Filter News
Area of Research
News Topics
- (-) Composites (25)
- (-) Critical Materials (25)
- 3-D Printing/Advanced Manufacturing (116)
- Advanced Reactors (34)
- Artificial Intelligence (87)
- Big Data (50)
- Bioenergy (88)
- Biology (96)
- Biomedical (58)
- Biotechnology (21)
- Buildings (55)
- Chemical Sciences (60)
- Clean Water (29)
- Climate Change (94)
- Computer Science (184)
- Coronavirus (46)
- Cybersecurity (35)
- Decarbonization (75)
- Education (4)
- Element Discovery (1)
- Emergency (2)
- Energy Storage (107)
- Environment (192)
- Exascale Computing (36)
- Fossil Energy (5)
- Frontier (41)
- Fusion (53)
- Grid (61)
- High-Performance Computing (83)
- Hydropower (11)
- Irradiation (3)
- Isotopes (49)
- ITER (7)
- Machine Learning (46)
- Materials (141)
- Materials Science (136)
- Mathematics (6)
- Mercury (12)
- Microelectronics (2)
- Microscopy (51)
- Molten Salt (8)
- Nanotechnology (60)
- National Security (59)
- Net Zero (12)
- Neutron Science (130)
- Nuclear Energy (105)
- Partnerships (40)
- Physics (59)
- Polymers (31)
- Quantum Computing (31)
- Quantum Science (66)
- Renewable Energy (2)
- Security (24)
- Simulation (45)
- Software (1)
- Space Exploration (25)
- Statistics (3)
- Summit (57)
- Sustainable Energy (121)
- Transformational Challenge Reactor (7)
- Transportation (94)
Media Contacts
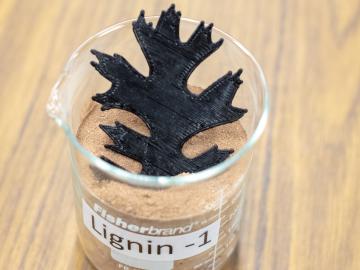
Scientists at the Department of Energy’s Oak Ridge National Laboratory have created a recipe for a renewable 3D printing feedstock that could spur a profitable new use for an intractable biorefinery byproduct: lignin.
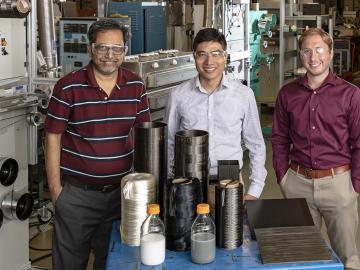
Carbon fiber composites—lightweight and strong—are great structural materials for automobiles, aircraft and other transportation vehicles. They consist of a polymer matrix, such as epoxy, into which reinforcing carbon fibers have been embedded. Because of differences in the mecha...
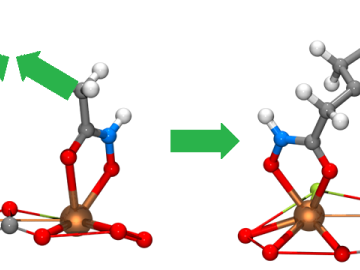
Scientists from the Critical Materials Institute used the Titan supercomputer and Eos computing cluster at ORNL to analyze designer molecules that could increase the yield of rare earth elements found in bastnaesite, an important mineral
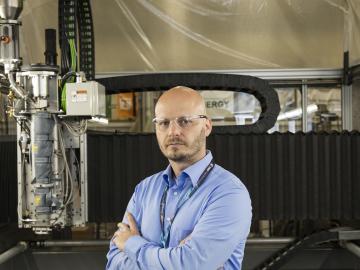
Vlastimil Kunc grew up in a family of scientists where his natural curiosity was encouraged—an experience that continues to drive his research today in polymer composite additive manufacturing at Oak Ridge National Laboratory. “I’ve been interested in the science of composites si...
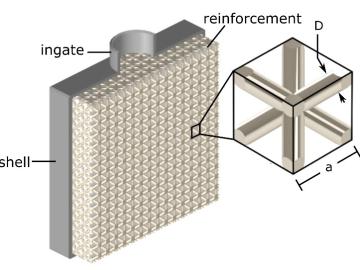
A new manufacturing method created by Oak Ridge National Laboratory and Rice University combines 3D printing with traditional casting to produce damage-tolerant components composed of multiple materials. Composite components made by pouring an aluminum alloy over a printed steel lattice showed an order of magnitude greater damage tolerance than aluminum alone.
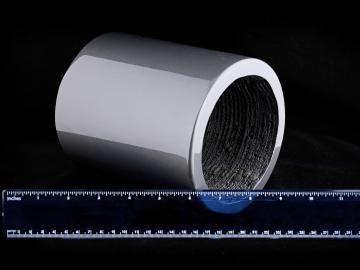
Researchers at the Department of Energy’s Oak Ridge National Laboratory have demonstrated that permanent magnets produced by additive manufacturing can outperform bonded magnets made using traditional techniques while conserving critical materials. Scientists fabric...
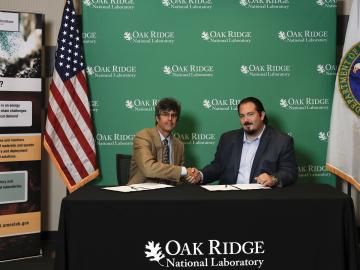
A process developed at Oak Ridge National Laboratory for large-scale recovery of rare earth magnets from used computer hard drives will undergo industrial testing under a new agreement between Oddello Industries LLC and ORNL, as part of the Department of Energy’s Crit...
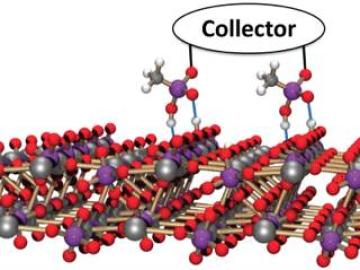
Ensuring a reliable supply of rare earth elements, including four key lanthanides and yttrium, is a major goal of the Critical Materials Institute (https://cmi.ameslab.gov) as these elements are essential to many clean-energy technologies. These include energy-efficient lighting, ...
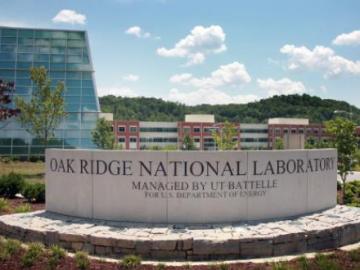
A new technology developed by the U.S. Department of Energy’s Critical Materials Institute that aids in the recycling, recovery and extraction of rare earth minerals has been licensed to U.S. Rare Earths, Inc.
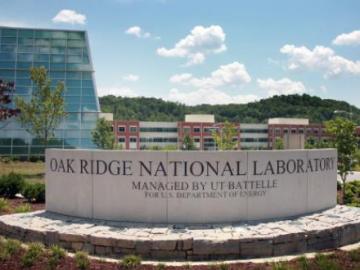
An alloy discovered at Oak Ridge National Laboratory holds great promise for permanent magnets as the material retains its magnetic properties at higher temperatures yet contains no rare-earth elements. This finding is significant because while rare-earth-based magnets are critical to alternative ...