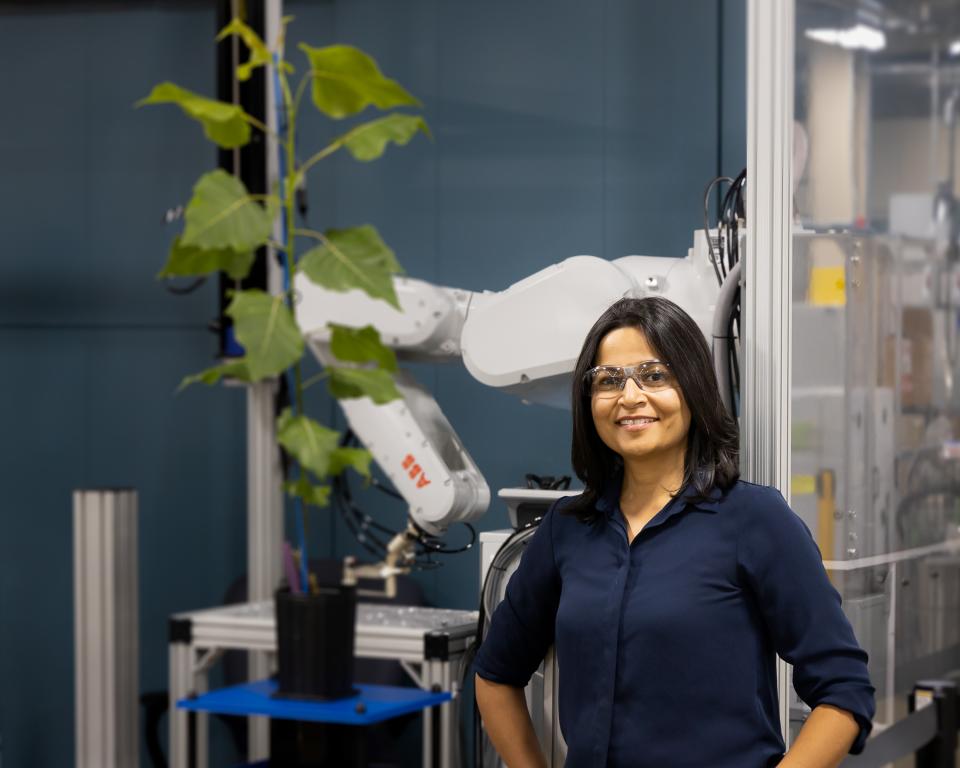
Scientists at the US Department of Energy’s Oak Ridge National Laboratory demonstrated proof of principle for a new automation system that harnesses artificial intelligence and robotics to quickly manipulate and sample living plants, accelerating efforts to optimize traits in bioenergy and agricultural crops.
The system, called Sensors, Machine vision, Automation and Robotics for Transforming Plants, or SMART Plant 1.0, performs key steps needed for plant transformation. During transformation, researchers transfer a gene of interest into a plant tissue sample, or explant, which is grown into a new plant. The new plant’s observable characteristics and responses, called phenotypes, are then studied to determine the effects of the added gene. This step is critical in the gene discovery process, but it is also a widely acknowledged bottleneck.
With advances in genomic technology, scientists can perform gene sequencing and analysis far more quickly than they can collect related data about how genes are expressed as phenotypes. To close this data gap, SMART Plant 1.0 is expected to boost throughput and accelerate the pace of plant transformation by 100 times.
“By enabling smart systems for predictive plant biology, we aim to drastically speed up the fundamental science driving the development of sustainable plant-based bioenergy, biomaterials and resilient plants that sequester carbon dioxide from the atmosphere,” said Udaya Kalluri, who led the development of SMART Plant 1.0.
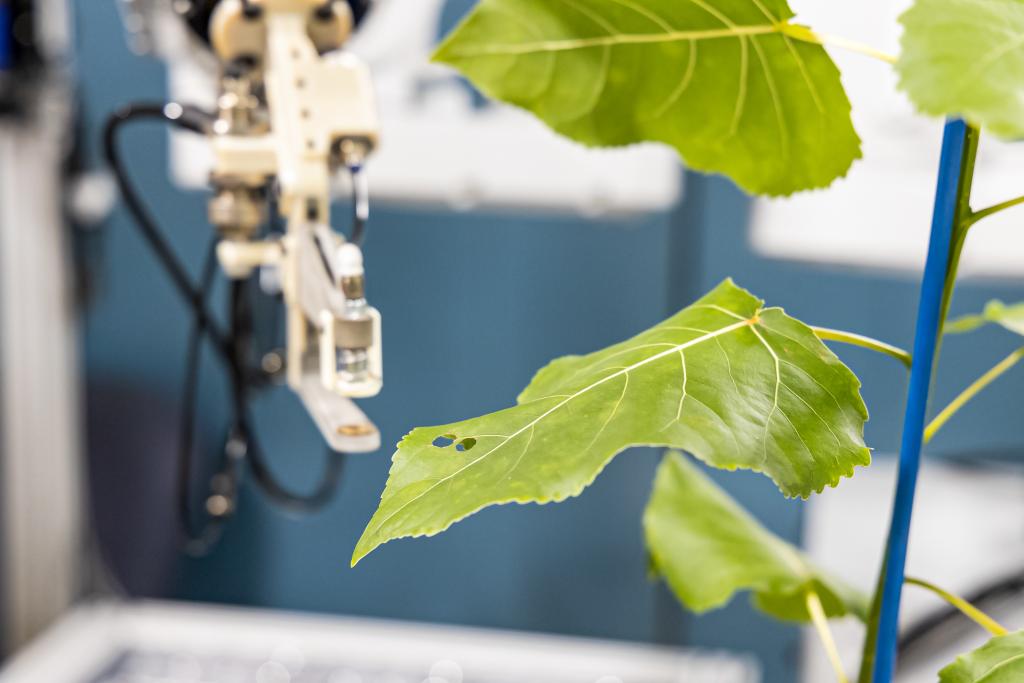
Robotic precision
When a plant is placed in front of SMART Plant 1.0, the system uses computer vision to scan the plant and glean data about leaf shape, color and size.
A robotic arm with an attached custom sampling tool then moves toward a suitable leaf. It adjusts and twists to achieve the correct orientation and pinpoints a specific location on the blade of the leaf.
Using the sampling tool, which resembles a hole punch, the robot precisely and consistently cuts out a small tissue sample. It then deposits the sample into a petri dish containing a biological medium needed to start the transformation process.
Although phenotyping systems that gather information through imaging are becoming more common, SMART Plant 1.0’s ability to not only image a plant but also physically manipulate and sample plant leaves is unique.
Our system has to read the plant’s 3D structure, determine which leaf to target, approach it at the correct angle, and then take a precise sample—for example, one that avoids the leaf’s vein and targets the blade of the leaf—and to do so reliably. That is a huge programming endeavor.
An interdisciplinary team of scientists and engineers conceived, developed and integrated SMART Plant 1.0 in house, which included 3D printing components of the robot’s cutting tool. Some components, including the robotic arm, were commercially manufactured but integrated into the system in novel ways.
As part of a second project, researchers are building another system—the SMART Plant G-series, or greenhouse series—to automatically read and manipulate plants of a wider height range. That robot will be integrated into ORNL’s Advanced Plant Phenotyping Laboratory, where conveyor belts move plants through a network of advanced imaging stations. The samples it collects will be used for a variety of measurements—not exclusively for transformation.
In the near future, the team envisions smart AI-driven measurement, monitoring and manipulation systems with added sensors for intelligent data collection and new edge computing capabilities for autonomously performing the entire transformation process in a controlled environment.
The ORNL research team includes Udaya Kalluri, Xiaohan Yang and Sara Jawdy of the Biosciences Division; Clay Leach, Vincent Paquit and Pooran Joshi of the Electrification and Energy Infrastructures Division; and Andrzej Nycz, Alex Walters and Lonnie Love of the Manufacturing Science Division.
SMART Plant 1.0 was supported by ORNL’s Laboratory Directed Research and Development fund. The invention is available for licensing through ORNL’s Technology Transfer office.
UT-Battelle manages ORNL for Department of Energy’s Office of Science, the single largest supporter of basic research in the physical sciences in the United States. The Office of Science is working to address some of the most pressing challenges of our time. For more information, please visit energy.gov/science. – Abby E Bower