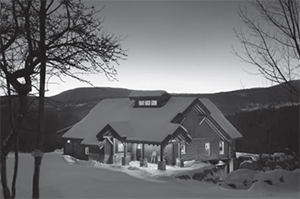
In Practice
A Conversation with Linda LaCroix, Aspen Construction Services
“If you ask five people what sustainability means to them, you’ll get five different answers, but if you ask what makes a building sustainable, you may just get the same answer – energy efficiency,” began Linda L. LaCroix, Partner at Aspen Construction Services and Vermont State Representative to the National Association of Home Builders® (NAHB). “One way to understand sustainability is as a capacity to maintain existing conditions over time. Resilience may be more what we are after – resilience might mean the capacity to create synergies over time. The way to do that is to think of buildings as systems that interact with people and with nature – the primary systems being architectural and site design, use planning, the building envelope and interior spaces, air, water and thermal systems, energy, waste and water services, and the building’s sustainability system,” explained LaCroix.
Aspen’s project portfolio includes the Roxbury House, a net-zero ready energy efficient log home in the Catskills region of Upstate New York (see Figure 9). The log home is certified under the NAHB Green Building Standard at the Gold Level, earned the Emerald Level in energy efficiency, achieved a Five Star Plus ENERGY STAR® rating, and met Department of Energy’s (DOE) Builders Challenge. Unique project details include a geothermal heating system that delivers the building’s domestic hot water, heating, and cooling energy. The system includes a high efficiency, modulating gas boiler back-up for below zero degree days. The first floor walls are framed with D-log, which feature doubletongues with foam gaskets for air sealing. The thirtyfoot high cathedral ceilings expose a dramatic view of the mountains: two floor to ceiling cypress trees built into the rear gable wall frame banks of windows and the French doors leading out to a stone patio (see Figure 10). Even with these challenges, the Roxbury House earned a HERS Rating Index of 48.
Figure 10. Roxbury embraces aesthetic beauty and design while still achieving performance. Photo courtesy Carolyn Bates.
“When you achieve balance in human, built, and natural environments, you deliver the highest value – a desirable and resilient building that preserves resources and capital,” emphasized LaCroix. “Good design and site planning can do so much to increase performance - to bring the energy load down: if you start with a building that requires less energy, its energy, waste, and water systems can be crafted from less resources, both when they go in, and over their lifetime. Careful consideration of materials, sources, and methods are at the heart of an economical and beneficial construction – you achieve a great deal of performance here, and the trick is to focus on best systems blends because you can create synergies between components.”
“For example, we incorporated a green roof in a great little Pavilion project that our company recently delivered. The roof stabilized the building, which means that it gives the building broader tolerances to changes in moisture. Wood moves less in a stable environment: if the moisture content dramatically increases or decreases, wood moves, splits, curls. Everything has energy, understanding how systems move energy through the building over time is the first step in achieving performance. It’s like Einstein said – if he had an hour to save the world, he would spend 59 minutes defining the problem and need only one minute to solve it,” said LaCroix.
“Yet, in an individual home, the answers to these questions are not always obvious,” said LaCroix. “Some of the improvements are not mechanical, or based on insulation levels; some improvements are in simple products.
Figure 11. D-log construction at the Roxbury House. Photo courtesy Aspen Construction Services.
The Roxbury House is an example of what can be achieved with a systems approach – one that brings design, building science, and services together, to achieve fabulous performance in what should be a low-performing structure – an 8” D-Log home. There are hundreds of details that contributed to a better result.” (See Figure 11.)
The Roxbury House has dovetailed corners that pull together over time instead of moving apart. The building envelope team improved thermal, air, and water performance prior to applying wall coverings by taking thermal images to uncover weaknesses in the envelope (see Figure 12), and the HVAC team worked with the mason and design team to smooth the effects of the mechanical kitchen hood and the air exchanges that are part of masonry structures – there are two masonry stone fireplaces in the home, one with a 54” opening (see Figure 13). Uneven air movement can impair the efficiency of air-sourced heating and cooling systems, but can aid in good airflow if considered during system design. The Roxbury House has both radiant heat and forced air distribution systems – radiant in the first floor deck coupled with an air source that delivers heating and cooling, and helps level out humidity levels (the system maintains a constant humidity). Two air ducts incorporated in to the large fireplace, behind two hand-forged iron grates, deliver targeted air flow to a north-facing corner. The energy recovery ventilation (ERV) system also plays an important part in gaining efficiencies for the two distribution systems.
Figure 12. Prior to finishing, the building envelope team took thermal images to find and fix any weaknesses in the envelope. Photo courtesy Aspen Construction Services.
The building’s thermal energy is principally fueled by a geothermal system supplied by three 500-foot vertical bores, spaced thirty feet apart. The system provides space heating and cooling with full hot water supply. Aspen worked with a geothermal equipment manufacturer from Canada to accept their first installation of a combined heat pump and air handler. “These kinds of partnerships benefit everyone,” offered LaCroix, “and are important pieces to testing systems in real environments. Plus, the investment from the manufacturer leads to a stronger working relationship.”
“Our customers get it,” said LaCroix. “We like pushing the edge with companies wanting to prove their innovations, and we enjoy the opportunity of installing things for the first time. We prefer to see each structure as a prototype of unique integrations. Even in production building, houses are individual labs; each is situated differently and has its own unique site conditions and opportunities.”
Figure 13. Thermal imaging of chimney heat transfer. Photo courtesy Aspen Construction Services.
“Combining space conditioning and hot water also created internal efficiencies,” summarized LaCroix. “The combo unit means that the mechanical system works less, reduces general wear and tear, takes up less space, uses less materials, and does more of what it is supposed to do, for less.” The Roxbury House features another innovation that changes the way radiant distribution systems are installed. GRAFIHX™, a graphite impregnated flexible cloth (see Figure 14) that conducts heat, is used to bolster the performance of the radiant floor heat distribution system. GRAFIHX comes in rolls, and can be easily cut. “In a typical radiant heating system, we create heat by running hot water through flexible tubing pushed through aluminum plates installed either underneath, or on top of the floor deck,” explained LaCroix. “The radiant floor tubing connects to the hot water source through circulator pumps.”
Figure 14. GRAFIHX™ a graphite impregnated flexible cloth, was used to boost radiant floor efficiencies. Photo courtesy Aspen Construction Services.
“If you were to take a thermal image of the tubes running through the floor, you would see two stripes of heat in the bay, and in between, a bunch of cold air. This is not a very efficient picture, as cold air in the bay fights with heated water in the tubes to equalize in temperature, meaning you need to compensate for the influence of the cold by running hotter water.” Instead, the GRAFIHX membrane allows the heat from the tubes to conduct throughout the floor bay.
The radiant tubing is free-stapled in the bays between a “sandwich” of GRAFIHX (see Figure 15). LaCroix explains, “The graphite material is a passive boost to performance because it spreads the heat outward from the tubing across the whole bay. This simple system allows us to lower the temperature of the water going through the tubes, and so outperforms traditional extruded aluminum plate systems. The materials cost about 50% less, and installation labor is a lot less because the worker doesn’t have to push the tubing through the rigid plates. Both short and long term goals are met.”
Figure 15. GRAFIHX™ in the installation, wrapped around radiant floor tubing to conserve heat. Photo courtesy Aspen Construction Services.
Next month, we’ll continue our conversation with LaCroix. To learn more about Aspen Construction Services, and to view videos documenting Roxbury’s construction, go to http://www.aspenvermont.com/portfolio_ item/roxbury-energy-efficient-log-home/.