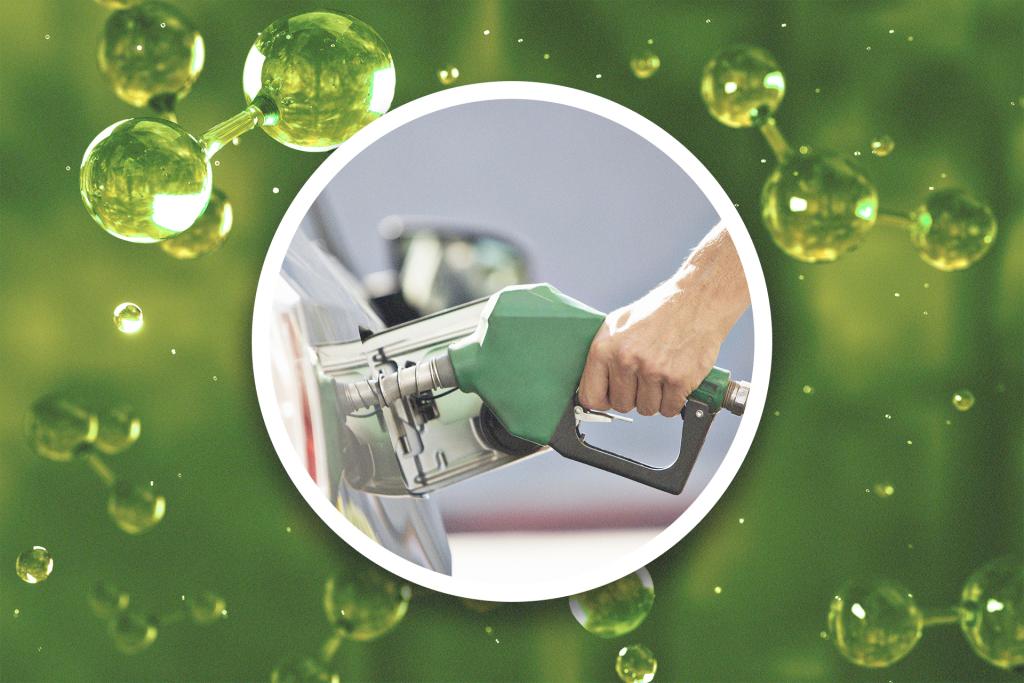
The U.S. Environmental Protection Agency has approved the registration and use of a renewable gasoline blendstock developed by Vertimass LLC and the Department of Energy’s Oak Ridge National Laboratory that can significantly reduce the emissions profile of vehicles when added to conventional fuels.
EPA approved the blending of up to 20% of the VertiGas20 green gasoline product with conventional gasoline. The low-cost, biomass-derived product is made from renewable ethanol produced by a method called Conventional Alcohol Deoxygenation and Oligomerization, or CADO, a technology originally invented at ORNL.
Ethanol is a familiar biofuel made from plants such as corn and sugar cane. It has been blended with gasoline since the 1970s to reduce reliance on imported oil and lower vehicle greenhouse gas emissions, but is currently limited to blending at 10% to 15% without vehicle modifications. Upgrading ethanol using the ORNL technology resulted in a more energy-dense hydrocarbon product that can be blended at higher quantities without changes to car and truck engines.
While ethanol’s chemical makeup includes oxygen, VertiGas20 is composed of only hydrogen and carbon, giving it properties similar to, and compatible with, petroleum-based fuels. Blending 20% of this hydrocarbon product with 10% bioethanol results in a 30% drop-in renewable gasoline. A variant of the Vertimass product currently under development could be used to help decarbonize planes, tractor-trailers and locomotive engines — heavy-duty applications where electrification options are currently limited.
In its announcement regarding the EPA approval, Vertimass indicated that use of the blendstock could eliminate 560 billion pounds of new carbon dioxide accumulation in the atmosphere as it replaces a portion of the fossil fuels required for conventional gasoline production.
The technology was licensed exclusively to Vertimass LLC in 2014, and the company then worked to scale up the process. Vertimass collaborated with ORNL, Technip Energies and DOE to optimize CADO and its novel catalyst, test it under varying conditions, analyze the technoeconomic and life-cycle sustainability of the process, and develop data for commercialization. The results demonstrated the new blendstock retains its sustainability benefits as it was scaled for commercial deployment.
Key to the conversion method is an ORNL-developed catalyst made from lower-cost metals and zeolite, a porous, absorbent mineral. Together, the new catalyst directly produces longer hydrocarbon chains from the original alcohol, in this case ethanol. ORNL replaced a traditional multi-step process with a highly efficient single-step method that requires no added hydrogen and less energy during production.
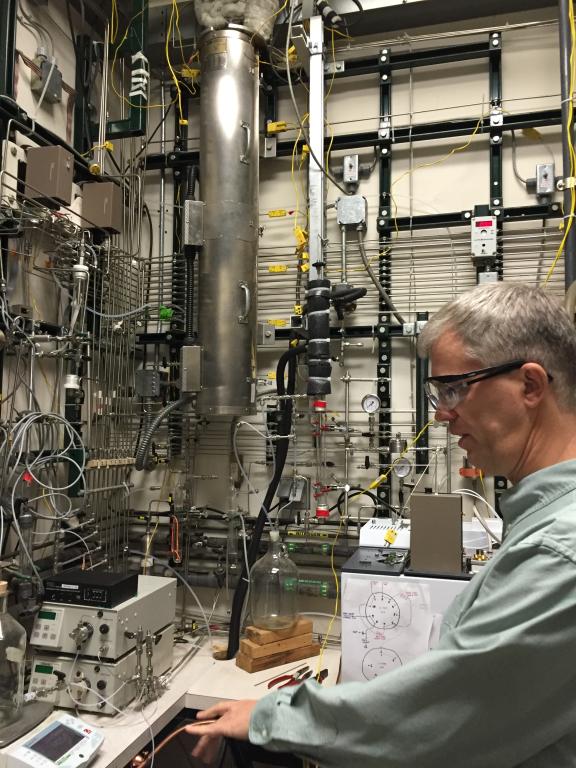
From science to success: Developing a better blendstock
The researchers demonstrated that contrary to long-held assumptions, an energy-consuming, separate intermediary dehydration step converting ethanol to ethylene was not required for the conversion. Instead, a “hydrocarbon pool” mechanism allows the zeolite-metal catalyst to directly produce longer hydrocarbon chains from the original alcohols, as described in a Nature Scientific Reports article.
“When we started thinking about better ethanol conversion to higher hydrocarbons, we had a dream list for a catalyst. We wanted stability in water so it could be used directly with biomass fermentation streams, and no precious metals or use of hydrogen to keep the cost down. We tried many different catalysts but narrowed it down to zeolite with transition metals pretty quickly,” said Brian Davison, ORNL’s chief scientist for systems biology and biotechnology and a Vertimass co-founder.
Vertimass is now ready to fully commercialize the technology. The company is also working to use the process to develop renewable propane and chemical feedstocks to decarbonize other industrial sectors, including the production of plastics, nylon, paints, and detergents. Vertimass has entered into an agreement with UGI Corporation to produce sustainable aviation fuel and propane using the technology with a goal of 20 plants over 15 years.
“Starting with technology developed at a national lab that is backed by their scientific expertise gave us an excellent starting point for refining and commercializing the technology,” said Vertimass Chief Operating Officer John Hannon. “Having that initial technology verification and intellectual property has been essential.”
Vertimass is “looking at the government’s sustainable aviation fuel (SAF) Grand Challenge of producing 3 billion gallons of SAF by 2030. There is approximately 17 billion gallons of renewable ethanol capacity in the U.S., providing an excellent platform on which to apply the novel Vertimass technology and rapidly help achieve these targets,” Hannon said. “Vertimass is eager to bring more low-carbon liquid fuels to market to help meet those goals.”
The work was also made possible by the interdisciplinary nature of the national lab environment, Davison said.
“The DOE national labs bring together people who think of solutions no one has thought of before,” Davison said. “In this case, the invention would not have happened without conversations between scientists from multiple disciplines under one roof who knew each other’s skills and interests and were able to articulate questions and potential solutions. We’re also good at persistence, engaging in the long handoff from a laboratory-level process to a higher technology-readiness level for greater impact. The goal is to assist industry in the development of an entire supply chain based on sustainability.”
The catalyst was developed and analyzed using the world-class characterization and materials synthesis capabilities of the Center for Nanophase Materials Sciences at ORNL, a DOE Office of Science user facility. The project was supported by the BioEnergy Science Center at ORNL, which is funded by the DOE Biological and Environmental Research program; by the DOE Office of Energy Efficiency and Renewable Energy’s Bioenergy Technologies Office; and ORNL’s Laboratory-Directed Research and Development program.
UT-Battelle manages ORNL for the Department of Energy’s Office of Science, the single largest supporter of basic research in the physical sciences in the United States. The Office of Science is working to address some of the most pressing challenges of our time. For more information, please visit energy.gov/science. — Stephanie Seay