Achievement:
Simulations of Inconel 625 microstructure development and constitutive properties during Selective Laser Melting processing were performed utilizing two exascale-capable codes on the pre-exascale Summit supercomputer. ExaCA, a cellular automata-based model of nucleation and dendritic grain growth, was deployed to model microstructure development for a part built with a raster pattern and 90 degree layer rotation. ExaConstit, a crystal plasticity finite element model of constitutive properties, was used to obtain mechanical response data for selected representative volume elements (RVEs) from ExaCA microstructures. ExaCA simulations were initialized using various substrate grain sizes and nucleation densities, as well as various random seeds to generate statistically equivalent substrate and nucleation conditions for a given substrate grain size and nucleation density. Similar 001-dominated textures were observed for all microstructures, though the increase in grain area as a function of build height had a notable dependence on the substrate condition and nucleation density. RVEs were taken from simulations with various nucleation densities and substrate grain sizes and from two build heights in the simulated part to examine the differences in ExaConstit-modeled mechanical behavior. Despite differences in grain area for different nucleation density, substrate grain size, and build height, similar stress-strain and triaxiality behavior was observed for all RVEs, with predicted yield stress values for a given RVE within 6% of the predicted value for any other RVE.
Significance and Impact:
Large-scale microstructure and mechanical response simulations were performed to examine the impact of an initial condition (substrate grain structure) and a boundary condition (heterogenous nucleation density in the undercooled melt pool liquid) on layerwise grain structure development during Selective Laser Melting (SLM). While similar cellular automata (CA) based simulations of grain structure development during additive processing have previously been carried out and coupled to models of constitutive properties, the quantitative impact of the highly uncertain substrate condition and nucleation density on grain structure and mechanical properties had not previously been examined. The conclusion that reasonable estimations for substrate and nucleation conditions can, after around 15 layers of simulation of this scan pattern, produce qualitatively similar microstructures (despite differences in average grain area), quantitatively similar textures, and reasonable similar yield behavior and triaxiality, will be important for further studies modeling uncertainty in SLM process-microstructure-property relationships. The scale of the present microstructure simulations (over 700 million cells in each of over a dozen ExaCA simulations), and the fact that the simulations could be run in less than six hours on no more than six nodes of Summit, is a significant accomplishment relative to previous CA-based AM solidification simulations using other codes. The utilization of pre-exascale resources (and eventually, exascale hardware) will allow for future, even larger scale uncertainty analysis with the incorporation of uncertainty in process modeling.
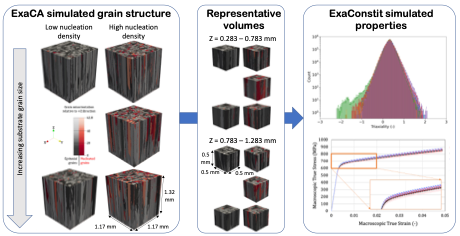
Research Details
- Cellular automata (CA) simulations of Selective Laser Melting (SLM) grain structure were performed using ExaCA, with input time-temperature history data generated using the computational fluid dynamics model OpenFOAM
- Simulations of 65 layers of microstructure were performed using time-temperature data for a raster pattern with 90 degree rotation (i.e., an “even” layer with scans in the X direction, and an “odd” layer with scans in the Y direction). Nucleation density was originally fixed at 1013 m-3, and mean substrate grain size at 45 µm, to examine the uncertainty in layerwise microstructure development from statistically equivalent sets of grain locations, orientations, and nucleation undercooling values. Mean grain area and mean weighted grain area were calculated as a function of build height
- After quantification of statistical variation in grain structure at a fixed nucleation density and substrate grain size, nucleation density values from 1012 through 1014 m-3, and mean substrate grain sizes from 25 to 65 µm were used to investigate mean grain area and mean weighted grain area versus build height, along with texture
- Representative volume elements (RVEs) from the center of the ExaCA simulations in X and Y, and two different build heights (“lower” RVEs encompassing layers 15-39, and “upper” RVEs encompassing layers 40-64), two different nucleation densities (1012 and 1013 m-3), and three different mean substrate grain sizes (25, 45, and 65 µm) were extracted and used by ExaConstit to generate stress-strain curves, quantify yield stress, and determine triaxiality distributions
- 120 layer ExaCA microstructure simulations, using extremes in substrate conditions (single crystals with near-001 and 111 orientations, and the minimum possible grain size) and fixed nucleation density 1013 m-3, were performed to quantify texture discrepancies in the top 30 layers of microstructure
Facility: ExaCA and ExaConstit simulations were performed using the Summit supercomputer at the OLCF.
Sponsor/Funding: Exascale Computing Project/ExaAM
PI and affiliation: John Turner, Computational Engineering Program Director, ORNL, and Jim Belak, Senior Scientist, LLNL
Team: Matthew Rolchigo (ORNL), Robert Carson, (LLNL), Jim Belak (LLNL)
Citation and DOI: M. Rolchigo, R. Carson, and J. Belak. Understanding uncertainty in microstructure evolution and constitutive properties in additive process modeling, Metals, 12, 2 (2022); DOI: 10.3390/met12020324
Summary:
Modeling of process-microstructure-property relationships, along with uncertainty associated with the models, is an important step towards utilization of additive manufacturing (AM) for predictable printing of alloys. While many studies have attempted to model AM processes, microstructure development, and constitutive properties, few studies have considered the role of uncertain inputs or physics on the model results, and propagation of said uncertainties between models. Using the ExaCA model of nucleation and dendritic growth, developed as part of the Exascale Computing Project and run on the pre-exascale Summit supercomputer, large-scale grain structures were generated using various substrate and nucleation conditions to explore their roles on grain size and texture development as a function of build height. Representative volume elements from two build heights within ExaCA simulations initialized with various substrate grain sizes and nucleation densities were passed to ExaConstit, which simulated stress-strain and triaxiality behavior. The simulated microstructures were qualitatively similar and had similar textures after the first 15 layers of build, and the constitutive properties were similar as well. This information on microstructure and property model sensitivity to nucleation, substrate, and build height will be important when developing future, more detailed uncertainty quantification with additive process, microstructure, and constitutive property models.