January 22, 2018 – Brian Post came to the Department of Energy's Oak Ridge National Laboratory looking for a way to combine his interests in controls engineering and robotics, and he found it at the Manufacturing Demonstration Facility (MDF), where he and his colleagues are revolutionizing 3D-printing with every improvement they make.
Post works on large-scale additive manufacturing at the MDF, a DOE Office of Energy Efficiency and Renewable Energy User Facility at ORNL. “A lot of that comes down to systems—making the machines do what humans want, from the hardware and software to embedded controls,” he said.
Post has been involved in nearly every large-scale printing project at the MDF, including multiple vehicles, a submersible, a tiny house, an outdoor pavilion, an excavator, and molds for manufacturing appliances, airplane wings, and wind turbine blades. Currently, his team is working on a mold for a 35-foot catamaran and on a large-scale, laser-based welding system for titanium aircraft parts as part of the MDF’s formal, collaborative work with industry.
“We’re building things on a scale that not many people have ever 3D-printed—we have to think carefully about how to design each component and how to build it,” Post said.
For instance, in the early days of large-scale printing, students followed the materials extruder around on the printing platform using spatulas to manually flatten the printed surface and keep it in place. To automate that process, the team created a patented technology using a reciprocating platen to serve the same function. The researchers also devised their own slicing software, which analyzes computer-aided design models for the objects to be printed and then guides the extruder on the proper path.
Post grew up in nearby Powell, Tennessee—the halfway point for his biologist parents commuting between ORNL and the University of Tennessee, Knoxville (UTK). His father, Wilfred “Mac” Post, is a retired ORNL environmental scientist who studied carbon cycles at the lab, and his mother, Susan Riechert, is a Distinguished Service Professor in Ecology and Evolutionary Biology at UTK whose specialty is arachnids.
“I always knew the lab was a place where interesting research was happening, and my parents enjoyed their work,” Post said. “But I wasn’t a biologist. I felt more like I should be building things, and, like many engineers, I grew up taking things apart and putting them back together.” In high school, he joined a technology student group that gave him the opportunity to begin thinking of engineering as a career.
Post went on to earn a bachelor’s degree in mechanical engineering at Purdue University. His interests widened as an undergrad during a summer internship with the robotics group at ORNL, where he worked with Lonnie Love, who now leads the Manufacturing Systems Research group at the MDF.
A profound influence: ORNL robotics internship, mentoring
“I worked on human amplifying machines and omni-directional vehicles that summer, and it was instantaneous: I knew that’s what I wanted to do. I wanted to build incredible things that have a purpose and a mission,” Post said.
Love’s mentoring had a profound influence on shaping Post’s academic and professional career, Post noted. He followed in Lonnie’s footsteps by continuing his studies at the Georgia Institute of Technology, earning both a master’s degree and a doctorate in mechanical engineering, specializing in dynamics, controls, and robotics. Post even ended up with the same adviser as Lonnie.
“I knew there were three ways I could use my PhD,” Post said. “I could work in the private sector, where I would solve related problems that have a big impact on the company. I could go into academia, where I would dive deep in one area and focus on that for most of my career to reach a level of expertise.
“In the middle is the national lab,” he added. “Here I work on complex and interesting challenges, and I’m not doing the same thing forever. Every 5 years you reinvent yourself, figure out where the next stage of technology is going, and how you will fit in.”
Post’s doctoral thesis focused on control of long-reach, flexible robotic manipulators, specifically associated with the robotic arm on the space shuttle orbiter. When Post came back to ORNL as a postdoc, his techniques were immediately applied as the MDF developed a robotic arm for its first large-scale additive manufacturing printer.
Now as full-time staff, Post finds engaging with his own interns very rewarding and akin to teaching as he guides them in modeling and additive manufacturing research at the MDF, funded largely by DOE’s Advanced Manufacturing Office.
Collaboration boosts materials science breakthroughs
Post also lauds the collaborative nature of the work at the lab. “We’re pulling in people from supercomputing to help us run data analytics on printed parts. We’re pulling in materials scientists who have developed new aluminum alloys” such as the cerium-aluminum alloy recently licensed to Eck Industries. “And we’re bringing others, for example, who had the idea of printing rare earth magnets,” an achievement documented in Nature Scientific Reports.
“We have experts in almost every field who make this kind of manufacturing a possibility. We’ve been able to create a system of innovation here that’s incredible to be a part of,” Post added.
One of the next big research areas for the MDF team is designing a system to strategically deposit multiple materials to create more complicated components. “We might want to move from foam to a solid to continuous fiber, then discontinuous long fiber within a single part. Or in printing an engine, we might want to deposit rare earth magnet materials in specific areas,” Post explained.
These kind of revolutionary advances “are the reason why ORNL exists,” Post said. “We have great streams of knowledge that have grown here. The origin of the lab was in creating manufacturing infrastructure to make nuclear materials. Our robotics research grew out of a need to find better ways to handle nuclear materials.”
Post added that “there’s not much about my job I don’t like,” Post said. “We handle some of the most complex and interesting challenges ever seen in engineering, often with short timelines. We try to limit ourselves to one miracle per project, but that’s a rule we break consistently.”
Post is building things away from the lab as well. He and his wife Sarah just completed a new house and had their first child earlier this month.
The MDF is supported by the DOE Office of Energy Efficiency and Renewable Energy’s Advanced Manufacturing Office. AMO supports early-stage applied research and development of new materials, information and processes that improve American manufacturing's energy efficiency, as well as platform technologies for manufacturing clean energy products.
ORNL is managed by UT-Battelle for DOE’s Office of Science, the single largest supporter of basic research in the physical sciences in the United States. DOE’s Office of Science is working to address some of the most pressing challenges of our time. For more information, please visit energy.gov/science.—by Stephanie Seay
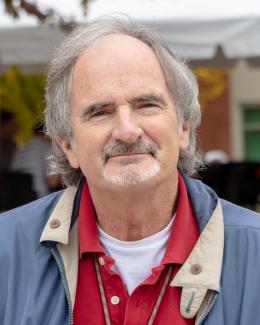