2012
MDF Advanced Manufacturing Shapes the future
The catalyst begins with 26 ORNL—industry MOUs with materials suppliers, equipment suppliers, and end users of additive and carbon fiber technologies. MDF will leverage ORNL’s unmatched capabilities in materials, neutrons, and computational science to develop innovative manufacturing technologies, helping large and small companies alike.
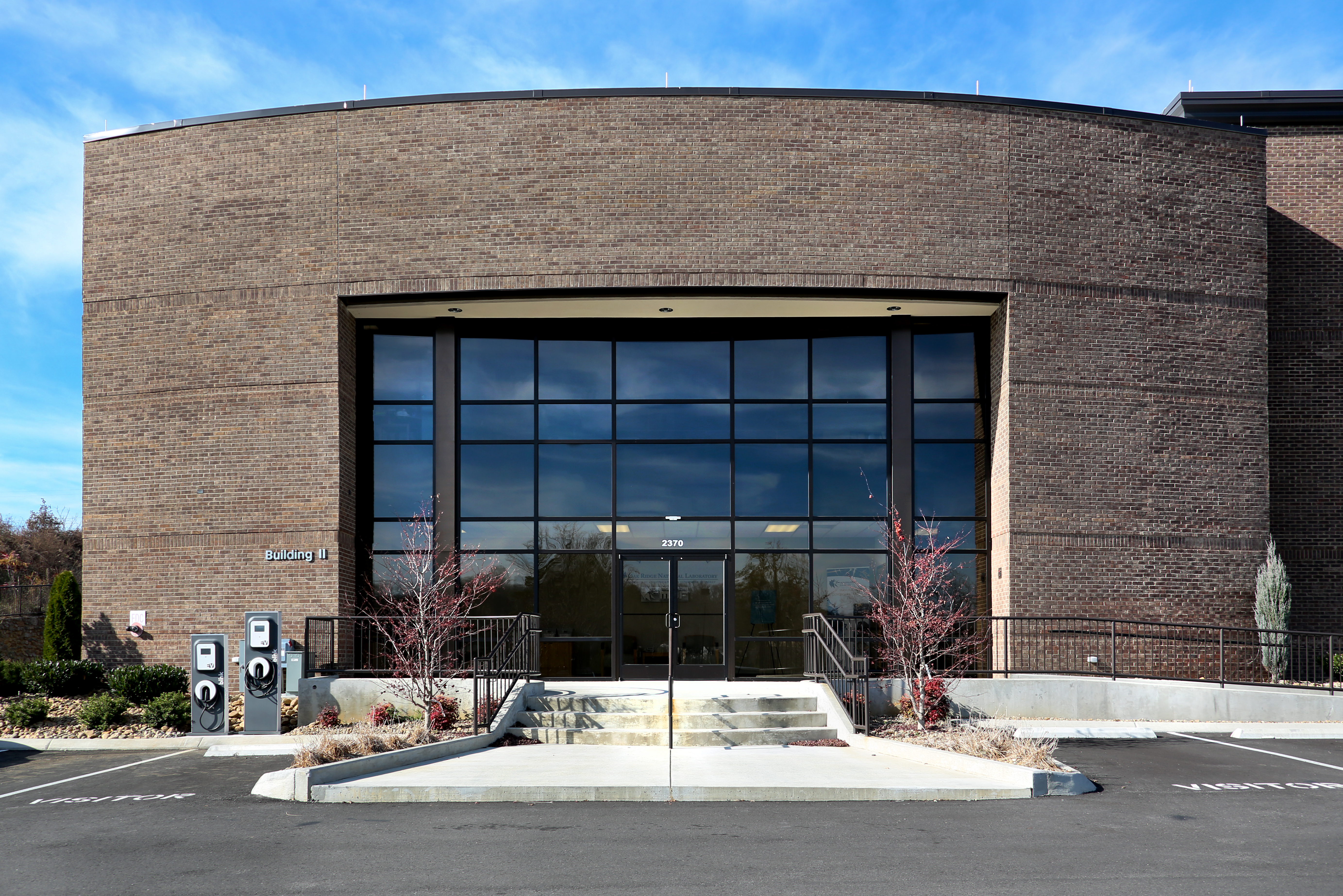
2012
One Layer at a Time
A team uses Electron-Beam Additive Manufacturing to produce a fully functional titanium robotic hand, demonstrating unmatched performance through design optimization. It is composed of only 46 parts and can be manufactured and assembled within 40 hours.
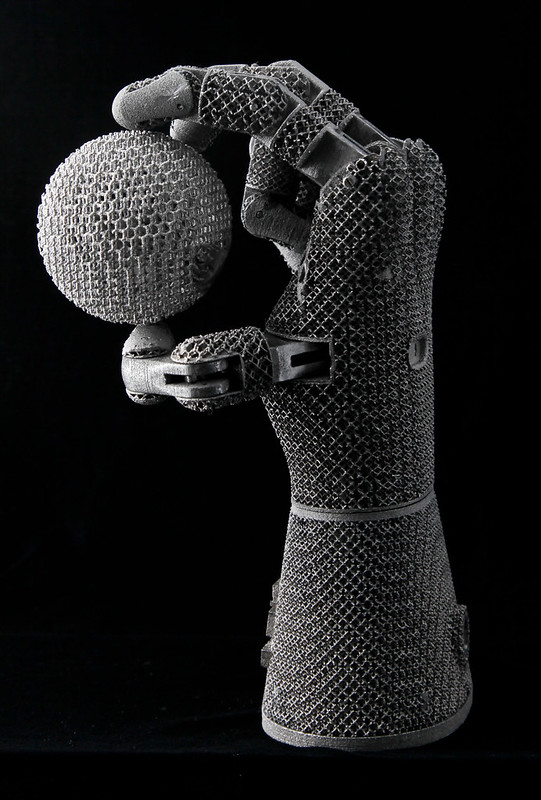
2012
Under Water Workers
A set of 3D-printed robotic arms for underwater use by the US Navy are printed using a titanium alloy. The arms have seven degrees of freedom and show proof of design in additive manufacturing with no external hoses or cables.
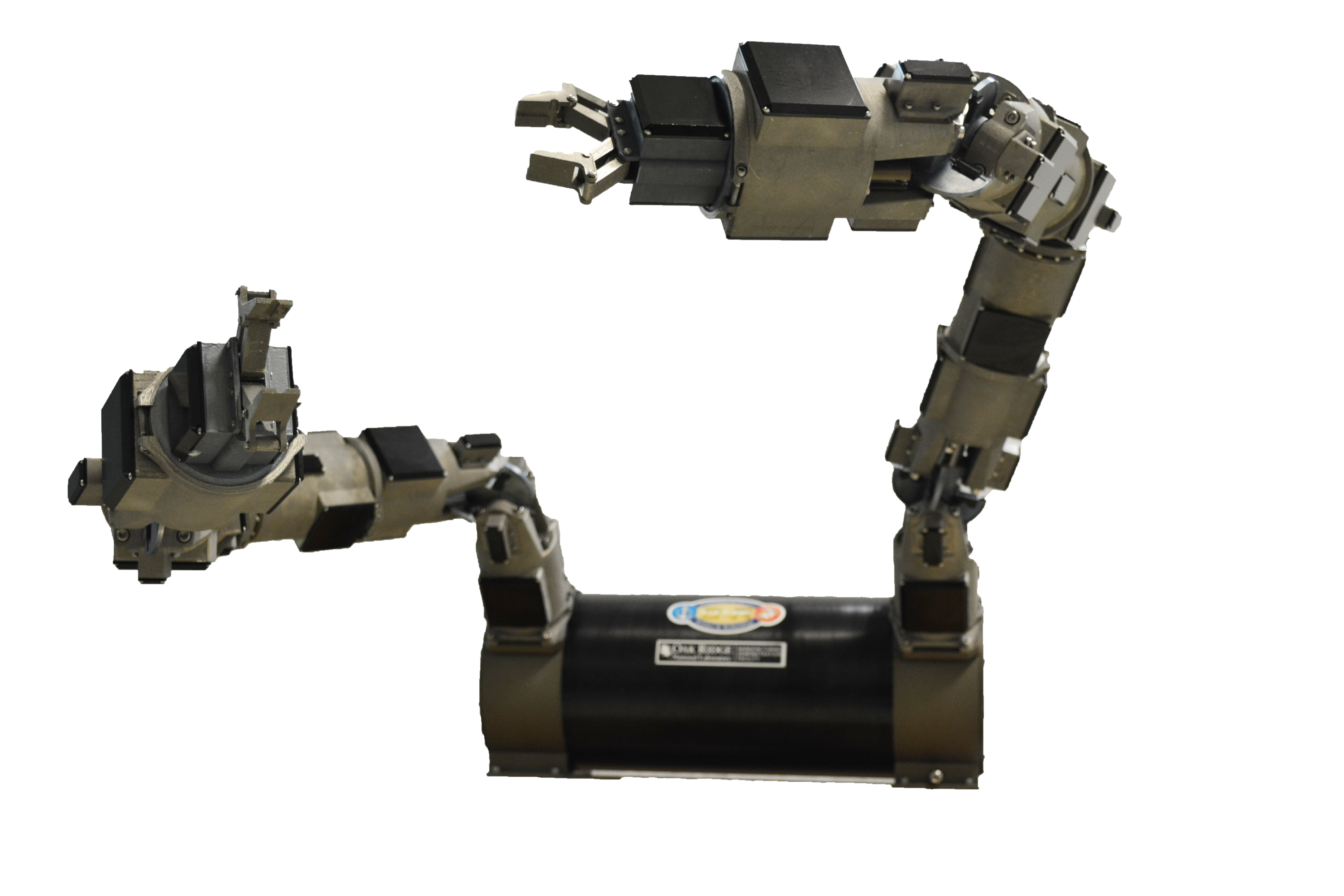
December 2013
Detecting Defects with AI
An innovative in-situ quality control system for electron beam melting (EBM) technology is demonstrated, presenting a promising alternative to traditional non-destructive techniques like X-ray computed tomography. This new technology combines an infrared camera with artificial intelligence to offer near-real-time 3D mapping of porous defects within additively manufactured components.
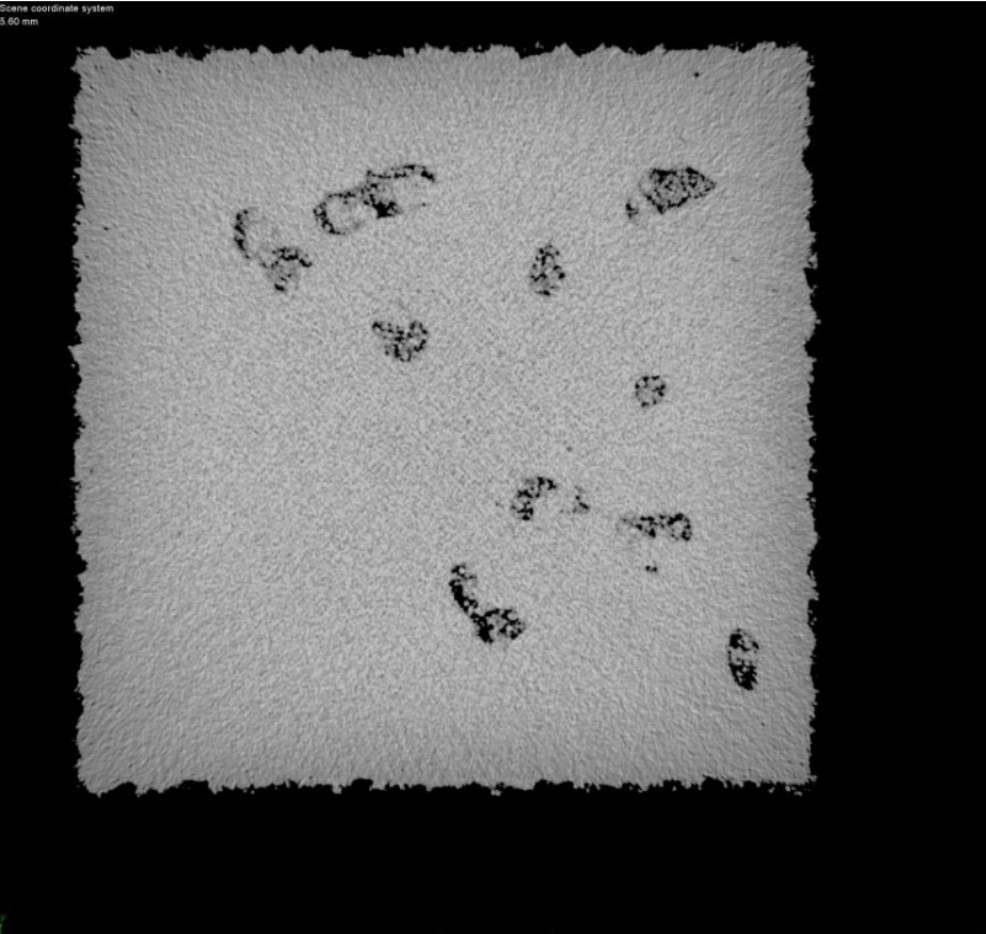
September 2014
Driving the Impossible
MDF researchers fabricate the world’s first 3D-printed electric car with Cincinnati Inc. and Local Motors live at IMTS in front of more than 100,000 people. The drivable vehicle is printed with a thermoplastic composite in just 44 hours, then milled and assembled over three days.
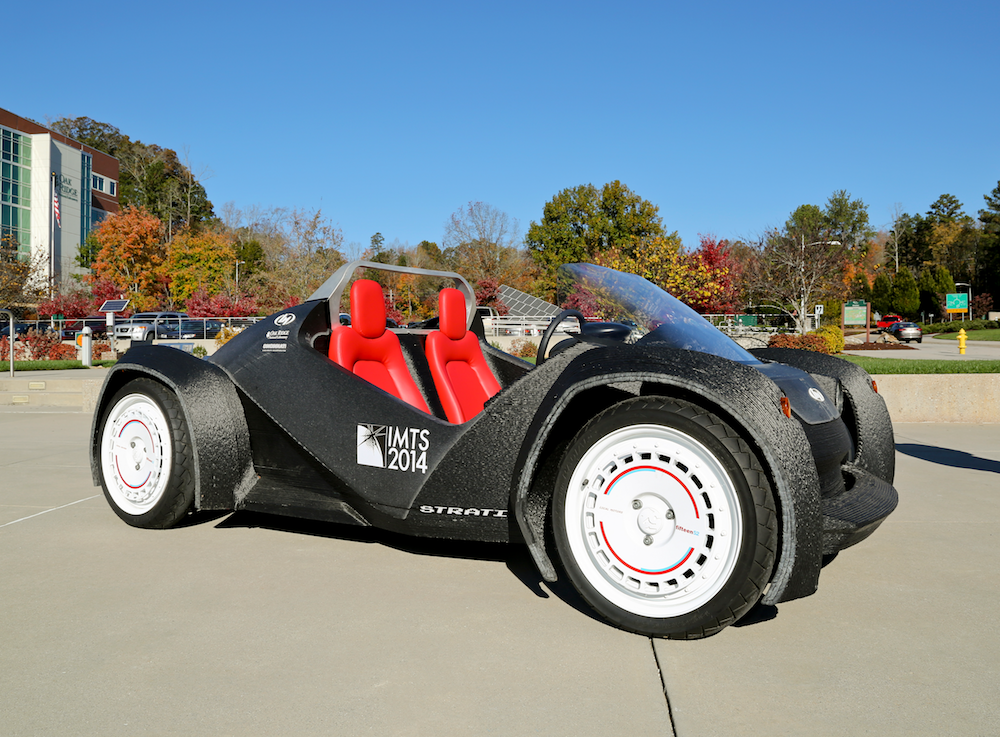
November 2014
3D Printed Shelby Cobra
A Shelby Cobra is taken from concept to drivable car in six weeks, debuting it at the 2015 Detroit Auto Show. Parts are printed in 24 hours, then machined, sanded, and polished, resulting in a 1,400-pound total weight—500 pounds of 3D-printed parts and 20 percent carbon fiber material.
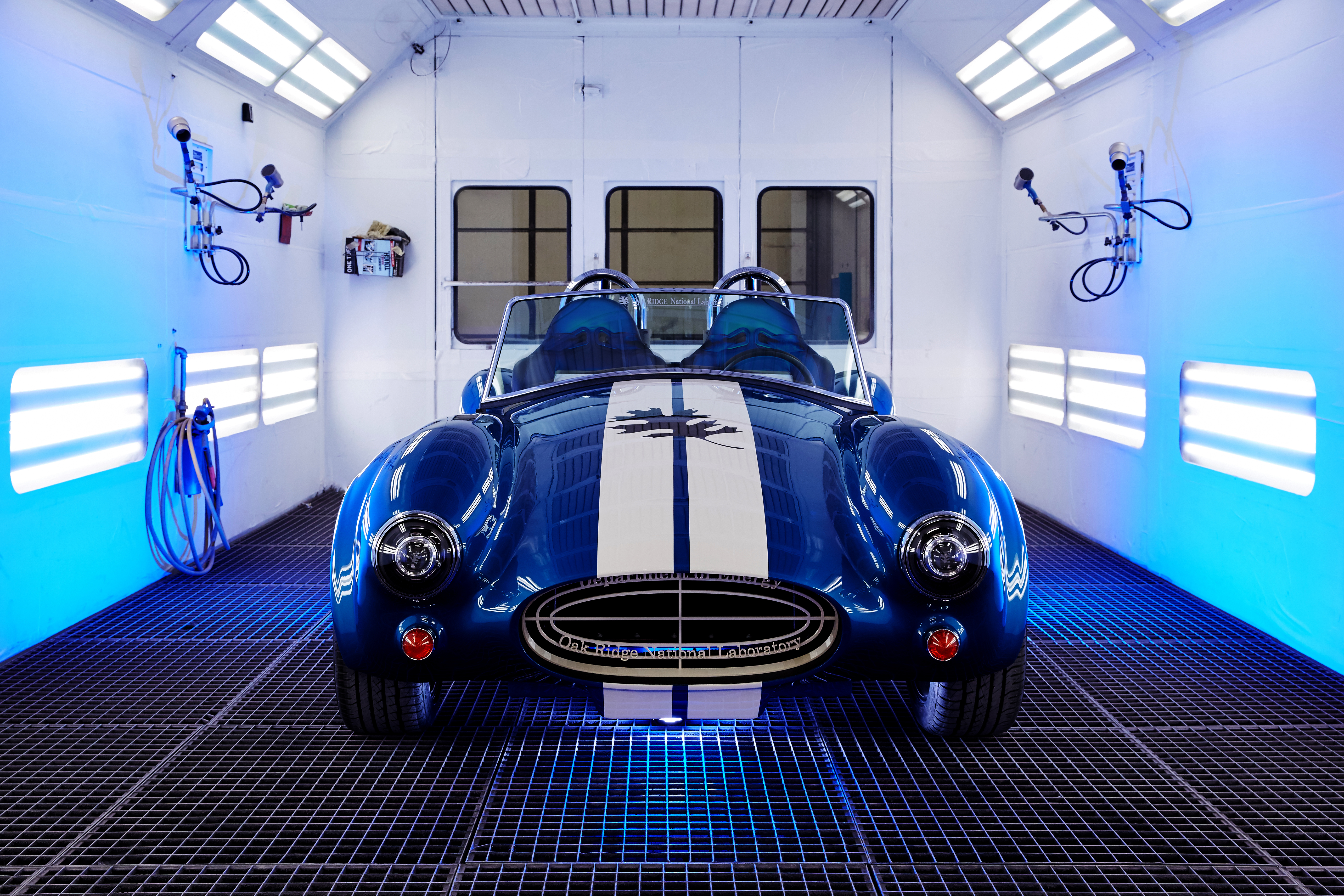
2015
New Grain Control Capabilities
Using electron beam melting, researchers demonstrate the ability to build metal components with site-specific control of the crystallographic orientation of grains.
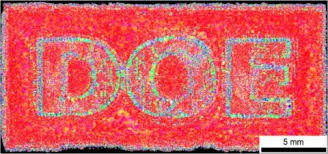
2015
Energy Integration for Car and Home
The fabrication of a combination house and car demonstrates a new approach to energy use, storage, and consumption through large-scale 3D printers. The Additive Manufacturing Integrated Energy demonstration, or AMIE, is a model for energy efficient systems that link buildings, vehicles and the grid.
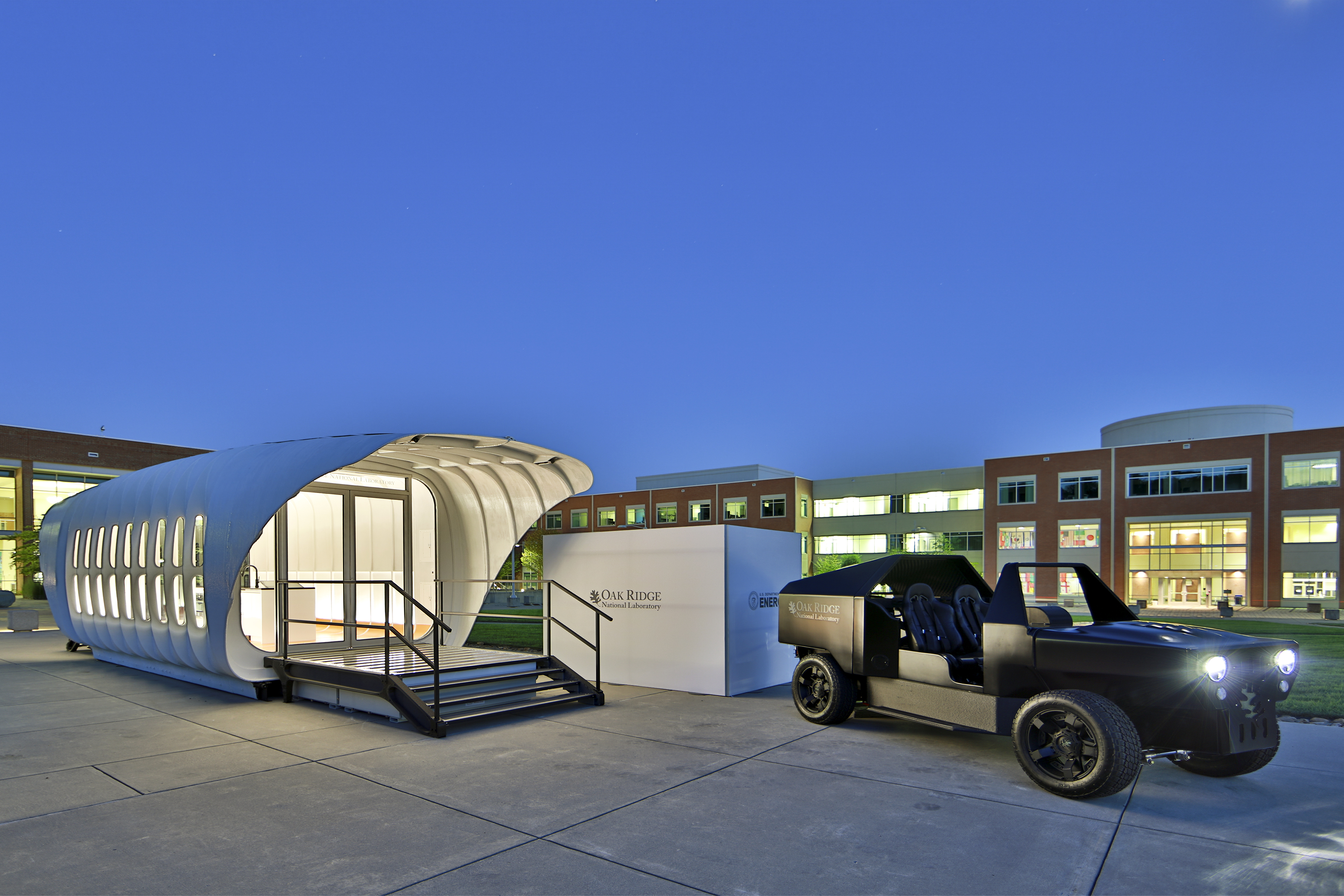
April 2015
Power from Water
MDF enables Emrgy, an Atlanta based startup, to manufacture low-head modular hydropower devices for shallow water streams with untapped energy potential. In 2017, Emrgy installs the devices for demonstration in Denver, Colorado. In 2019, Emrgy signs an agreement with GE Renewable Energy for global commercialization of Emrgy’s hydropower units.
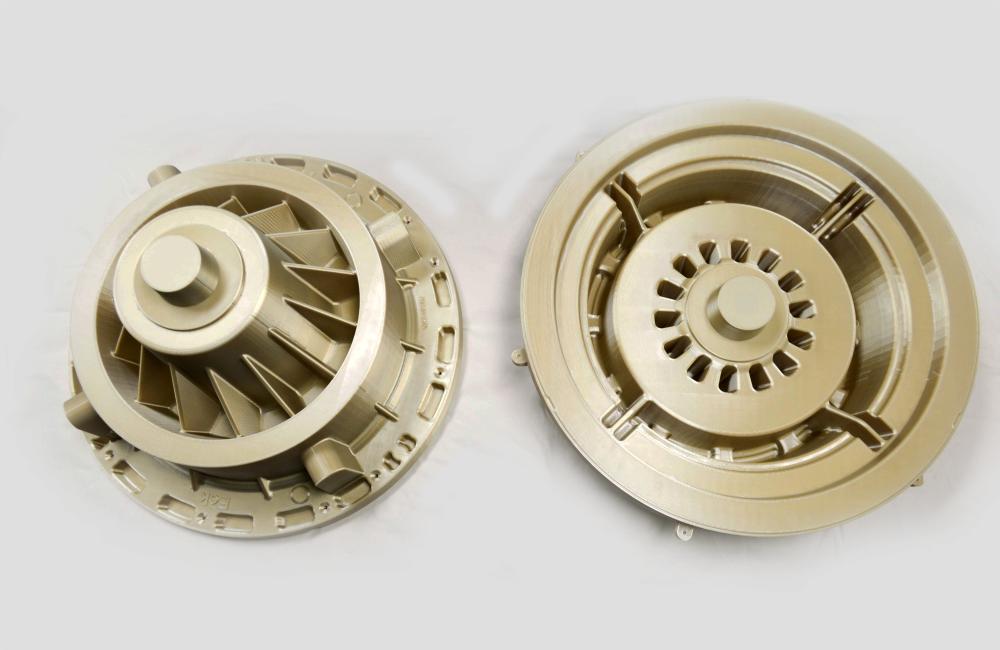
2016
Bamboozled in Miami
Using over 10,000lb of material, two bamboo pavilions are created printed for the DesignMiami expo. The pavilions demonstrate the potential to 3D print biobased materials and initiated efforts related to sustainable manufacturing practices.
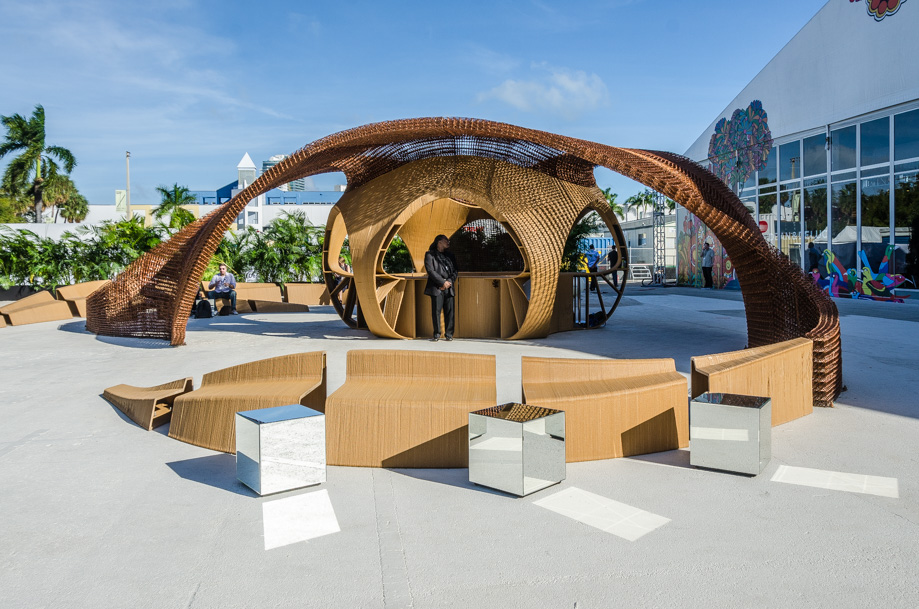
2016
World’s Largest 3D-Printed Tool
A 3D-printed “c tool” developed for Boeing receives a Guiness World Record for the largest solid 3D-printed item. The tool measures 17.5ft long, 5.5ft wide, 1.5ft tall, and weighs about 1,650lb. The tool is used on the production floor, initiating widespread use of 3D printed tooling.
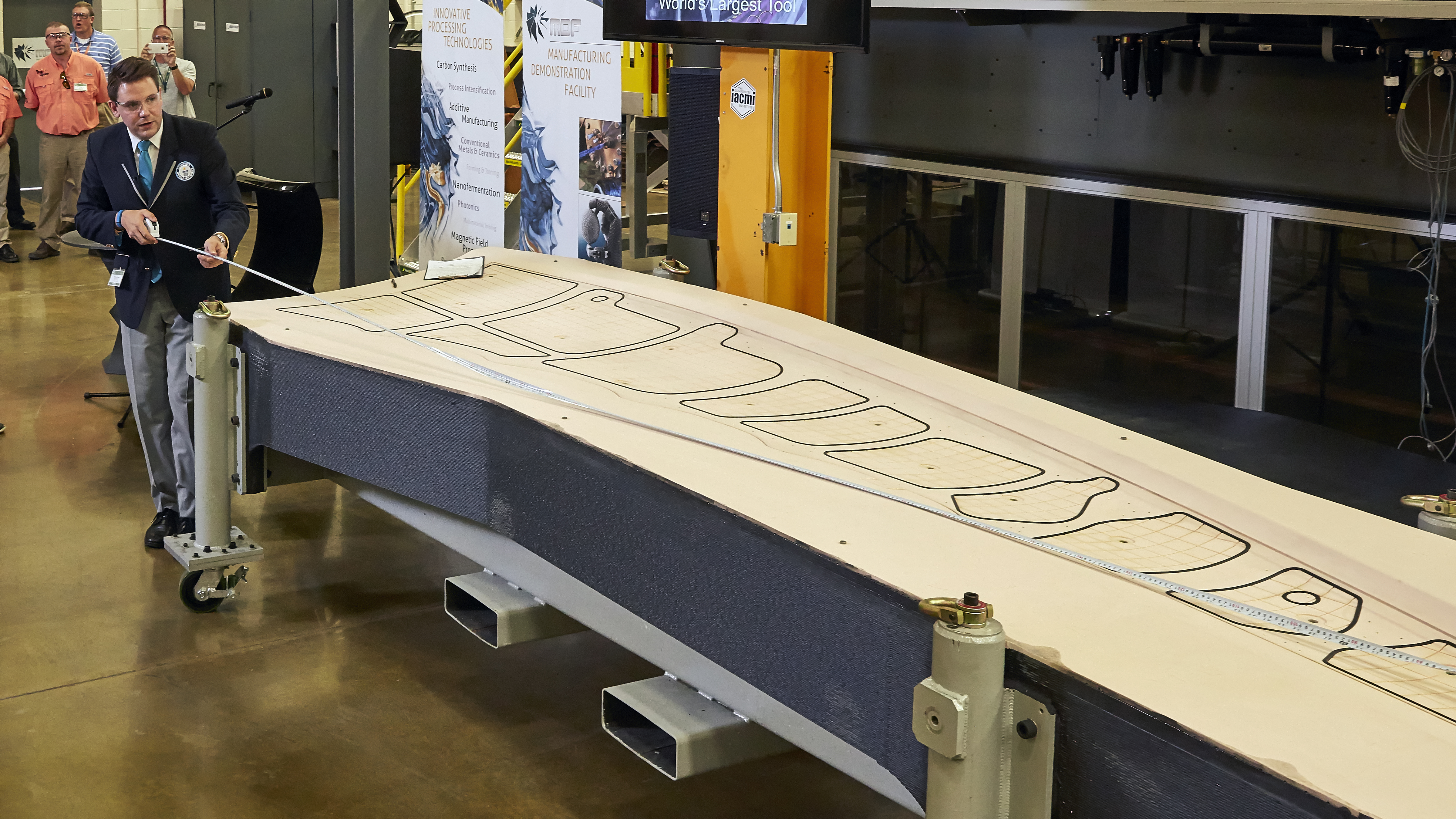
September 2016
3D Printing Digs Deep
ORNL demonstrates revolutionary breakthroughs in large-scale metal additive manufacturing technology with a fully printed functional excavator arm with integrated hydraulic lines using low-cost steel. The cab and heat exchanger were printed as well, highlighting the MDF’s expertise in AM technologies at North America’s largest construction trade show.
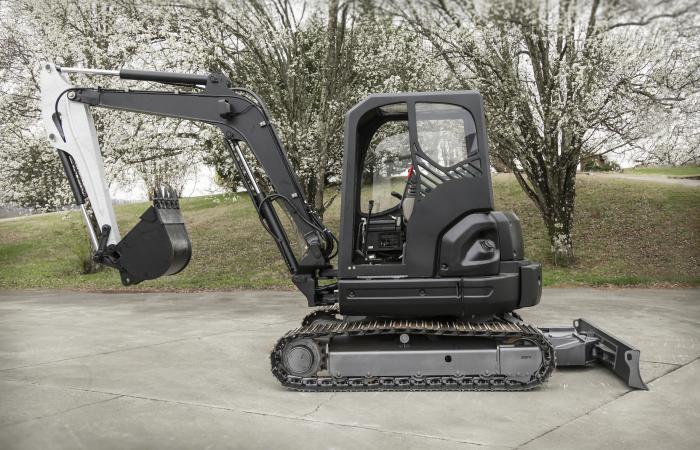
2017
We All Live in a (Black Submersible Hull)
In only four weeks, a 30ft-long submersible hull demonstrator is created for the US Navy using Big-Area Additive Manufacturing (BAAM) technology. BAAM reduced production costs by 90 percent and proves the potential to create on-demand vehicles while saving time and energy.
2017
The ‘Art’ of Additive Manufacturing
Leveraging modeling, artificial intelligence and machine learning, researchers expand on the microstructure manipulation techniques discovered in 2014 to create a copy of the Mona Lisa in a nickle based superalloy. The work of art demonstrates unprecedented levels of microstructure control only possible with 3D printing technologies.
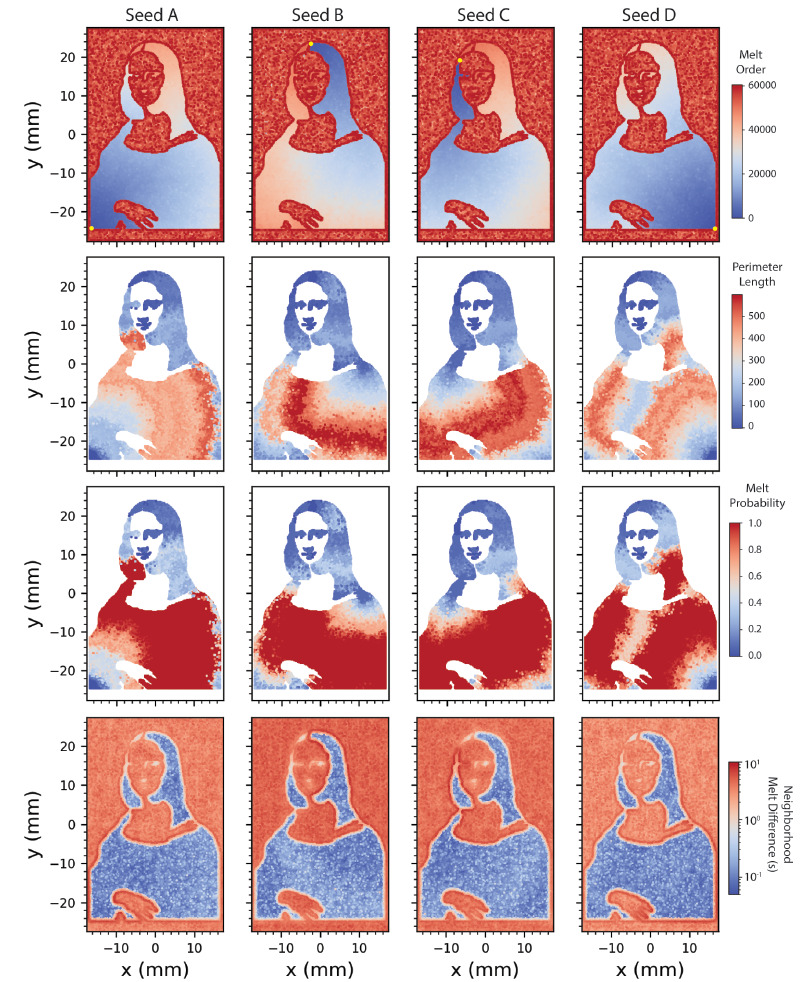
2018
Autonomous Bus
In conjunction with the Vehicle Systems Integration Laboratory, researchers print ORNL’s first autonomous bus, nicknamed GROVER, which is used to test sensors and controls, batteries, and power electronics in a single platform that can move in any direction.
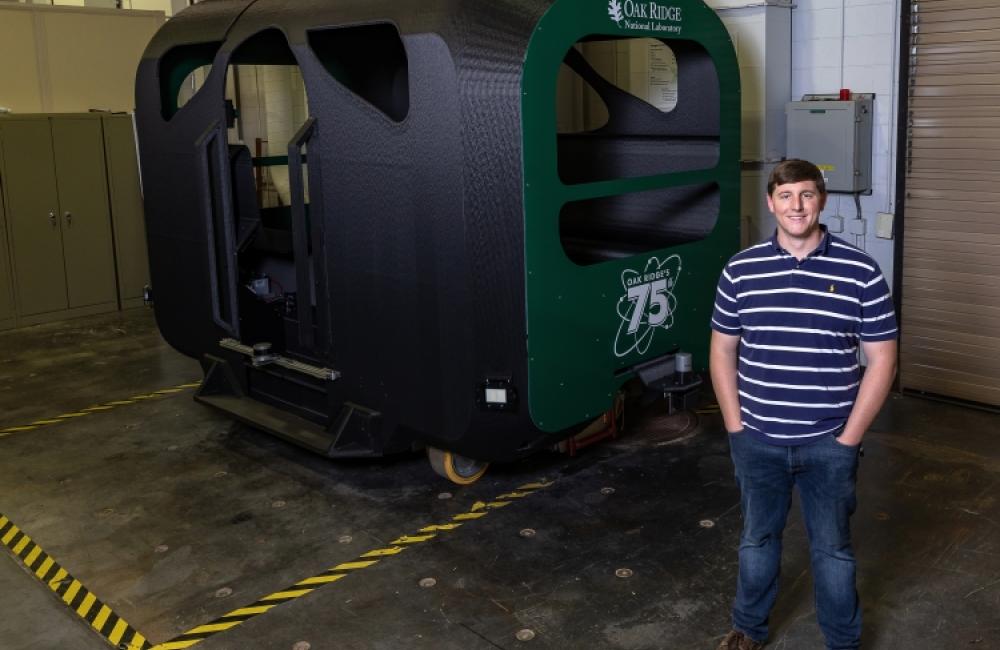
September 2018
Producing a Die in a Day
Researchers design, print, machine, and use five dies in a single day for 130,000 attendees at the International Manufacturing Technology Show, the largest manufacturing conference in North America. Ordinarily, the creation of die casts could take anywhere from weeks to months.
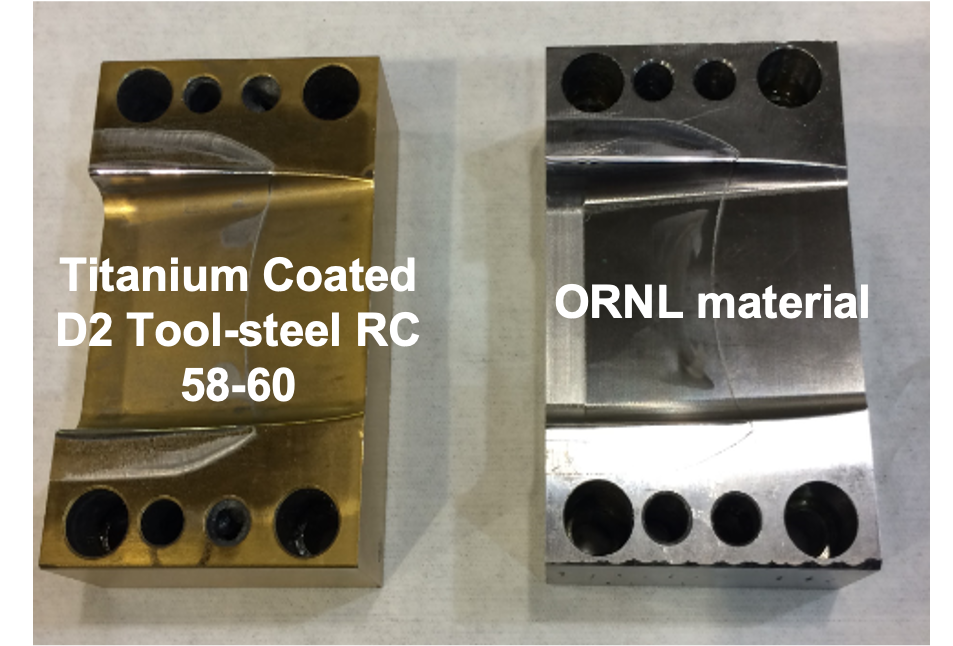
March 2019
Concrete Sugar Cubes
Polymer extrusion is used to create carbon fiber reinforced thermoplastic molds for precast concrete façade segments of the Domino Sugar Refinery in Brooklyn, New York. Each mold can cheaply cast 200+ concrete parts, a 75% cost saving per mold over traditional wood molds.
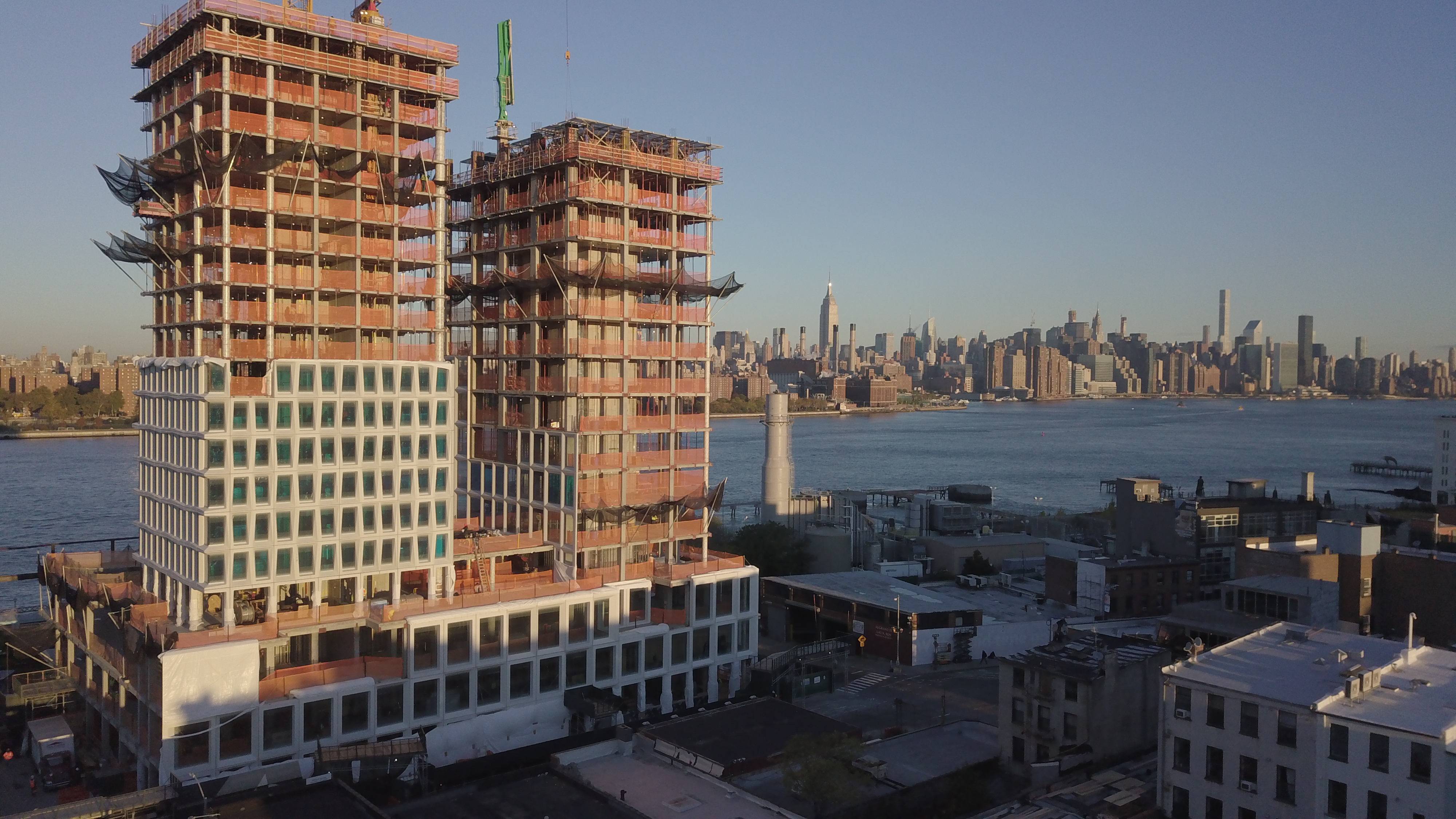
2020
Concrete Ideas
Researchers create a machine tool base using an additively manufactured polymer mold filled with fiber reinforced concrete. The base is shown to have a better stiffness-to-dampening ratio than traditional cast iron bases while being significantly cheaper and faster to produce.
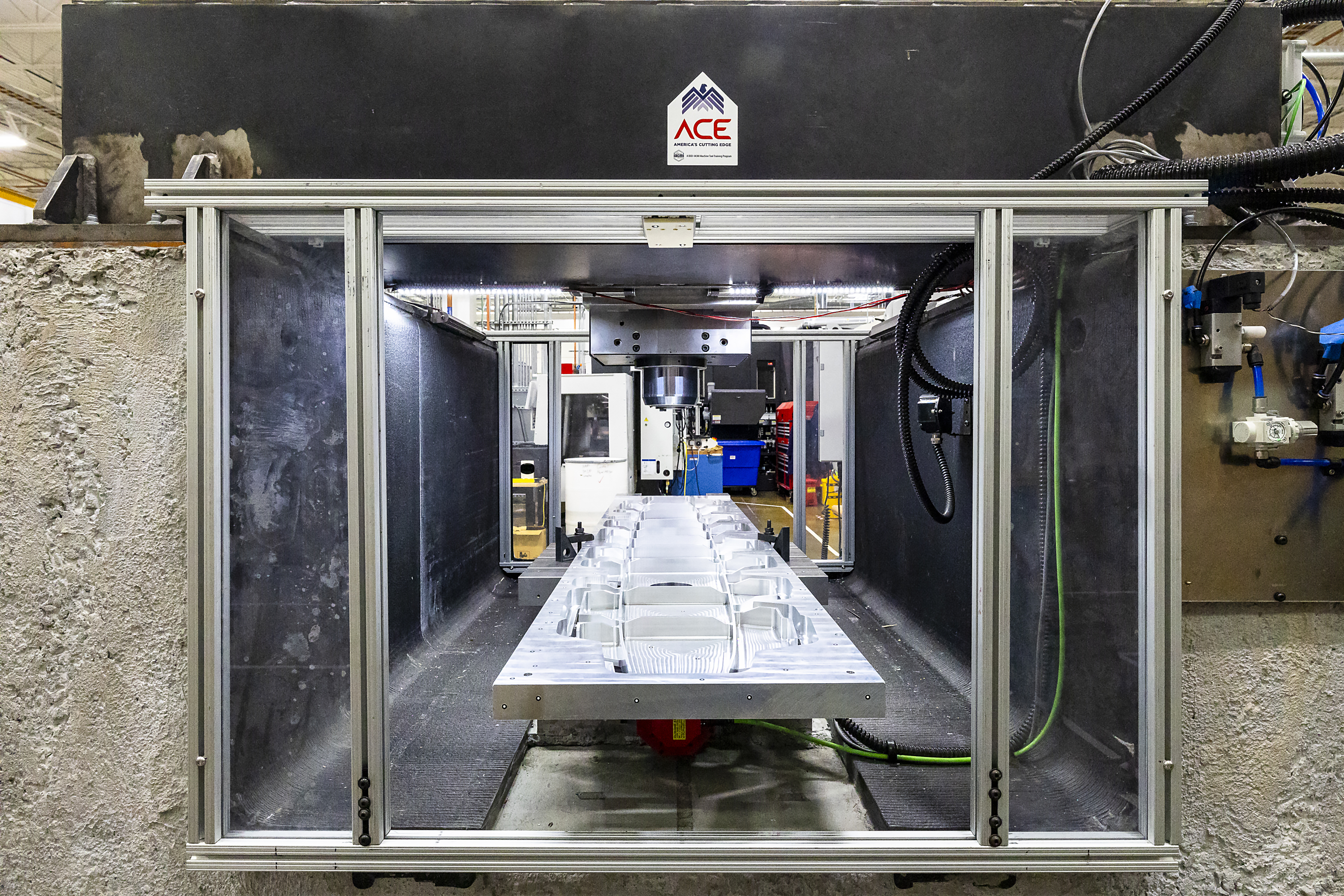
2020
High Temperature Turbine Blades
Using powder bed additive manufacturing, and working with Siemens Technology, 3D-printed turbine blades are created from a highly non-weldable nickel superalloy (IN718) and certified for use in gas powered turbine engines. This demonstration paves the way for many more wire-arc advancements to follow.
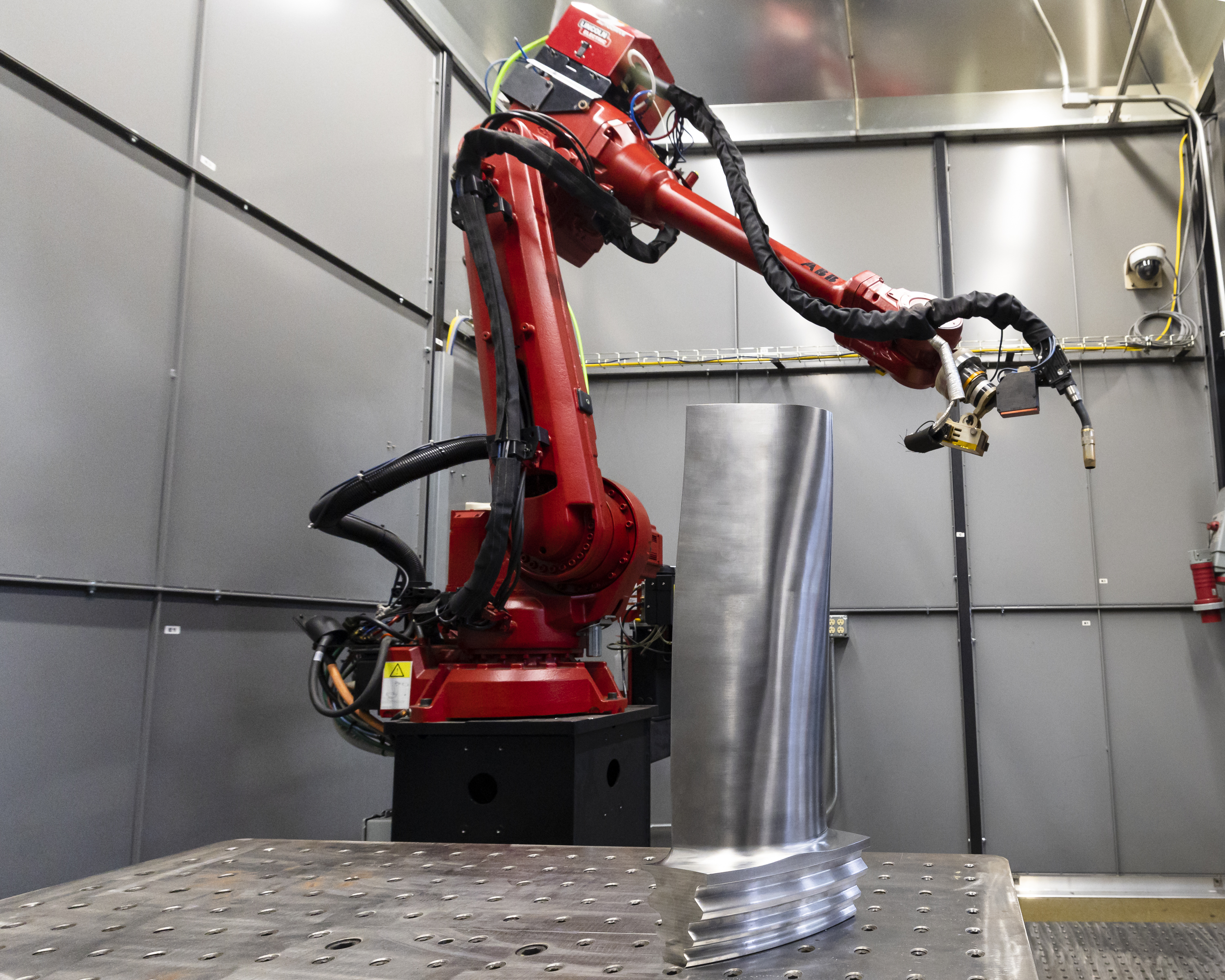
2020
Building Walls and Breaking Barriers
A 3D-printed concrete smart wall showcases the possibility to function as a heating and cooling system for a room using an embedded thermal storage system, drastically reducing energy use. Field tests reveal that the technology could yield more than an 8 percent savings on energy.
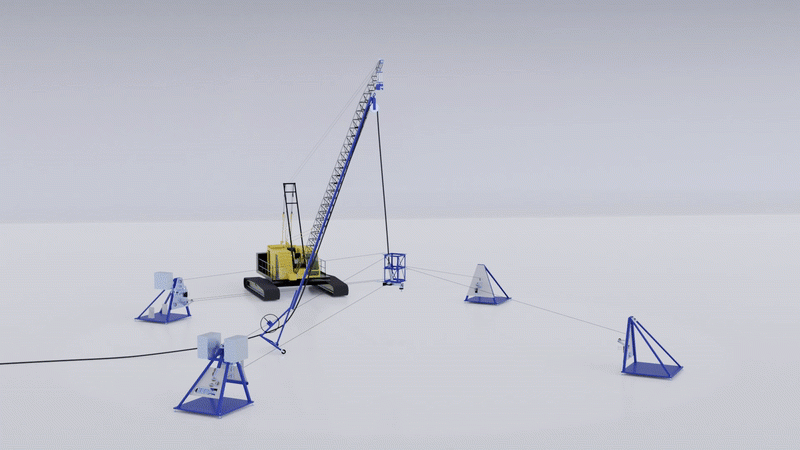
2020
Healthcare supplies
In the fight against COVID-19, researchers at MDF pivot their manufacturing expertise to produce custom molds and tooling for the mass production of millions of N95 masks, as well as a variety of other healthcare supplies such as test kits and face shields.
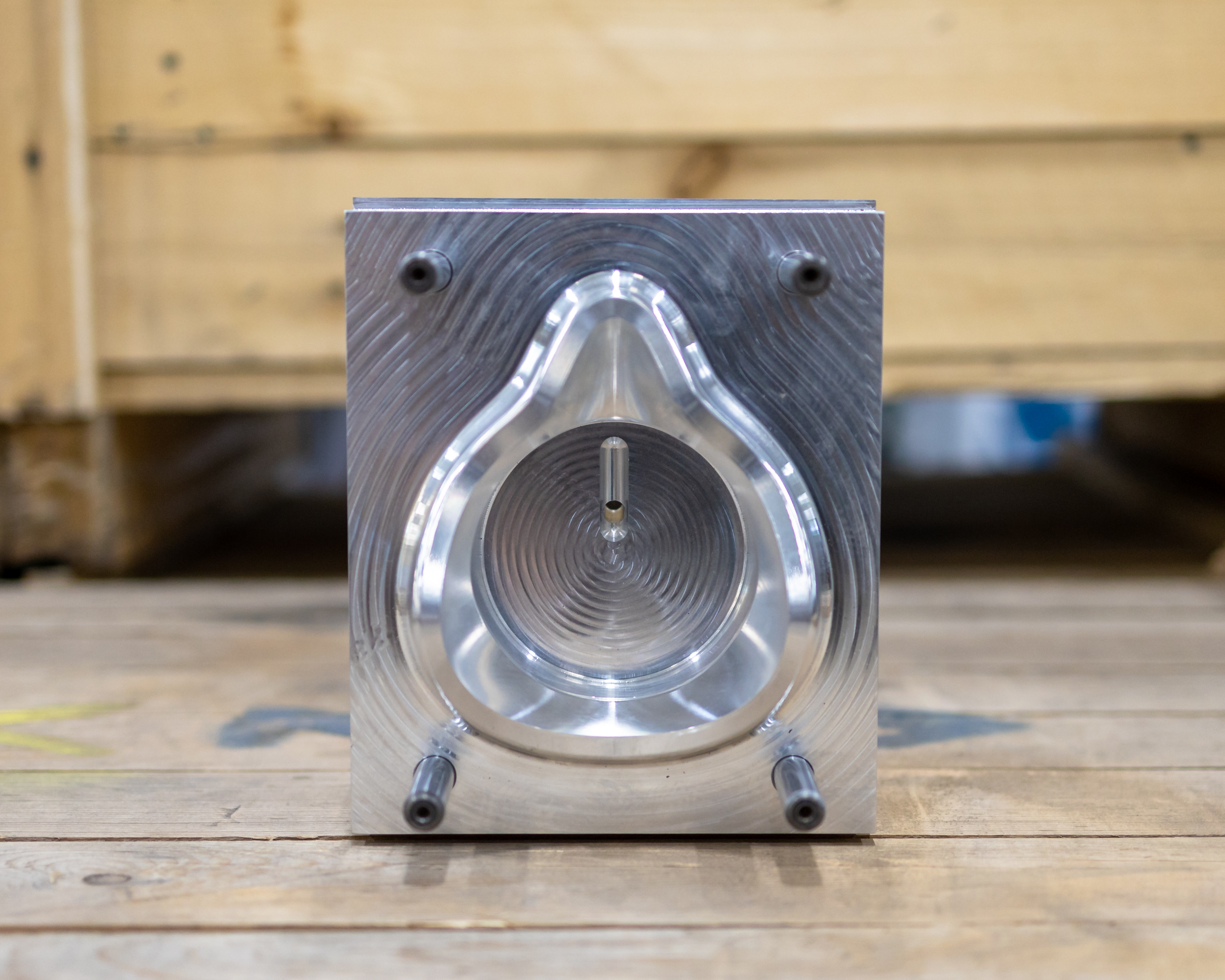
2020
Face Mask Production Speed
Working alongside MDF in the fight against COVID-19, the Carbon Fiber Technology Facility applies melt-blowing capability to the production of ORNL-developed self-sanitizing filter material for N95 masks. The technology enables the production of more than one million face masks and respirators per day and creates 1,500 jobs.
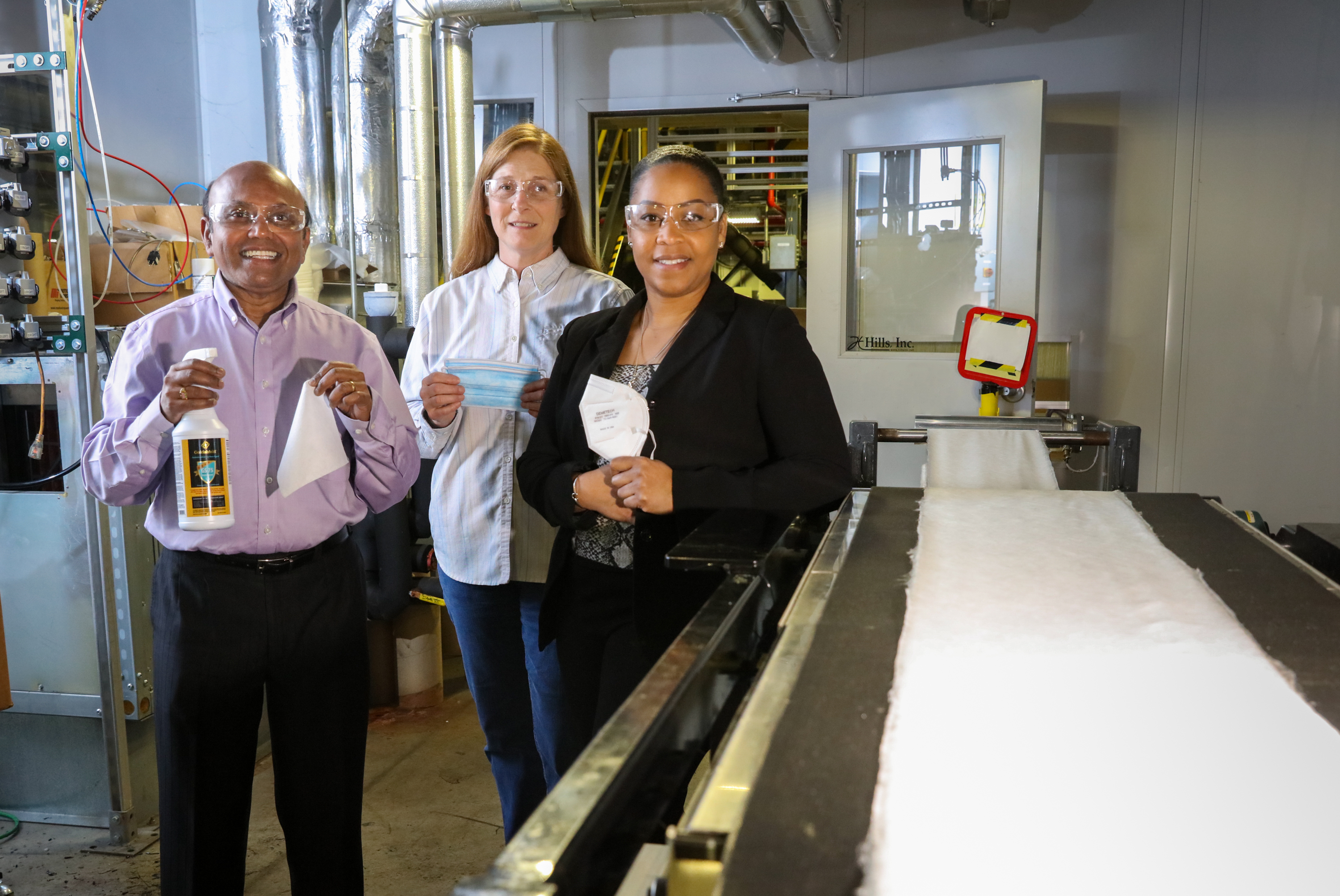
August 2020
3D Printing Goes for a Spin
In collaboration with Solar Turbines, a set of 3D-printed gas turbine engine blades and an air foil are produced from a traditionally non-weldable superalloy (IN 738). The project is a milestone for the goal of rapidly produceable turbine blades capable of performing inside turbine engines.
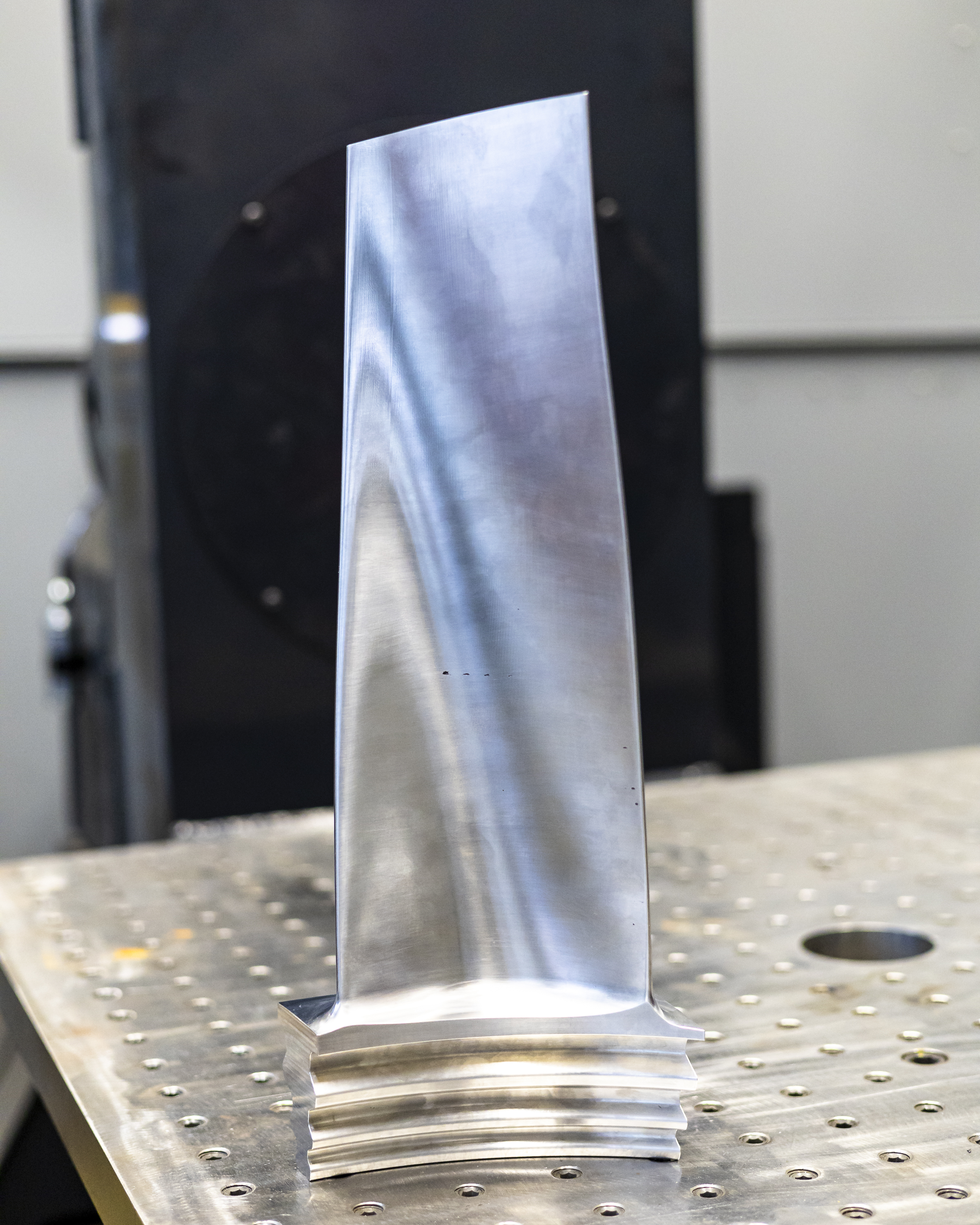
August 2020
Peregrine Launches
Peregrine, an AI software for laser powder bed 3D printers, supports the advanced manufacturing digital thread that collects and analyzes data through every step of the manufacturing process, from design to feedstock selection to the print build to material testing. Peregrine quickly becomes ORNL’s most licensed AI technology.
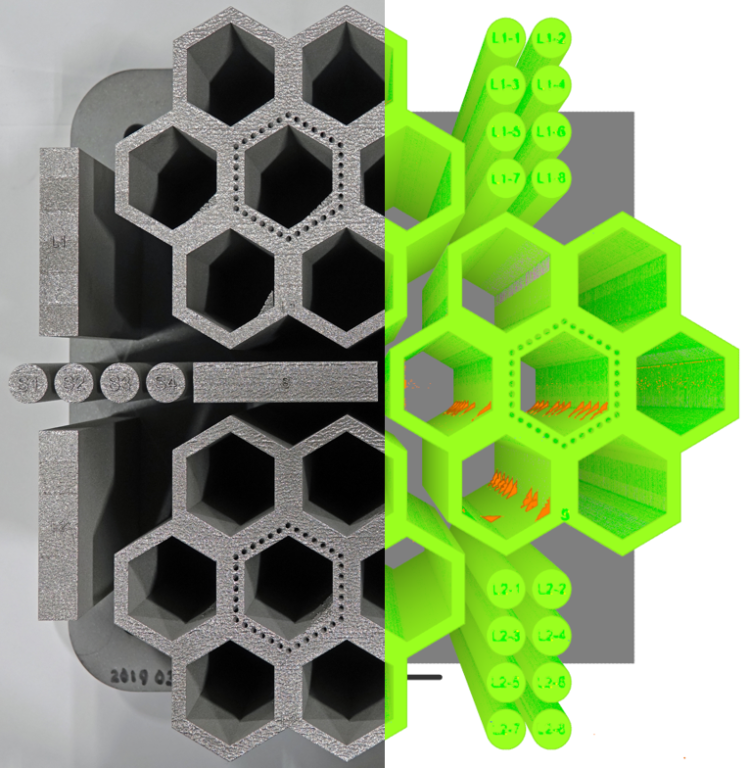
2021
3D Printing Goes Nuclear (Power)
Four fuel assembly brackets are additively produced and rigorously analyzed using AI-based software, then installed in TVA’s Browns Ferry Nuclear Plant in Athens, Alabama. The installation demonstrates the potential for 3D-printed parts to be rapidly certified and qualified for use in highly regulated environments.
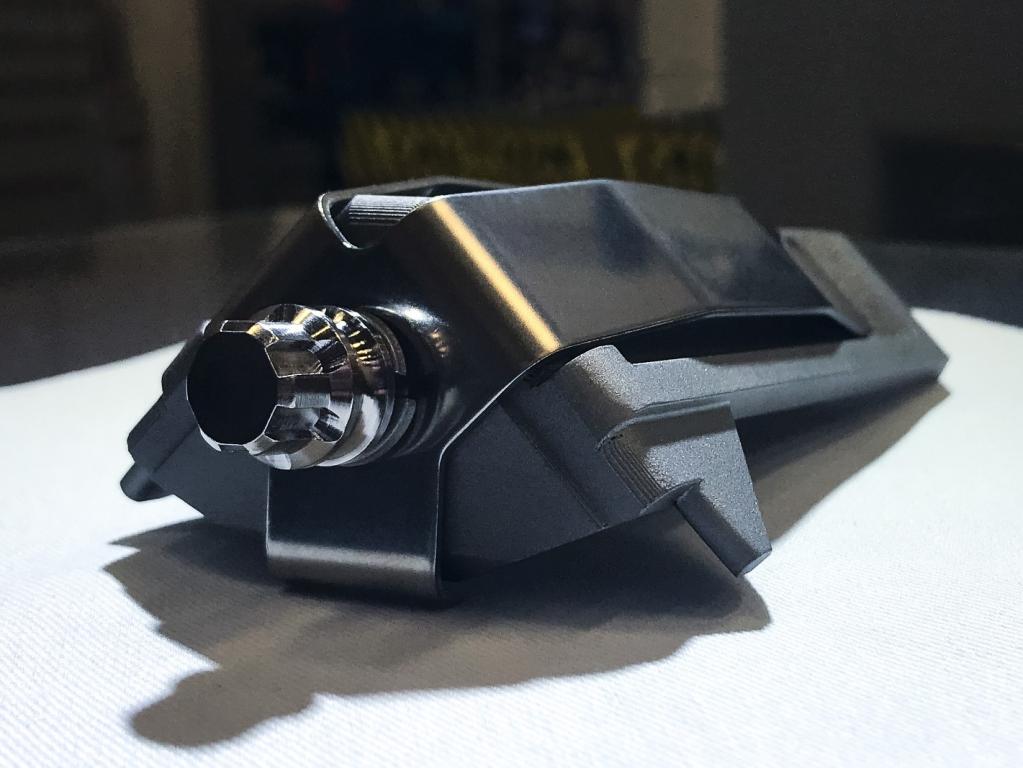
2021
3D Printing Can Take the Heat
A 3D printed thermal protection shield (TPS) is installed onboard NASA’s Cygnus spacecraft for a supply mission to the International Space Station, marking the first time an AM heat shield has been sent to space. The TPS not only protected Cygnus on the way up, but successfully allowed reentry.
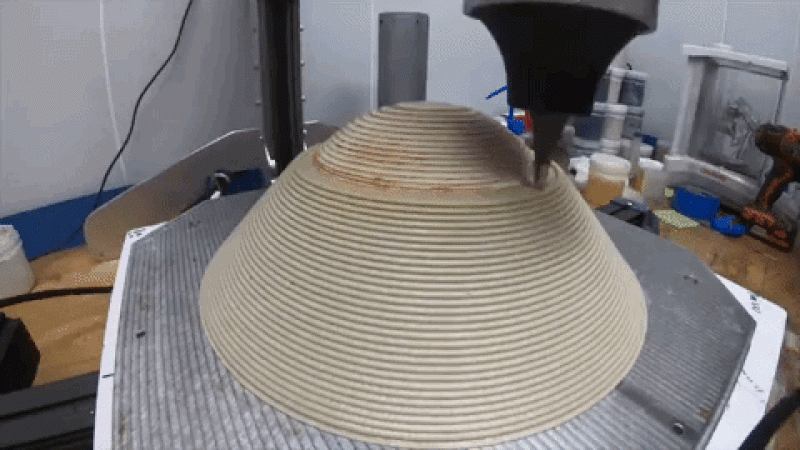
March 2021
Quick Cooling Tooling
In collaboration with DTS, researchers at MDF use a wire-arc technology system to 3D print a hot stamping die for an automotive “b-pillar.” The die takes less than half the time to produce than those made using traditional methods and performs better in the extreme heat faced during large-scale production.
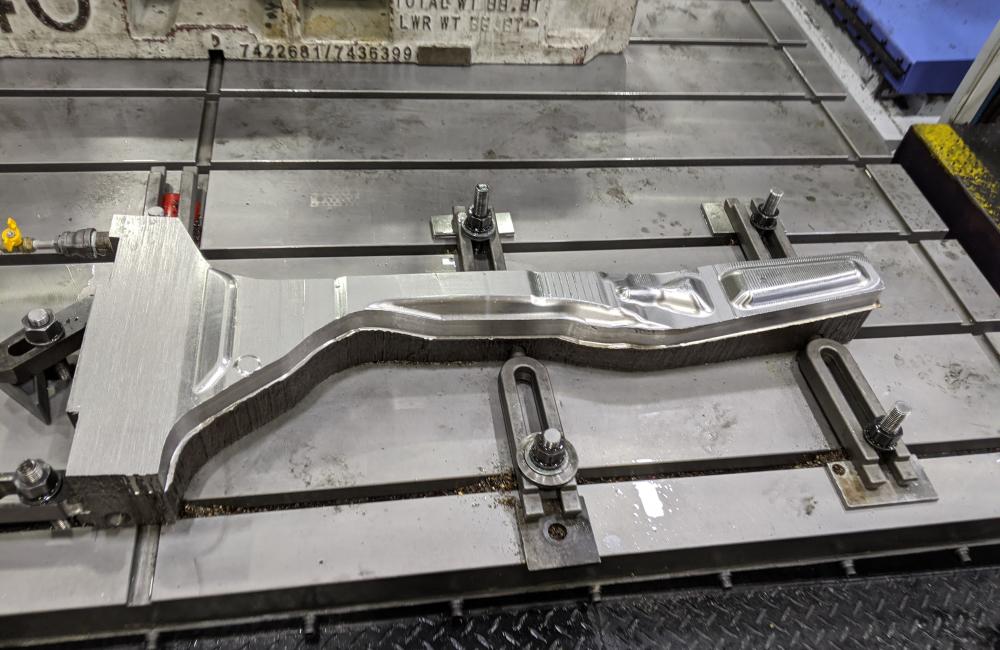
November 2021
Creep Resistance
Using a laser powder bed system, pistons are printed from a lightweight aluminum alloy for testing in a full-scale engine. The alloy demonstrates a remarkable ability to resist the deformation, or creep, caused by spending long periods in harsh environments. Creep-resistant materials are needed for automotive and aerospace applications.
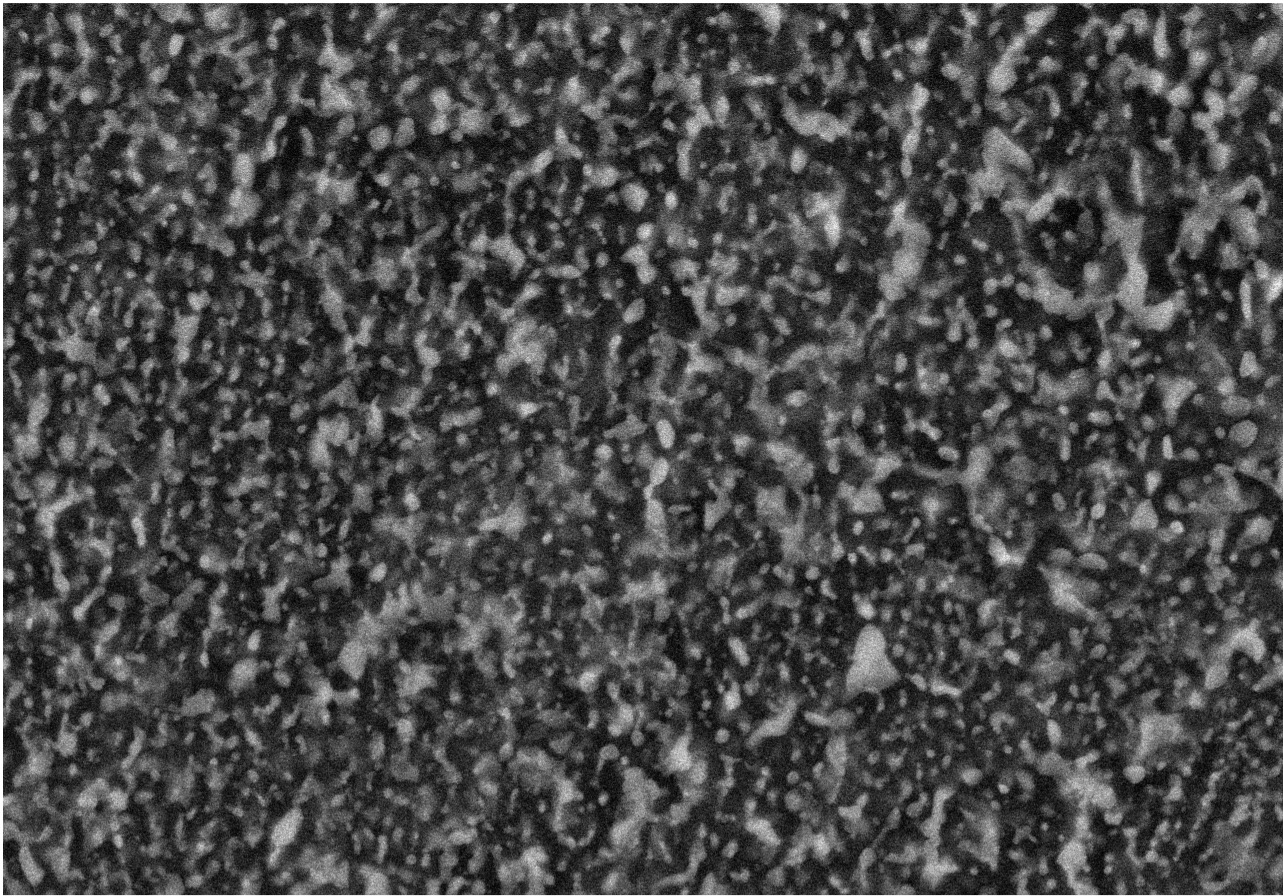
2022
Faster, More Precise Machining
ORNL and MSC collaborate to improve CNC milling performance by creating a digital twin of a CNC machining center that predicts the optimum stable speeds, feeds, and depth of cut in automated machining. Initial results reveal massive improvements in profits and efficiency.

2022
3D Printing Can Handle the Pressure
In just 19 hours, researchers 3D print a high-pressure die casting mold for a marine engine component using 410 stainless steel parts. The technology improves the productivity of pre-existing US tooling and demonstrates 3D printing’s ability to craft molds that can handle high pressure for extended periods.
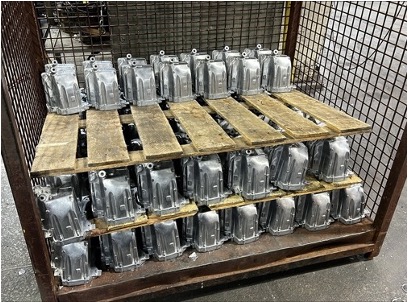
September 2023
Clean Racing
In collaboration with Airtech Advanced Materials Group, researchers use recycled materials to 3D print a new splitter mold and help the Brumos Racing Car set a world record for its class at the 2023 Pikes Peak International Hill Climb, demonstrating the endless recycling potential of 3D printing.
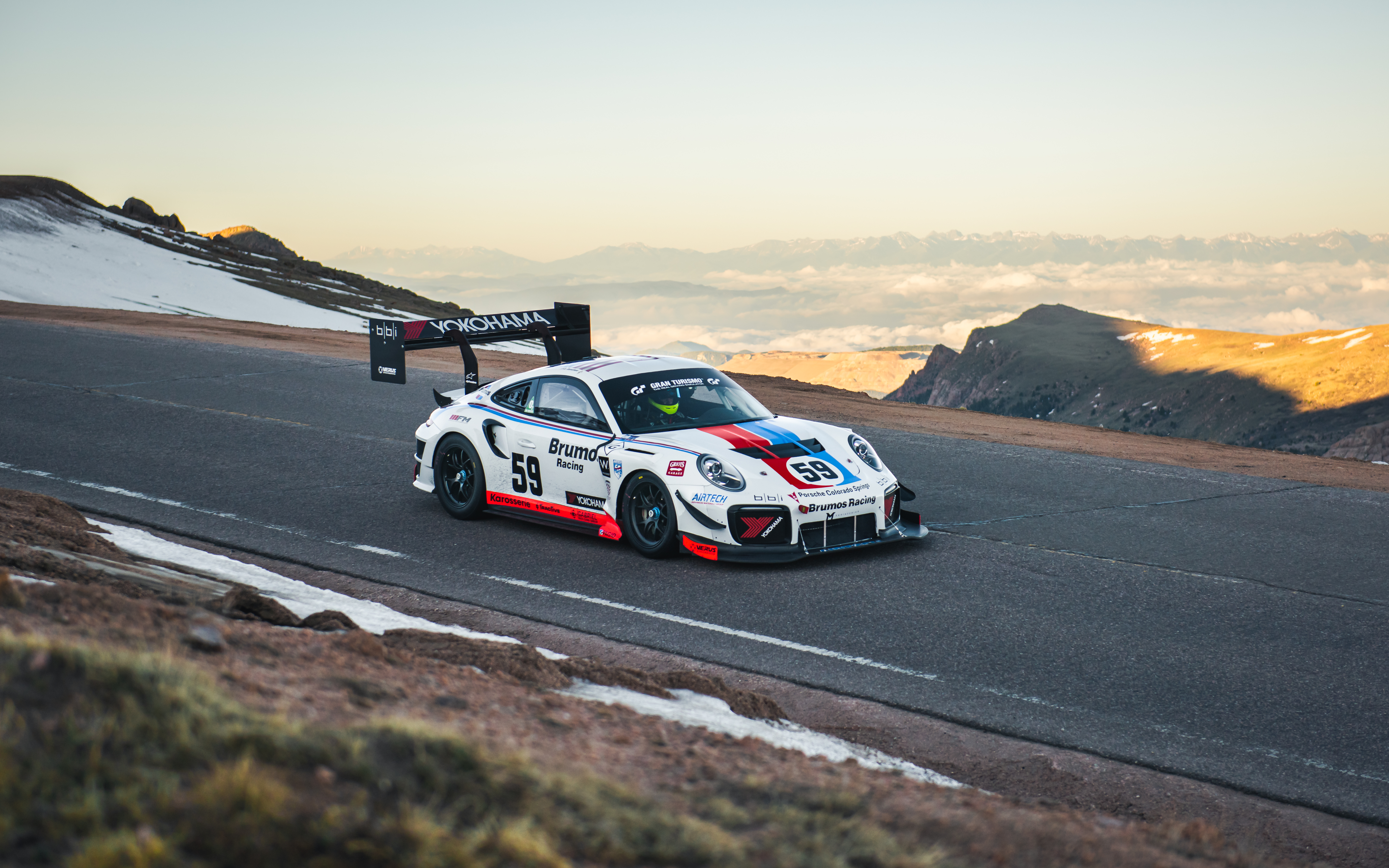
October 2023
Copper and Steel, Together at Last
By functionally grading two materials together, researchers deposit stainless steel on top of a pure copper alloy during 3D printing. This novel approach has the potential to help the tooling industry improve thermal performance in molds and dies without losing mechanical performance.
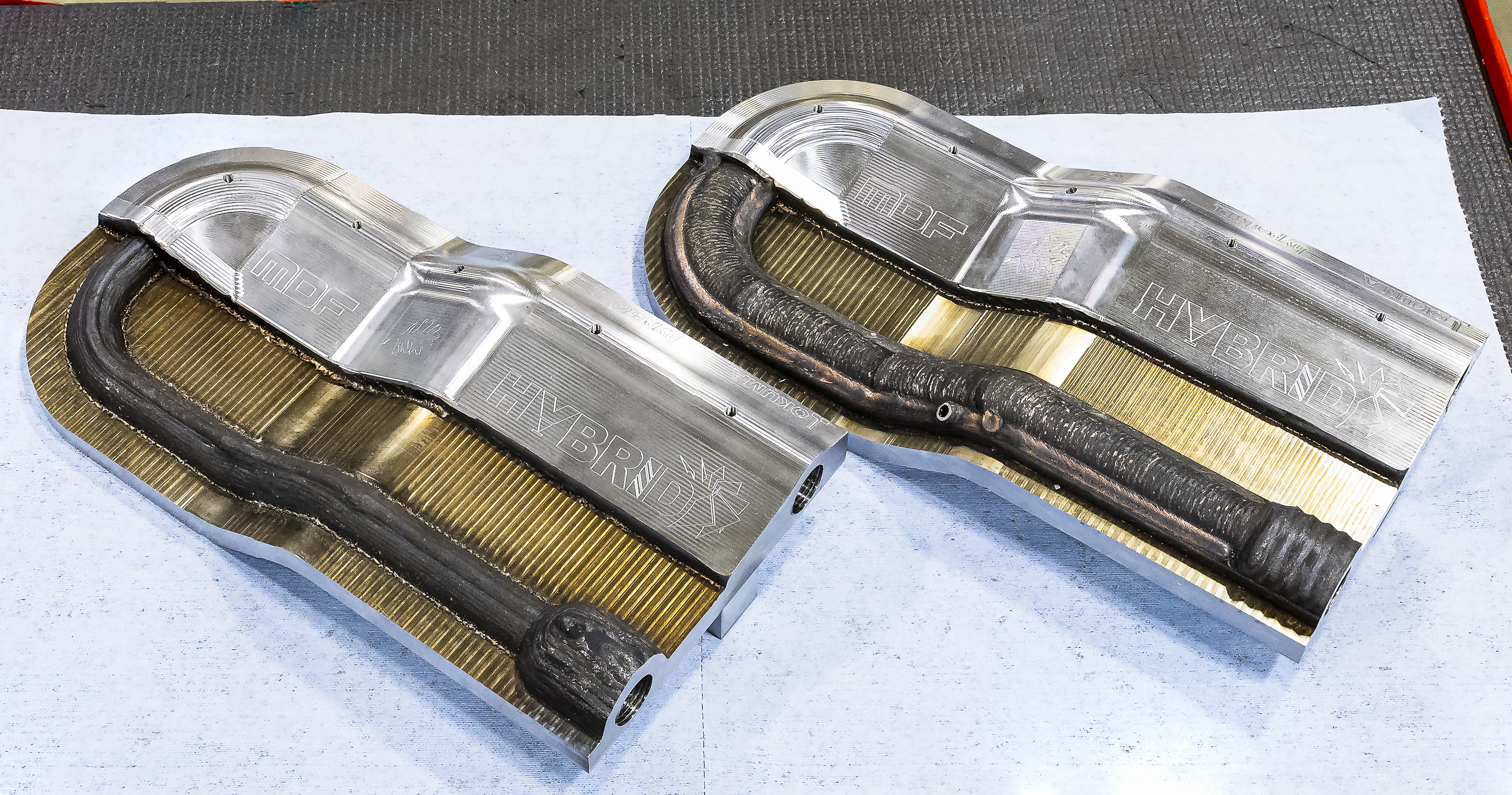
October 2023
Speedy composite manufacturing
Additive Manufacturing Compression Molding (AMCM) is developed in collaboration with Orbital Composites. The technology combines advanced and traditional manufacturing methods to produce composite-based lightweight parts for automotive applications such as battery box trays for electric vehicles. AMCM proves to be an important step forward in speedy, low emissions manufacturing.
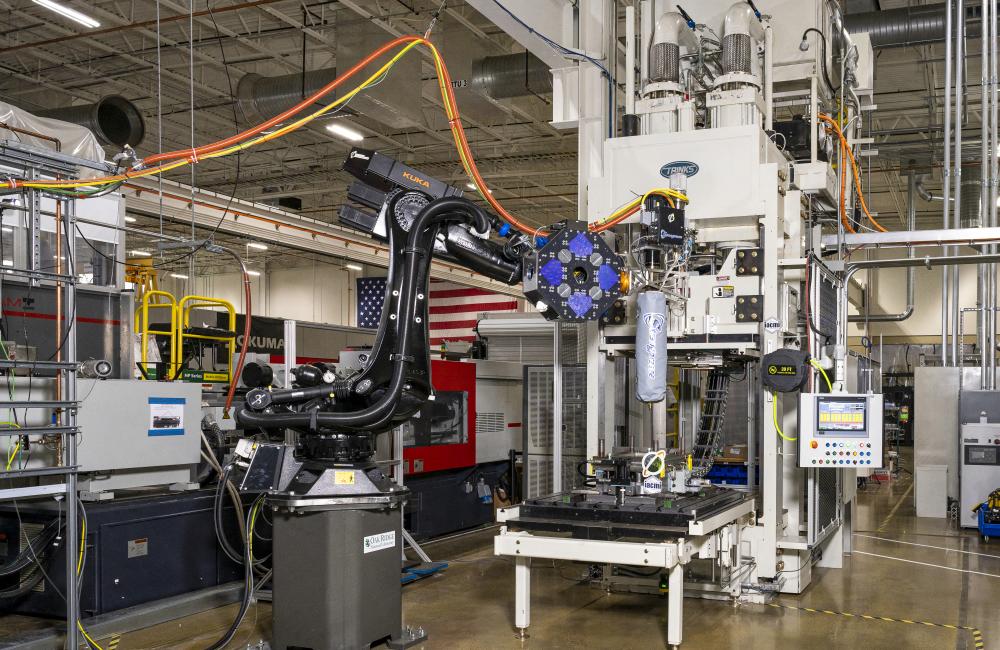
November 2023
It’s Electric!
Using additive manufacturing and compression molding, a full-scale Electric Vehicle (EV) Battery Enclosure is made from a mold less than half the size of the final product. Making parts larger than the manufacturing equipment could help companies become part of the manufacturing supply chain with minimum investment.
December 2023
A Polarizing Discovery
Magnets used in electric motors are printed for the first time and achieve up to 6,000 RPM in a 9kW motor. This technology demonstrates the feasibility of a new hybrid manufacturing process, the capability of tuning magnets for electric motors, and controlling the structural stability of the motor components.
December 2023
Steam Power in the 21st century
Researchers at MDF became the first to 3D print large rotating steam turbine blades, weighing over 25lb, for generating energy in power plants. Traditionally, the blades are forged overseas and take about 8 months to arrive in the US. However, the team at MDF prints the blades in 12 hours.
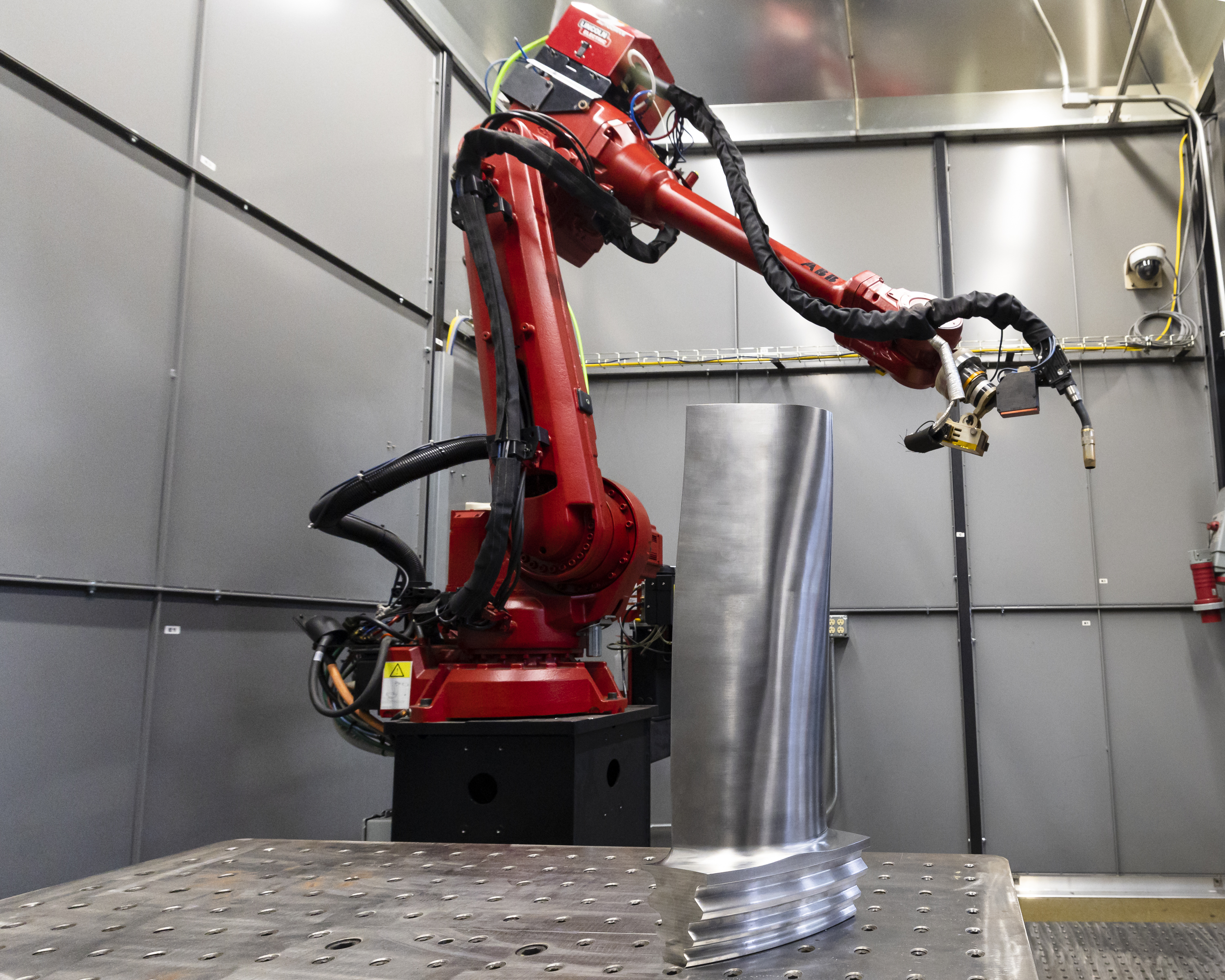
February 2024
100lb per Hour Deposition Rate
Researchers demonstrate the ability to 3D print 100lb of metal per hour in complex, geometric shapes. This advancement is another step toward significantly lowering the time and money needed to produce large-scale metal printing projects for industries such as ship and pipe building.
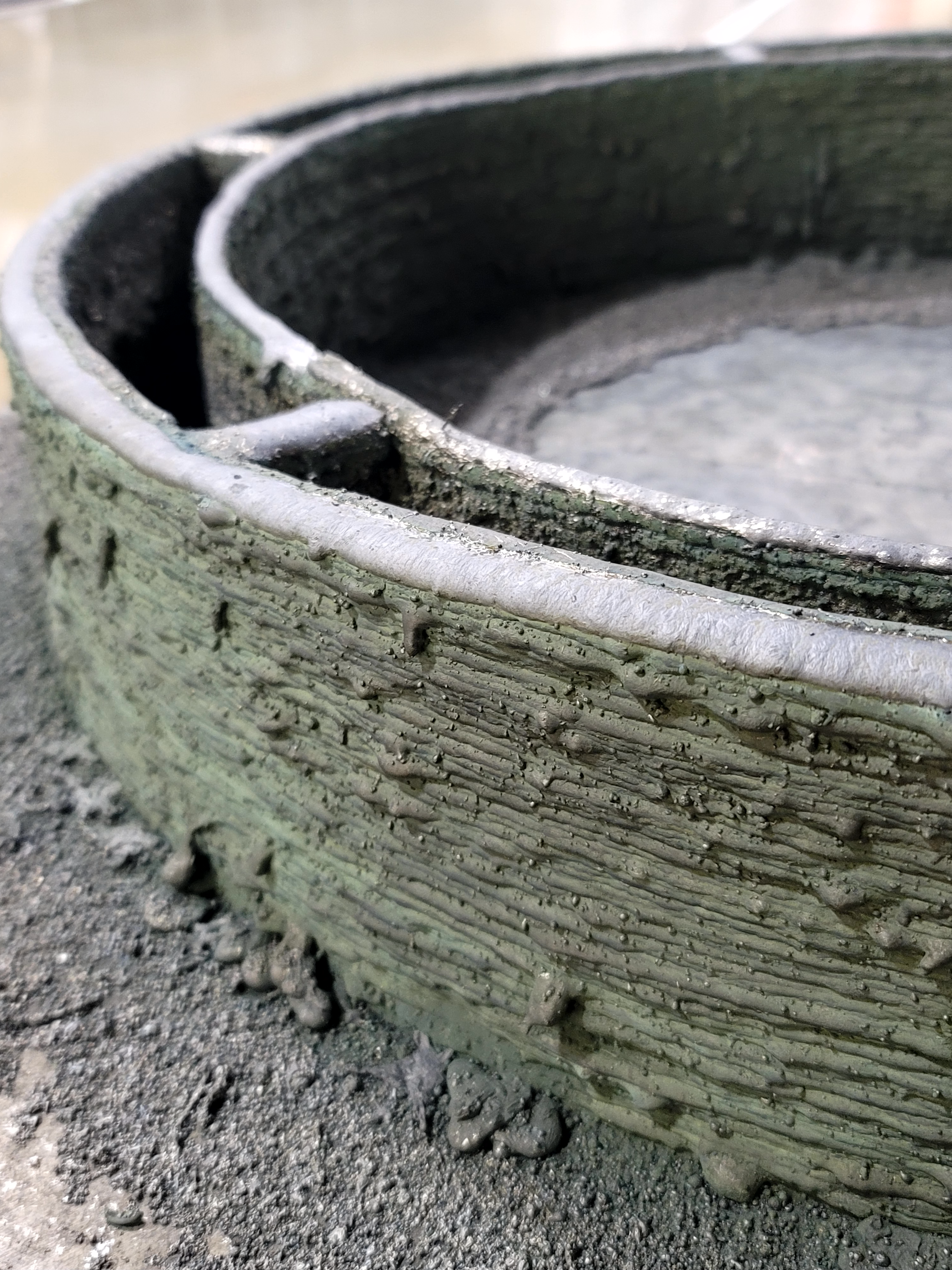
March 2024
HIP for Hydro
A wire arc manufacturing robot known as MedUSA is used to print a 900lb hydropower impeller can, which will be filled with metal powder and placed in a hot isostatic press (HIP) to solidify the material. Ordinarily, producing such cans takes months, but MedUSA completes it in just 46 hours.
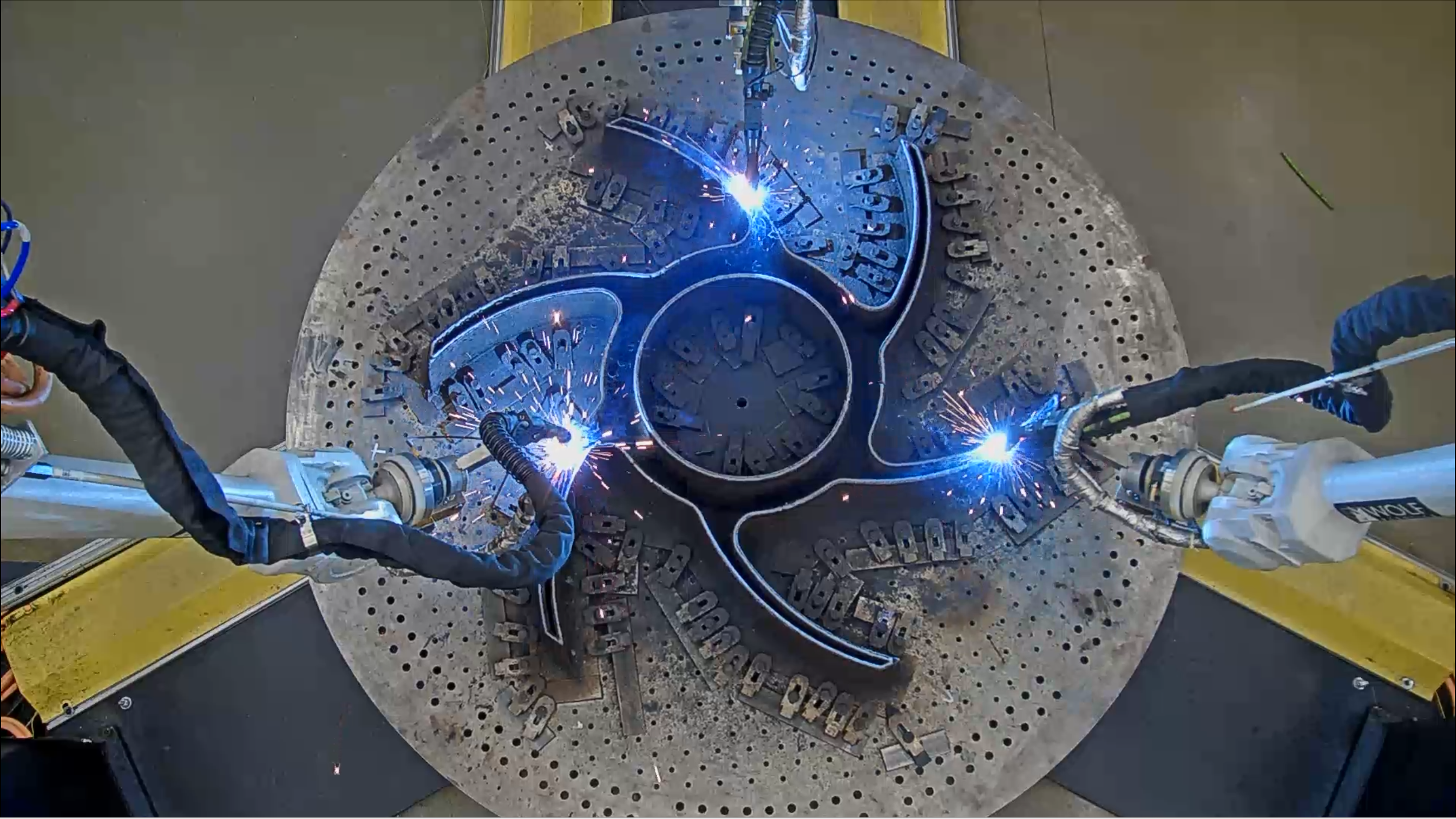