Click here to read a static version.
In an autonomous chemistry laboratory on Oak Ridge National Laboratory’s main campus, a mobile robot shuttles between workstations, most of which have their own robots.
Guided by advanced artificial intelligence, the equipment — much of it custom-built — grabs chemicals and mixes them together. Sometimes it heats the mixtures in a furnace; at other times, it runs them through high-speed mixers. In either case, the new products are then sent to separate instruments for analysis.
Along the way, computers automatically collect all the information created in the process — information on what worked as well as what didn’t — which will be used to accelerate scientific understanding and to improve AI models.
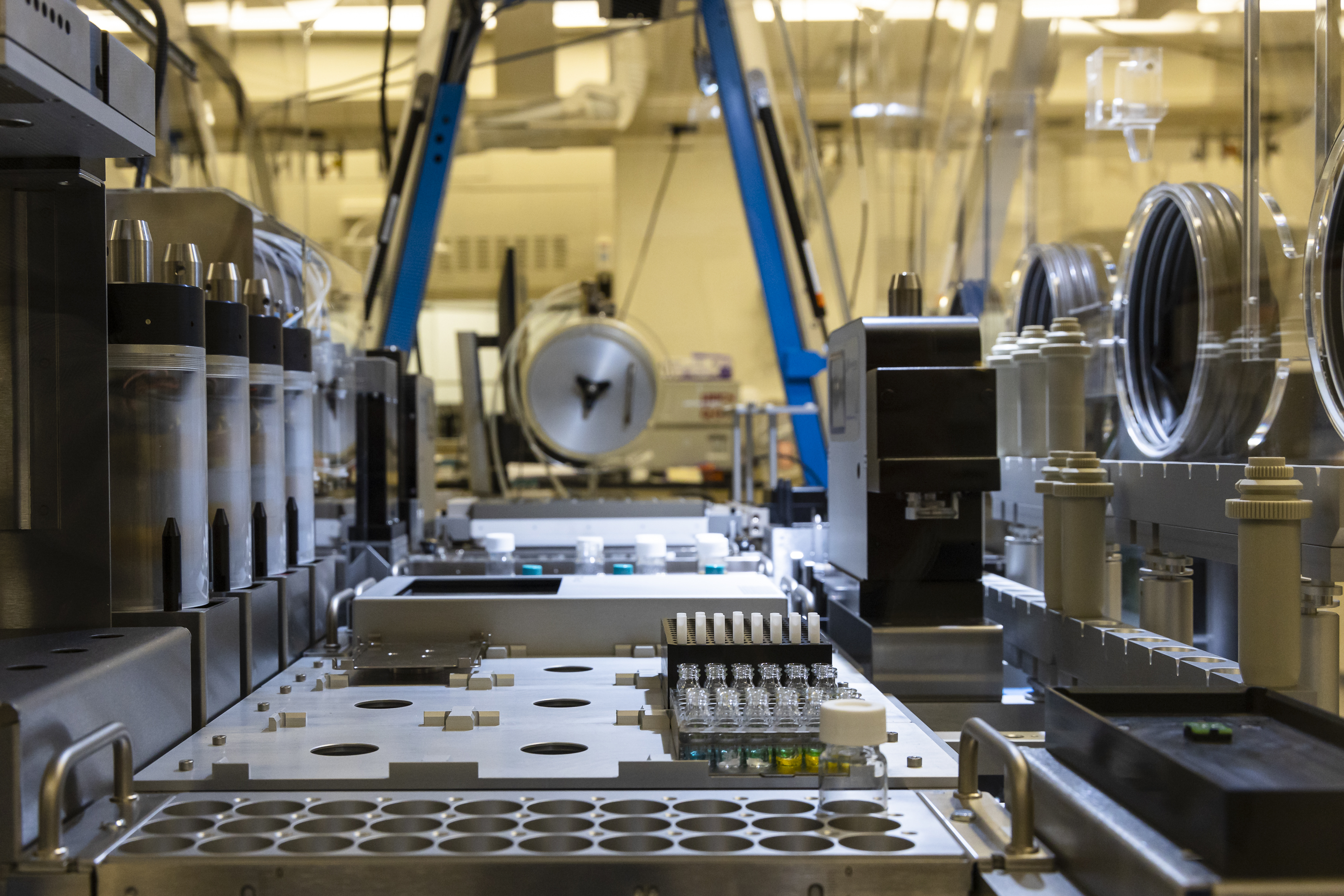
A quarter mile across ORNL’s main campus, a state-of-the-art electron microscope examines a tiny sliver of an ultrathin material such as graphene. Because the microscope is highly susceptible both to vibrations and to electric and magnetic fields, the AI-enabled computers that control it are located in a separate building.
Control algorithms tell the microscope to capture images of the 3-millimeter disk — about the width of two stacked pennies — and then zoom in on one or more areas that promise to yield useful information. These close-up images reveal intricate lattices of individual atoms, providing insight into the structure of the material, including atomic bonding and surface defects.

As with the autonomous chemistry lab, the computers collect and analyze a rising mountain of data while helping to manage the hundreds of gigabytes collected each day.
About 20 miles down the road at the lab’s Manufacturing Demonstration Facility, high-powered computers use simulation to control a 3D printer producing metal parts.
Networking + AI + unique capabilities = groundbreaking research
These autonomous laboratory projects and others across ORNL are connected to form the lab’s Interconnected Science Ecosystem — a labwide initiative launched in 2022 that aims to reimagine the way scientific research is performed.
The initiative, commonly referred to as INTERSECT, has two primary goals.
The first is to use AI, robotics, computer simulation, the lab’s networking expertise and other high-tech tools to reduce the time it takes to conduct research, taking experiments that typically take days or even years and completing them in minutes.
The second, more ambitious goal is to use these tools to deliver scientific breakthroughs that would be unachievable in traditional research settings.
“The vision of INTERSECT is to create a network of autonomous, self-driving smart laboratories that enable new multidomain scientific research,” said Ben Mintz, one of the initiative’s two co-directors.
Along the way, INTERSECT is streamlining the process of doing science by automating repetitive tasks and creating a standard set of software tools that can be used and adapted for seemingly dissimilar research endeavors.
If it’s real, it’s reproducible
On a practical level, the new processes are making the day-to-day business of conducting research both less tedious and more dependable.
For a working researcher, it’s not enough to do an experiment and get a result. You need to be able to repeat it and get the same result. In the words of INTERSECT’s other director, Rob Moore, “If it’s real, it’s reproducible.”
“Because of that, we end up doing a lot of things over and over and over again,” Moore said. “We'll run experiments with slightly different parameters to figure out what’s real and what's not. We'll run theoretical calculations with slightly different parameters to see what's reliable and what's not.”
The repetition is critical, but it can also be mind-numbingly dull. It’s also a process that hasn’t changed for many decades.
“Chemistry labs haven't gone through much of a revolution,” said Sheng Dai, who leads the autonomous chemistry lab. “Current labs are the same to some extent as we had 40 years ago. Our overarching goal is to develop a more smart lab.
“There's a lot of advantage to doing this. Number one, we can do an experiment very safely; there's no human error. And number two, the experiment can be done efficiently, because the robots can work 24/7 — and in the dark.”
These projects have more in common than you might think
INTERSECT has shown that automation, AI and interoperability can supercharge the full gamut of scientific research. Other INTERSECT projects include the following:
Improving the hit-or-miss process of creating quantum materials
If you sandwich the right materials together under the right conditions, the place where they meet becomes a powerful quantum device.
The challenge, of course, is in finding the right materials and the right conditions, a genuine needle-and-haystack endeavor. Theory promises great advances with the right sandwich — known as a quantum heterostructure — but the process of finding the right recipe can be daunting.
“So far, we have never constructed a single perfect quantum heterostructure in the way that we had imagined we should,” said Ganesh Panchapakesan, lead researcher for the INTERSECT quantum materials project.
Panchapakesan and colleagues are incorporating INTERSECT’s networking tools with state-of-the-art computer simulation and materials synthesis to speed and improve the process.
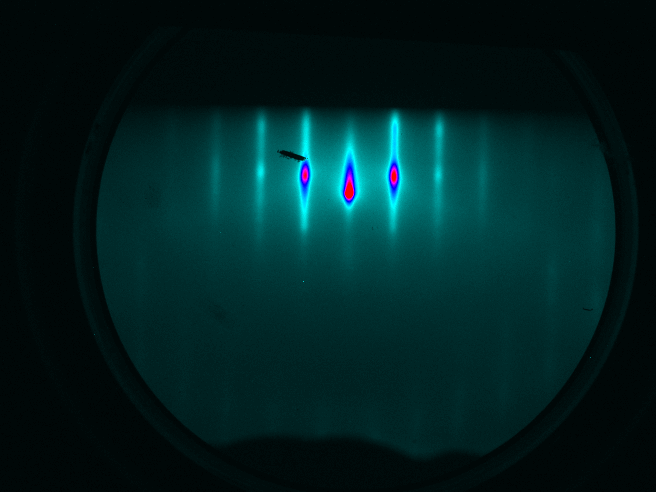
“There is a wealth of knowledge over years that is captured in how accurately we can simulate properties of materials and their formation,” he said. “Harnessing this knowledge should help us achieve truly autonomous synthesis.”
Before they grow a new material, the researchers use ORNL’s Frontier supercomputer to run simulations that create what are known as digital twins of the growth process while capturing signatures of this process in experimental measurements.
Using advanced automated workflows as well as AI and machine learning algorithms, the digital twins identify potential candidates for new heterostructures and discover the right conditions for making them using simulations of the growth process. The goal is to reduce the number of relatively slow and expensive physical experiments needed to create a new material by 80% or more, greatly reducing the time and cost of realizing new quantum heterostructures.
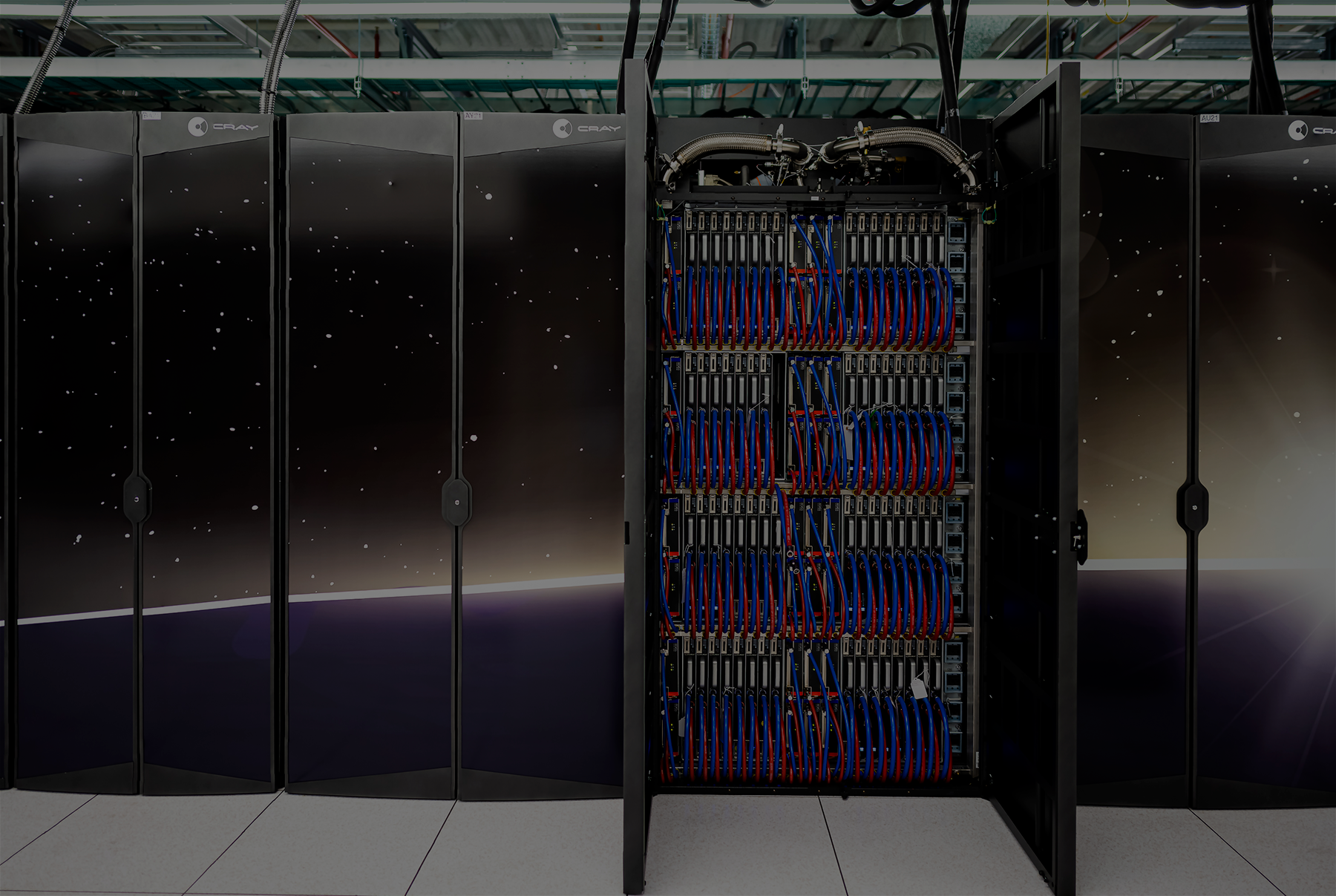
“We can get very strong or high-performance properties by controlling the sequence and the gradient of copolymerization,” explained Rigoberto Advincula, the project’s principal investigator. “You cannot do this easily by just mixing them or doing them in a batch.”
Advincula noted that the lab can easily be turned into a small production facility. It can also be used to automate formulation development or isotope separation and enrichment.
“If a machine is both an optimizer and a manufacturer,” he said, “then in one setup we basically have a factory in the laboratory that can produce products as long as we continually feed reactants to the beast.”
Bringing environmental research into the future
Like other scientific endeavors, plant and ecology researchers collect a mountain of data — on soil temperature and moisture levels, concentrations of elements in air and water, the presence of microbes in the soil, the list goes on. To date, such data has been collected by hand, a labor-intensive process.
ORNL researchers are working with INTERSECT to bring AI and automation to projects ranging from creating efficient biofuel crops to analyzing and anticipating the health of large ecosystems.
It’s all about the data
A common thread throughout INTERSECT’s projects is their reliance on AI, sophisticated modeling, advanced experimental capabilities and a thorough understanding of the ever-growing generation of data. This increasing volume of data necessitates the development and integration of state-of-the-art tools.
“Microscopy has had a data revolution in the past few years,” said Debangshu Mukherjee, who leads the electron microscopy project, “and one of the major reasons it got revolutionized was the introduction of a new generation of detectors.”
As a result, the amount of data collected by these instruments has exploded. The size of a single image, Mukherjee said, has grown by three orders of magnitude, ballooning from 4 megabytes to 4 gigabytes, and the output of one day’s work can reach 400 gigabytes.
“The way we used to collect our datasets,” he said, “was a microscopist would prepare the samples, insert the samples inside the microscope, sit on the microscope, collect as much data as they can, then insert flash drives, take out the data, go to their laptop and then start analyzing the data.
“That does not work for advanced experiments that generate so much data. We need to be processing data in real time.”
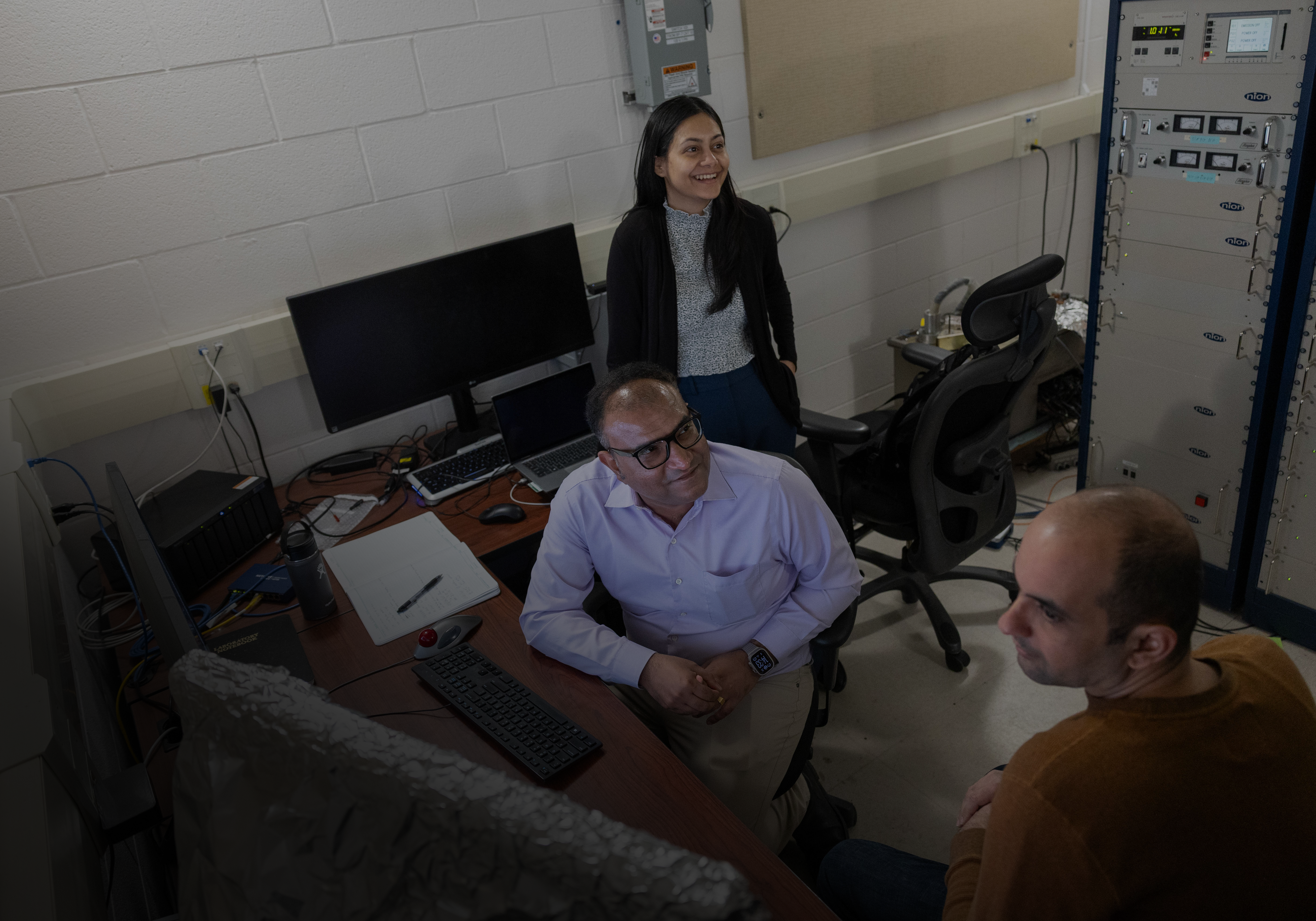
That mountain of data is useful not only for analyzing the project at hand; it is also used to train and improve AI models.
“Traditionally, when people do research and things don't work, that information often gets lost or is not considered useful for publication,” said Craig Bridges, who works with the autonomous chemistry lab. “But in this research, we try and capture all the information. We care about getting good data under reproducible conditions, not just trying to get the best samples.”
These projects often also make liberal use of computer simulations to guide experiments. The additive manufacturing project uses fast simulations connected to its high-tech temperature sensors to anticipate and adapt to issues that arise as it prints a metal part.
This approach is indispensable, as additive manufacturing leaves literally no time to stop and think. Every moment lost is a moment when the part is cooling in unwanted ways, threatening the integrity of the structure.
“We can run a bunch of simulations and ask, ‘What if we pause in the middle of the layer? What if we start on the left side instead of the right side for the next layer?’” said Stephen DeWitt, the project’s lead.
“We run through all these what-if scenarios, and then we see which one we expect to get us back on track. That's the instruction that we send to the printer.”
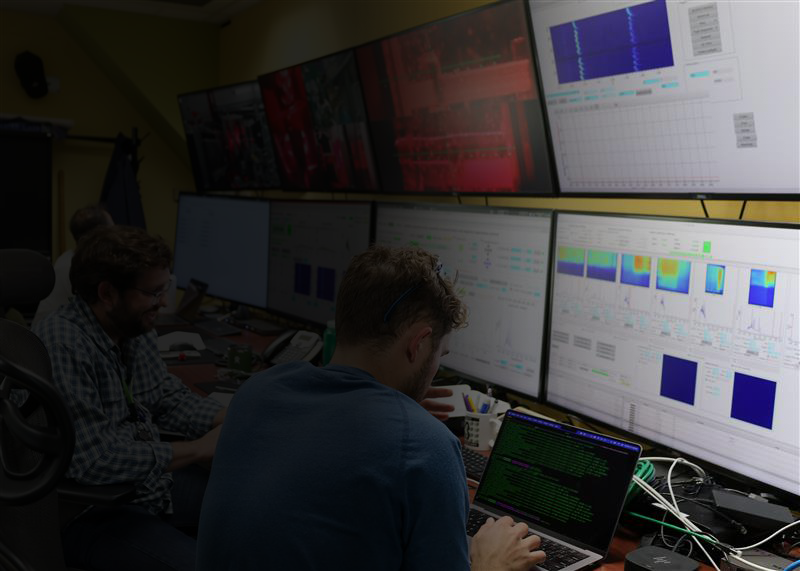
What will the future look like?
So what will labs of the future look like? The possibilities are manifold, according to Mintz.
Some may evolve into distributed user facilities, empowering remote research institutions to take advantage of ORNL’s research capabilities. Others may expand to incorporate production facilities that both discover new materials and turn them into devices for a variety of applications such as quantum computing, quantum sensing and microelectronics.
And many, he said, could blur the boundaries between scientific disciplines, promoting interdisciplinary collaborations to tackle emerging and urgent national research challenges.
"We're focused on transitioning to true multidomain science,” he said.

As INTERSECT progresses into its fourth year of a seven-to-10-year vision, Mintz believes its first goal — accelerating research — has been demonstrated.
“For example, in the INTERSECT continuous flow chemistry project, we can create products within hours compared to days — a measurable achievement,” he said.
The longer-term question is whether interconnected autonomous labs yield unprecedented breakthroughs.
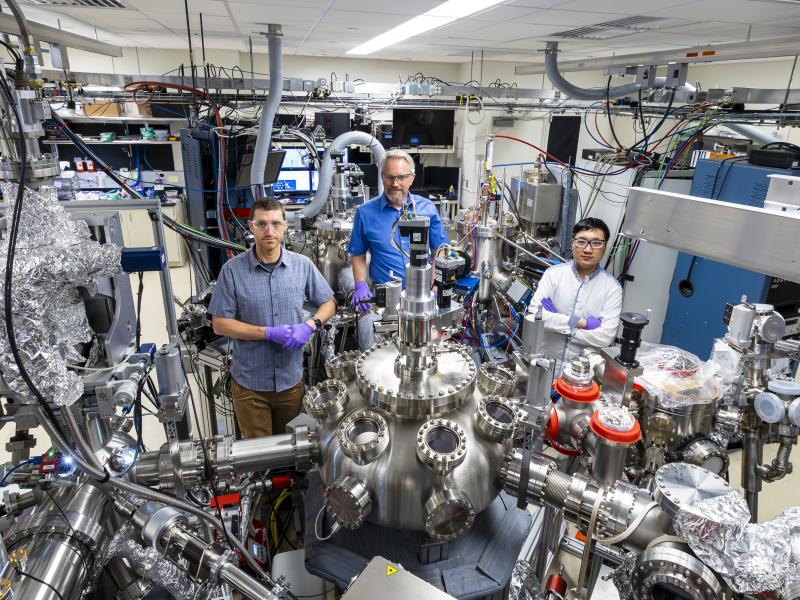
“INTERSECT is about forward-looking innovation. Can we unlock new scientific possibilities?” Mintz said. “Proving this potential is essential to gaining interdisciplinary buy-in and advancing toward the interconnected future we envision.”
To get there, Moore said, researchers will have to rethink how they do business.
“In the end, we are trying to redefine how we do science. We have seen the rapid development of artificial intelligence and machine learning tools, and we are already seeing how they change our approach to science.
“To fully harness the power of these tools to improve efficiency and accelerate scientific discovery, we have to rethink what a science laboratory should be and tailor it to make our instruments and facilities, our data generators, ready for this new way of performing science.”
UT-Battelle manages ORNL for the Department of Energy’s Office of Science, the single largest supporter of basic research in the physical sciences in the United States. The Office of Science is working to address some of the most pressing challenges of our time. For more information, please visit energy.gov/science.
ORNL’s INTERSECT, launched in 2022, established autonomous laboratories across scientific domains, using software tools and robotics to optimize researchers’ time by reducing monotonous manual tasks. Watch here

Alvin Weinberg's 1961 concept of "big science" raised important questions, and today, ORNL's INTERSECT initiative leverages advanced technologies to tackle global challenges. Read more
The INTERSECT initiative established six autonomous labs targeting diverse high-impact fields, aiming to connect specialized efforts through cross-discipline data and workflows. Learn more

A workshop led by scientists at ORNL sketched a road map toward a longtime goal: development of autonomous, or self-driving, next-generation research laboratories. Read more