Lightweight Metals Processing
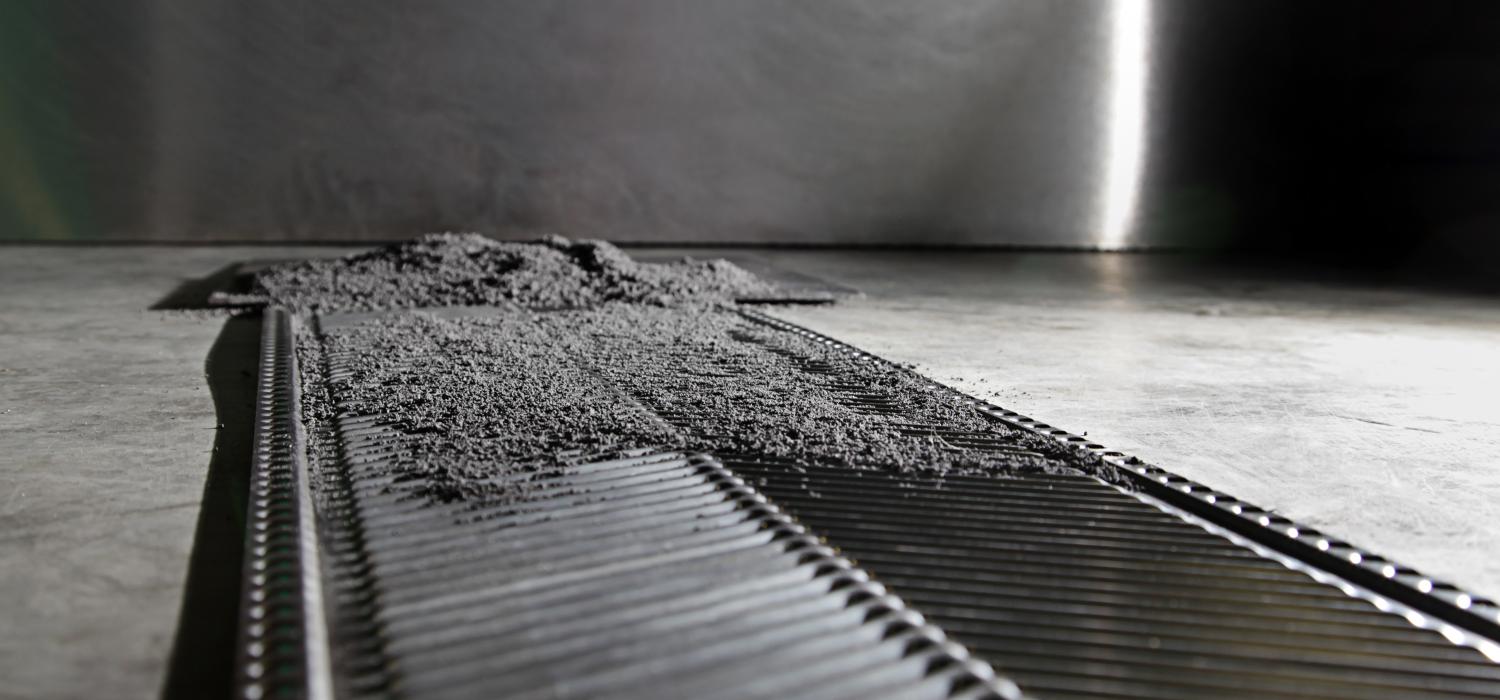
The objective of the current work is to develop feedstock material guidelines, information, and/or specifications to improve the supply chain integration and broaden the use of lightweight metals in Additive Manufacturing (AM) technologies. R&D in this Focus Area can determine the powder qualities (i.e., chemistries, size distribution, morphologies, etc.) required for making successful components meeting or exceeding traditional manufacturing technology properties, and will investigate alternative starting materials to decrease the overall cost and energy consumption for making AM components. Economic and consistent feedstock material specifications are required before AM can be pervasive in developing energy efficient systems.
This MDF work can enable AM equipment manufacturers and feedstock material suppliers to provide required powder morphologies and size distributions, chemistries, and material sources to meet final component properties fabricated from AM technologies. The information can be used for the development of guidelines, standards, specifications, and/or qualifications, such as the ASTM F42 Committee, to enable broader use of the AM technology. Additive manufacturing has the potential to create energy efficient designs and components not previously possible for both renewable energy and energy efficient systems once supply issues, qualifications, and equipment shortcomings are solved.
Additive manufacturing technology advancements are moving faster than the supply chains, design, and qualification to support the commercialization of these technologies. AM has used commercially available feed materials to fabricate components without a method or support of optimizing chemistries and/or material properties. Historically, materials for welding have had their own chemistry and property specifications that have been different than the parent material due to the potential to pickup or lose certain elements during the process. Additive manufacturing is a fusion process as well, and therefore, will require unique specifications and qualifications to meet required properties for application. Furthermore, the energy source (ie., electron beam, plasma, laser, etc.) and equipment design of AM vary between vendors resulting in further potential outcomes.
Additive manufacturing has the potential to create energy efficient designs and components not previously possible for both renewable energy and energy efficient systems. However, new supply chains and feedstock providers (i.e., powder, particulates, wire, sheet) with ample production rates are required for commercialization of large scale additive manufacturing with high deposition rates and/or the potential for high volume components. This Focus Area can perform research and development in the areas of potential feedstock material suppliers, determining required morphologies, geometries, and chemistries to meet build and mechanical criteria, and develop modified AM processing criteria to establish economical and energy efficient builds.