Sachin Nimbalkar may have grown up in a small town in the shadows of India’s Sahyadri Mountains dreaming of outer space, but it’s the science of conserving energy in inner space where the engineer has made his mark.
Nimbalkar, who leads ORNL’s Energy Efficiency Research and Analysis Group (EERA), became interested in science when he learned about NASA’s Apollo 8 moon mission.
“Seeing that picture of the Earth rising in space from Apollo was a driving force for me. I was going to get my engineering degree, move to the US, get my PhD and work for NASA, he said. “I am still having an impact on space, just not in the way I originally intended.”
Nimbalkar earned his bachelor’s degree in mechanical engineering from Pune University in India and came to the US in 2002 where he completed his master’s and PhD in mechanical and aerospace engineering at Rutgers University.
While he didn’t land on the moon, Nimbalkar and his team do work with corporate energy managers across the US through DOE’s Better Plants, Federal Energy Management Programs (FEMP), and Weatherization Assistance Program (WIP) – and that includes helping NASA’s jet propulsion labs with energy efficiency.
Path to ORNL
The son of an electrical engineer who worked in hydropower, Nimbalkar found his path to ORNL through his own energy efficiency project at Rutgers involving a vortex tube, a small device that splits a compressed gas stream into a cold and hot stream without any chemical reactions or external energy supply. Nimbalkar’s job was to figure out how to improve the tube’s efficiency so that it could be widely applied to a building’s heating and cooling processes.
While working on the project, Nimbalkar interacted with ORNL’s Residential, Commercial and Industrial Energy Efficiency Group and the Industrial Assessment Centers (IAC) Program, part of DOE’s Energy Efficiency and Renewable Energy, Advanced Manufacturing Office (AMO). As an IAC graduate student at Rutgers, Nimbalkar performed close to 30 IAC assessments of US manufacturing facilities in New Jersey, providing recommendations to save energy, prevent or reduce pollution and improve productivity. He also reviewed IAC engineering reports submitted by 26 IAC centers, and provided programmatic metrics and technical resources.
All of this work soon caught the attention of ORNL researchers visiting Rutgers, who in turn sparked Nimbalkar’s interest in continuing his research at a national lab. He soon joined ORNL as a postdoctoral research associate in 2008 and became full-time R&D staff for the Residential, Commercial, and Industrial Energy Efficiency Group in 2009. He later joined the Manufacturing Systems Research Group in 2013 where he stayed until he was tapped to lead EERA in 2017.
FEMP, WIP, and Better Plants are three of several DOE technical assistance programs Nimbalkar supports through his group’s work. Additional projects include AMO’s Strategic Analysis Project and AMO’s Energy Systems Software Tools and Training Project. DOE relies on ORNL’s expertise to help federal and private sector building and manufacturing plant owners reduce energy consumption.
“These DOE technical assistance programs are not about developing new technologies, but rather looking for energy efficiency potential in a systematic and holistic way, integrating resources to overcome customer barriers to action and capturing energy efficiency opportunities” Nimbalkar said.
The group’s energy efficiency technology deployment covers manufacturing sites, commercial buildings, federal facilities and residential homes.
Our team researches, analyzes and disseminates knowledge on energy efficiency to manufacturing plants and building owners across the US, helping them develop, deploy and promote impactful practices and technologies
Systematic approach, diverse settings
Nimbalkar leverages his background in fluid and thermal sciences and mechanical engineering to identify opportunities to improve energy efficiency and achieve cost savings in buildings of all types and size, specifically in the Better Plants program. The goal is to help industrial plants reduce energy intensity by 25% over a 10-year period across all US operations.
“When a company joins the Better Plants program, the first thing I do is engage with their corporate energy manager,” he said. “I’m not recreating their processes; I’m giving them a better path going forward and resources to help improve efficiency.”
DOE’s Better Plants program provides free energy assessments, in-plant trainings, access to diagnostic equipment, and energy management software tools. The DOE software tools include the online MEASUR (Manufacturing Energy Assessment Software for Utility Reduction) tool, which provides access to pumps, motors, process heating, steam and compressed air, offering more than 40 energy and equipment calculators for industries to track and monitor energy usage.
“We’re industry agnostic. However, we can have the most significant impact in the manufacturing sector,” he said. “There are more than 200 Better Plants partners in the program and to date, partners have reported that by using DOE’s energy management approaches, in-plant trainings, and tools like MEASUR, their estimated cumulative energy savings is 1.06 quadrillion Btu, which translates into cost savings of roughly $5.3 billion.”
While Nimbalkar works with diverse industries, he said that he implements a system-specific approach to improvements with each one.
“When I enter into any facility, I start thinking in terms of systems because energy support systems are the same anywhere,” Nimbalkar said. “For example, in a chemical plant, the steam system is almost similar to that in a food plant. Our software tools are system-specific and that makes it easier for us to quickly identify opportunities for efficiency improvements.”
Nimbalkar has worked with some of the largest companies in the world, but it’s making a difference in some of the smaller, family-owned companies that often brings the greatest satisfaction. Recently, he helped an Ohio-based iron and steel company achieve the ISO 50001 energy management standard, signifying that the company continually reduces energy use, energy costs and greenhouse gas emissions.
“I introduced their corporate energy manager to DOE’s 50001 Ready resources and now they’ve received national recognition for being so well structured in energy management. This was accomplished through DOE in-plant training and exposing areas for energy efficiency improvement,” he said. “Everyone wants to achieve, what I call ‘making a difference one BTU a day. No matter where I travel, the commonalities outweigh the differences.”
ORNL is managed by UT-Battelle for the Department of Energy's Office of Science, the single largest supporter of basic research in the physical sciences in the United States. DOE’s Office of Science is working to address some of the most pressing challenges of our time. For more information, please visit https://energy.gov/science.
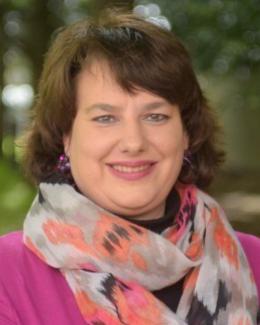