Achievement: A multidisciplinary team of researchers from Oak Ridge National Laboratory (ORNL) and the University of Texas at Austin developed a new framework for assessing the accuracy of approximate models of microstructure formation during additive manufacturing and welding and applied it to a new multiscale approximate model. The new assessment framework consists of comparing microstructural quantities of interest from the approximate model to a computationally expensive dendrite-resolved, phase-field simulation of the entire melt pool for a spot melt. The new approximate model consists of a single-crystal phase-field simulation confined to a narrow spatial domain with solidification conditions taken from a curved path through the melt pool from a melt-pool-scale thermal simulation. Through the assessment framework, the new multiscale model was found to yield accurate results for four out of five quantities of interest across four test cases while requiring 200x fewer computational resources than the full-melt-pool simulations. For the quantity of interest with inconsistent accuracy, the full-melt-pool simulations provided insight for why the approximate model failed and highlighted the importance of one aspect of the solidification process (the influence of the shape of the melt pool on non-steady-state interactions between dendrites) that had previously attracted little attention. In summary, this work (1) demonstrates a new framework for testing approximate models of microstructure formation in additive manufacturing and welding, (2) presents a new approximate model of microstructure formation, (3) shows that this approximate model accurately predicts most quantities of interest, and (4) highlights the importance of long-range melt-pool shape on dendrite-scale features.
Significance and Impact: This work is the first systematic, quantitative comparison between the predictions of a full-melt-pool phase-field simulation and a phase-field-based multiscale simulations. It demonstrates a new framework for developing and assessing approximate models of microstructure formation during additive manufacturing and welding – using a full-melt-pool, dendrite-resolved phase-field simulation as the reference solution. Historically, full-melt-pool simulations have been rare, even in 2D as in this work, due to computational cost, but advances in computing make these simulations more computationally tractable. A simulated, high-fidelity reference solution provides the full spatial and temporal evolution of the microstructure under precisely known solidification conditions, thereby permitting a rigorous calculation of the error introduced by approximations in simplified models. This work, both through the new assessment framework and through its new approximate model, is a step toward computationally tractable high-fidelity microstructure predictions that can be used to understand and optimize the material properties for additively manufactured components.
Research Details
- The same phase-field model for the solidification of a dilute binary alloy (Al-Cu) was used for both the full-melt-pool model and for the dendrite-scale micro-model in the multiscale scheme. Phase-field models are typically regarded as the highest fidelity method for modeling solidification microstructures.
- The phase-field models were one-way coupled with a non-computationally intensive melt-pool-scale thermal model.
- For the approximate multiscale model, the phase-field micro-model was solved in a small rectangular domain with the thermal gradient and solidification velocity taken from a curved path (“solidification lines”) through the melt pool perpendicular to the thermal gradient during solidification.
- The phase-field model was implemented using the finite difference method with forward Euler time integration. The simulations were performed on NVIDIA V100 GPUs, with up to 16 GPUs being used for full-melt-pool simulations.
- Going forward, the results of the approximate model can either be used directly or for the rapid generation of parametric simulation data that could be used for subsequent development of an even less computationally intensive reduced order model (e.g. via a neural network).
Sponsor/Funding: DOE ASCR (AEOLUS Center)
ORNL lead researcher and affiliation: Stephen DeWitt, Scalable Algorithms and Coupled Physics Group, Computational Sciences and Engineering Division, ORNL
Team: Yigong Qin (UT-Austin), Yuanxun Bao (UT-Austin), Stephen DeWitt (ORNL), Balasubramaniam Radhakrishnan (ORNL), George Biros (UT-Austin)
Citation and DOI: Y. Qin, Y. Bau, S. DeWitt, B. Radhakrishnan, G. Biros. Dendrite-resolved, full-melt-pool phase-field simulations to reveal non-steady-state effects and to test an approximate model, Computational Materials Science, 207, 111262 (2022); DOI: 10.1016/j.commatsci.2022.111262
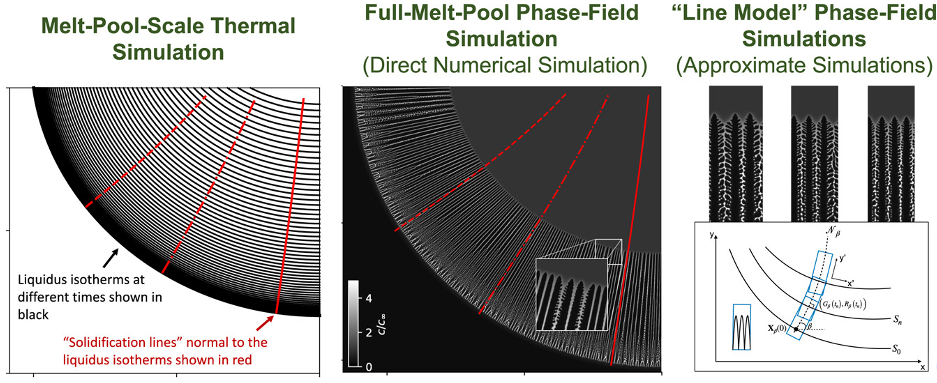
Summary: The dendrite-scale solidification microstructure plays an important role in the properties of metal alloys. Understanding and controlling these microstructural features during additive manufacturing is of significant scientific and technological interest. This work demonstrates a new framework to assess the accuracy of approximate models of dendrite-scale microstructure formation, as well as a new multiscale approximate model. With dendrite-resolved, full-melt-pool simulations used as reference solutions, the new multiscale model is shown to accurately describe four out of five quantities of interest while being 200x less costly than the reference solution. The full-melt-pool models provide insight for why the fifth quantity of interest (the primary dendrite arm spacing) is inconsistent in accuracy – it can be strongly influenced by the long-range curvature of the melt pool, an effect ignored in the multiscale model.