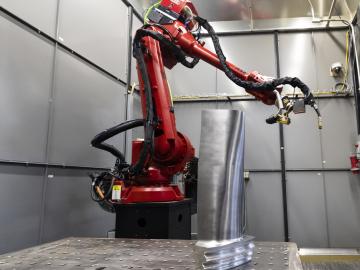
Researchers at ORNL became the first to 3D-print large rotating steam turbine blades for generating energy in power plants.
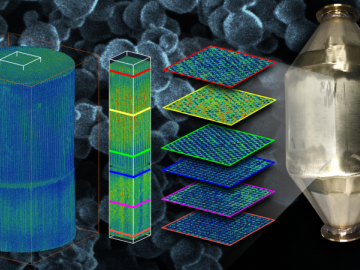
Natural gas furnaces not only heat your home, they also produce a lot of pollution. Even modern high-efficiency condensing furnaces produce significant amounts of corrosive acidic condensation and unhealthy levels of nitrogen oxides
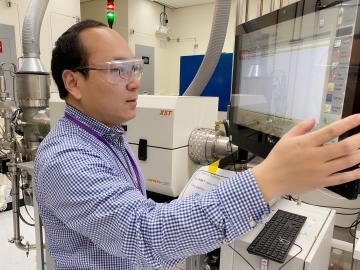
About 60 years ago, scientists discovered that a certain rare earth metal-hydrogen mixture, yttrium, could be the ideal moderator to go inside small, gas-cooled nuclear reactors.
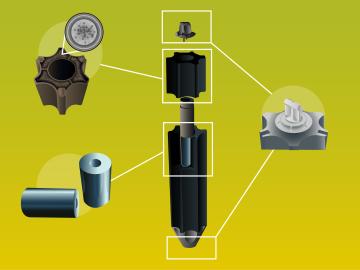
It’s a new type of nuclear reactor core. And the materials that will make it up are novel — products of Oak Ridge National Laboratory’s advanced materials and manufacturing technologies.
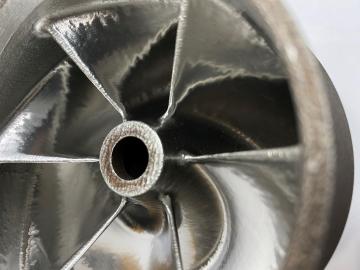
Scientists at the Department of Energy Manufacturing Demonstration Facility at ORNL have their eyes on the prize: the Transformational Challenge Reactor, or TCR, a microreactor built using 3D printing and other new approaches that will be up and running by 2023.