When Scott Smith looks at a machine tool, he thinks not about what the powerful equipment used to shape metal can do – he’s imagining what it could do with the right added parts and strategies. As ORNL’s leader for a newly formed group, Machining and Machine Tool Research, Smith will have the opportunity to do just that.
When Scott Smith looks at a machine tool, he thinks not about what the powerful equipment used to shape metal can do – he’s imagining what it could do with the right added parts and strategies. As ORNL’s leader for a newly formed group, Machining and Machine Tool Research, Smith will have the opportunity to do just that.
“Could we have some features on the additive parts that make the machining process easier, and thereby make the total cost less?” he asked. “We should be able to include stiffening features, clamping features, locating features, and so on. I think the possibilities for this are infinite.”
Based at DOE’s Manufacturing Demonstration Facility (MDF) at ORNL, Smith will focus on how to include subtractive capabilities with additive manufacturing machines, providing the opportunity for the manufacturing of a part and the subsequent needed machining, shaping or fine-tuning to occur within one system or using a combination of equipment.
It’s an opportunity for him to have a positive impact on manufacturing in the US, specifically from an economic perspective.
Three goals: improve, design, build
The ability to investigate the capabilities of additive machines and answer this question is what drew Smith to ORNL. He left his 23-year career in academia at the University of North Carolina in Charlotte, where he served as a professor and department chair, leading the mechanical engineering program for nine years, to join the national laboratory.
With the MDF, ORNL has a huge presence in additive equipment. This is the place to be, and I want to be the subtractive guy in additive land
In order to integrate subtractive capabilities into the world of additive, Smith outlines what he calls the “three big themes.”
“First we focus on how to improve existing machine tools,” he explained. “Then, we begin to design the ideal machine tool, explore what the machines should look like based on the parts we want to make. Finally, we start to build up a workforce that can support our innovation.”
Workforce development will be a big part of Smith’s first year as a new group leader at ORNL. He’s responsible for recruiting and building the team that will support machine tooling efforts. He intends to fill his team with postdocs and graduate students to early-career researchers who can be the new generation of machine tool users, machine tool designers, software developers, entrepreneurs, and manufacturing thought leaders.
“These are the people that are going to come up with new materials and processes,” he said. “They may go on to start their own company, but they’ll begin here at the laboratory, changing the game for machine tools.”
Innovation takes flight
Back in the 1990s, Smith himself was a new generation game-changer. Growing up in Cookeville across the street from Tennessee Tech University where his father was a professor in earth sciences, Smith says he knew early on that he wanted to be an engineer even before he knew what an engineer was.
“I liked making things and problem-solving,” he said. “Engineering is about creation and about decision making. You’re forced to make decisions in the time available and with the information you have, and then move on. And, I like that. I’ve always liked that.”
Smith wasted no time in deciding his career path. He chose to take advantage of a Tennessee Tech scholarship, taking the short commute and a direct path to obtaining his bachelor’s degree in mechanical engineering. After graduating he continued with graduate school at the University of Florida in Gainesville, because at that time in the mid-1980s, the school was gaining attention for its robotics program.
“It was an exciting place for engineers to be,” Smith said. “I thought I was going to work in robots, but then I realized I didn’t like it as much as I thought I was going to. I was thinking about changing schools and going in a different direction, but that’s when I met a professor who was a machine tool researcher. He offered me a job, and I took it; it turned out I really liked machine tools, and I never looked back.”
Smith went on to complete his PhD and join the faculty at Florida, focusing research efforts on the dynamics of machine tools, vibrations and machine design. On a sabbatical leave, Smith worked at the University of North Carolina at Charlotte to learn about metrology or the science of measurement.
“I knew if I was going to be successful in machine tools, I had to understand measurement,” Smith said. “I spent nine months there in metrology, came back to Florida when my sabbatical ended, and then Charlotte called with an attractive job offer as a machine tool researcher, so I turned around and went right back.

Since that time, Smith’s been awarded several patents for his inventions, and he’s one of 17 US fellows elected to the International Academy for Production Engineering. Smith has also been honored by the American Society of Engineers with the William T. Ennor Manufacturing Technology Award for creating thin monolithic machined structures, commercially used today in the airline industry.
The monolithic components are what Smith credits as his biggest accomplish to date.
“You used to have to bend sheet metal, drill holes in it, attach pieces by rivets to build the structures for planes out of the sheet metal pieces,” he said. “I was approached by McDonnell Douglas and the Air Force to figure out how to use high speed machining to make thin monolithic parts to replace the sheet metal. We got rid of the rivets, all of the assembly tools and we reduced the weight of the piece. It turns out, it was possible to make these really exquisitely thin monolithic aluminum components.”
Machine tooled components drastically reduced the cost of the part, because the need for hand labor was eliminated.
“The cost was all in the labor; it was in all the special tooling, the storing of it, all the assembly operations, the drilling, and the weight of the rivets, and so on,” Smith said. “So, it essentially changed a manufacturing process, and this was in the early 1990s. Today, if you’ve flown on an aircraft, it has these types of components in it, from the wings to the bulkheads and even to the seat mount.”
While the thin aircraft parts might have garnered the most attention in Smith’s career, it’s not the only innovation of note. Any machine tool operator that’s used a device called the “Harmonizer” has Smith to credit for it. His doctoral work led to the development of the device that stops the vibration or chattering in a machine tool.
“I developed a way to capture the sound of the machine tool with a microphone, and then the piece of software that tells you what speed to change the machine to in order to stop the vibration,” he said.
Smith’s knack for figuring out machine mechanics is in evidence all around him in his office that overlooks the equipment high bay at the MDF. He’s brought several aluminum parts in varying shapes and sizes with him as reminders of his decades of pioneering machine tool research.

“Think about a flat piece of aluminum,” Smith explained. “If I’m going to make this type of part additively, it would be helpful to have some feature in there that allows me to hold it, so maybe I put a lip on it, so I can then add a clamp to the piece and that makes this part sturdier and stiffer. And then maybe I can put some features on the part that makes it easy to accurately find the workpiece, that would be called the fiducial mark. Now if I take this marker from one machine to another, I can pinpoint exactly where to begin cutting, and I save time and cost and material waste, too.”
According to Smith, these type of machining innovations are possible with the right additive machines to experiment on and those machines are at the MDF.
“We’re going to focus on the development and deployment of simple, intuitive tools built on machining science, to make it easier for machine tool users to quickly find the best cutting conditions for their system, and to know those conditions at the time the part program is written,” he said.
“I see what I'm doing at the MDF as a really strong complement to what's already here,” he said. “And I think there is room for a lot of growth in this area. It's important to DOE, to the Department of Defense, and to industry. I’m here because I think what we’re doing in manufacturing is good for the country.”
ORNL is managed by UT-Battelle for the Department of Energy's Office of Science, the single largest supporter of basic research in the physical sciences in the United States. DOE’s Office of Science is working to address some of the most pressing challenges of our time. For more information, please visit https://energy.gov/science.
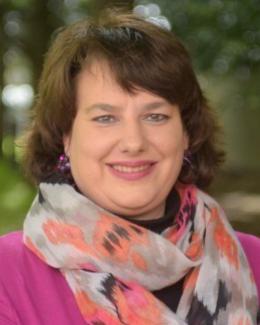