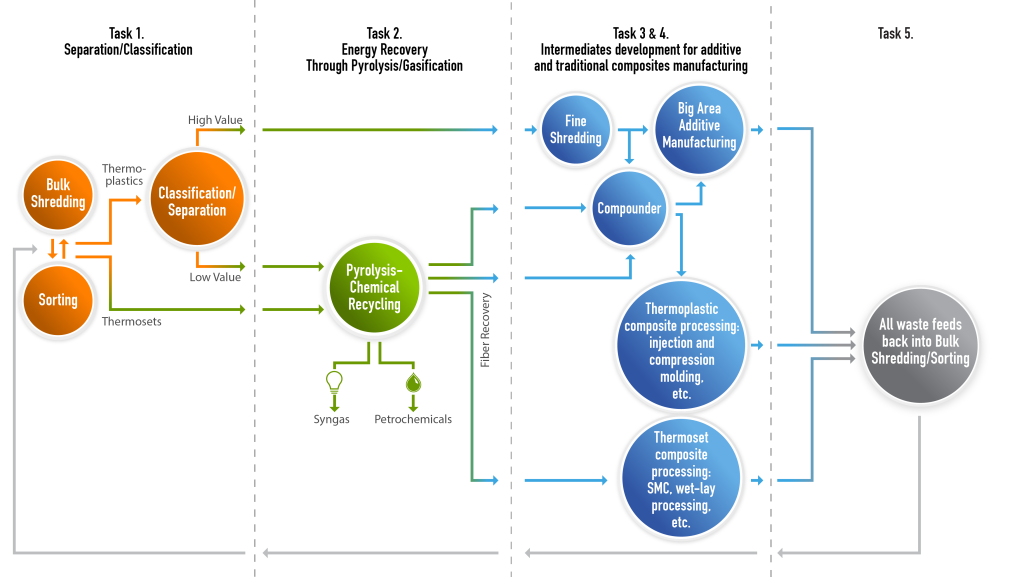
Circular Economy
Recovery and Recycling of Advanced Manufacturing Materials
The US Department of Energy (DOE) Manufacturing Demonstration Facility at Oak Ridge National Laboratory (ORNL) is working with industry to replace material disposability with renewability.
ORNL’s research focuses on closing the loop on the modern material supply chain so that today’s composite waste materials that are a by-product of advanced manufacturing processes become tomorrow’s valuable raw materials. Researchers are deploying new processes that convert feedstocks used in advanced manufacturing into reusable materials.
According to DOE, 5.7 billion metric tons of discarded plastic have never been recycled. The vast amount of discarded waste presents a critical need for new technology in the area of plastics recycling. In addition, Environmental Protection Agency (EPA) data indicated that 75% of plastic waste is sent to landfills, representing almost one-fifth of all landfilled solid waste, with the rest incinerated.
Despite the need, recycling composited polymer (plastic) waste is challenging because polymer materials contain many types of fiber reinforcement to enhance mechanical performance. Many of these composite materials are also made using thermoset polymers such as epoxy that cannot be remolded like other plastics making the recycling process even more difficult.
ORNL addresses these challenges by focusing on recycling materials from the following advanced manufacturing processes:
- Big Area Additive Manufacturing (BAAM)
- Injection Molding
- Compression Molding
- Sheet Molding Compounding
- Thermoset Additive Manufacturing
- Prepeg Molding
Research involves developing methodology for processing recycled fibers with recycled resin systems to produce nonwoven and reinforced thermoplastics and converting thermoplastic into materials that can be fed into manufacturing processes. Existing compounding and textile tools are being adapted and shredding and pelletizing equipment modifications are being made to produce optimized feedstocks conducive to recycling.
New techniques to repurpose one-time single use polymers, resins and plastics include pyrolysis and chemical recycling; classification and separation; bulk shredding and sorting; and compounding.
ORNL researchers are also exploring many avenues for creating a circular process for composite materials including converting recycled carbon into automotive panels and using reclaimed polycarbonate waste with bamboo to create structures such as an additively manufactured utility pole.
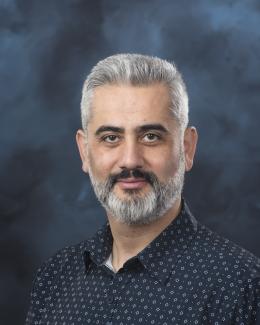