A new convergent manufacturing platform, developed in only five months at the Department of Energy’s Oak Ridge National Laboratory, is debuting at the International Manufacturing Technology Show, or IMTS, in Chicago, Sept. 9–12, 2024.
The technology, called Future Foundries, opens the door for hundreds of thousands of small- and medium-sized companies to join the convergent manufacturing revolution, according to ORNL researchers. It is a cutting-edge platform that integrates multiple advanced manufacturing systems into a single, agile platform.
“The democratization of manufacturing will be a key component to keep U.S. manufacturers internationally competitive,” said ORNL’s Chief Manufacturing Officer Craig Blue. “The convergent manufacturing approach we are demonstrating at IMTS is a significant step toward realizing this vision. It has the potential to enable the expansion of domestic supply chains by enabling small companies to have significant impacts in a broader range of products.”
Around 400,000 U.S. manufacturing companies employing more than 15 million people compete globally, with more than 80% of those companies small- or medium-sized. Scalable, flexible and cost-effective, Future Foundries levels the playing field for those companies.
“This is a game-changer,” said Thomas Feldhausen, R&D staff member in ORNL’s Disruptive Manufacturing Systems Development group and principal investigator for the initiative. “Convergent manufacturing platforms significantly reduce production times, enhance material properties and streamline the transition from prototype to deployment.”
In the past 20 years, the U.S. has lost 40% of domestic casting abilities to overseas facilities. Future Foundries offers a way to supplement existing U.S. casting facilities and, in doing so, help increase domestic production of critical energy components to help the country achieve its clean energy goals. This technology will also help strengthen the U.S. manufacturing base and support national security.
Multiple systems for many products
In Booth 236700 (North Building, Level 3, Emerging Technology Center) at IMTS, Future Foundries demonstrates wire-arc additive manufacturing, heat treatment, inspection and machining systems that are physically connected by a pallet changer that moves components between each of the systems. A smart manufacturing thread interconnects the entire platform, enabling communication between each robotic system and providing data to operators that can speed up production and inform future process improvements.
Core industry partners include Okuma and Fastems, which have provided both equipment and staff to help bring the platform together with ORNL’s team.
“This collaborative effort will provide attendees a glimpse at what can be done when talented engineers from several companies come together to demonstrate the future of manufacturing,” said Bob Baldizzi, Fastems sales manager. “Additive manufacturing technology has grown leaps and bounds in the last few years, but combining it with subtractive manufacturing and automation is quite a unique approach. Our automation solutions and dynamic scheduling software are a perfect fit for this application.”
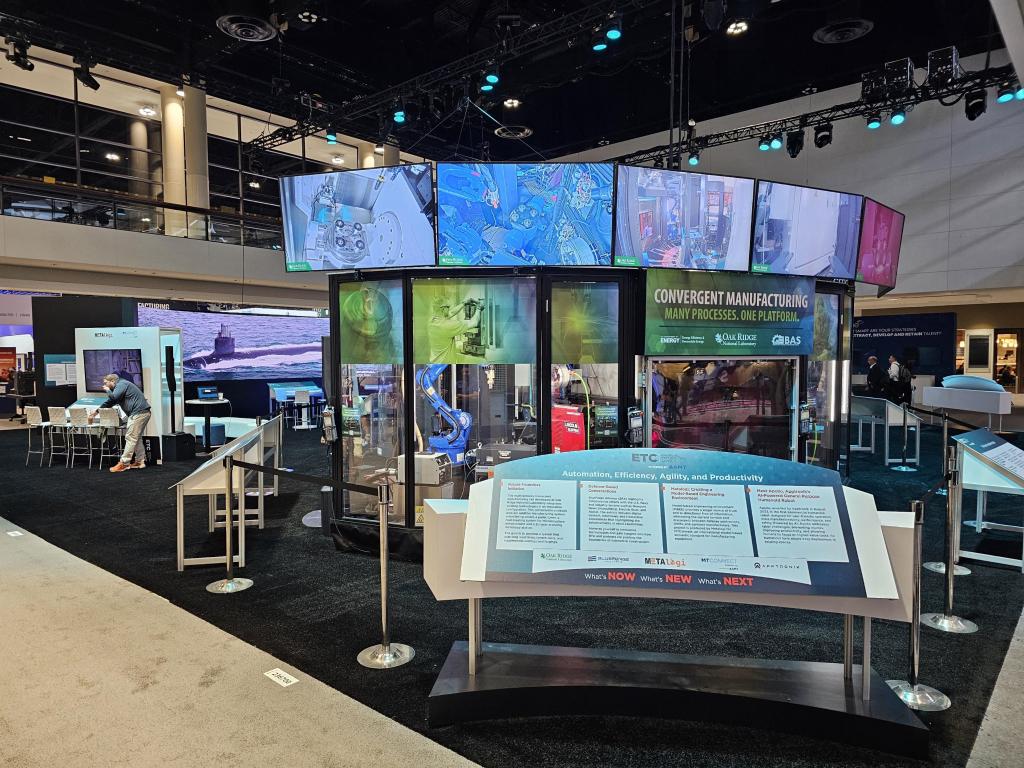
ORNL will demonstrate the platform’s agility by running three demonstrations simultaneously — the repair of a wind turbine gear; the production of a component using readily available materials that typically would be cast; and the creation of six unique challenge coins, each made daily from the same injection mold. The platform makes variability of each mold possible.
“Now manufacturers can be adaptable,” Feldhausen said. “If you have a machine shop and you have to change something in your process, you no longer have to start from the ground up. This is modular, so you can easily change out different aspects. We’re presenting a solution with unprecedented modularity, flexibility, connectivity, reconfigurability, portability and customization capabilities.”
A history of “MDF Moonshots” at IMTS
ORNL’s manufacturing program has a reputation for cutting-edge, high-impact results with a long line of emerging technologies, or “moonshots,” that have been displayed at IMTS. A decade ago, the lab collaborated with Local Motors and Cincinnati Incorporated to print, machine and assemble a fully operational car, called Strati, in real time at the trade show.
“Moonshots like the Strati and, now, Future Foundries underscore the innovative nature of the MDF for bringing together multidisciplinary research teams to solve complex challenges in collaboration with industry,” said Ryan Dehoff, Manufacturing Demonstration Facility, or MDF, director. “The MDF takes strategic risks so industry doesn’t have to, and we demonstrate what’s possible through the development of advanced manufacturing technology platforms of the future like Future Foundries.”
Printing the Strati demonstrated what could be possible through big area additive manufacturing, or BAAM, another ORNL-developed technology. The event 10 years ago, along with subsequent technology advancements, helped launch today’s thriving global large-scale polymer printing industry.
To celebrate the 10th anniversary of Strati’s printing, the car will be on display at the outside entrance to IMTS at McCormick Place in Chicago all week.
Future Foundries was developed by a 40-plus-member, cross-disciplinary team at MDF that started work on the platform in April 2024. Following the IMTS show, the platform will return to MDF at ORNL where it will continue to serve as a foundation for ongoing research and development of convergent manufacturing technologies in support of U.S. industry. A 3D animation of the technology is available here.
The MDF, supported by DOE’s Advanced Materials and Manufacturing Technologies Office, or AMMTO, is a nationwide consortium of collaborators working with ORNL to innovate, inspire and catalyze the transformation of U.S. manufacturing. Funding for the platform is provided by AMMTO, as well as the Department of Defense Industrial Base and Analysis and Sustainment program.
UT-Battelle manages ORNL for DOE’s Office of Science, the single largest supporter of basic research in the physical sciences in the United States. DOE’s Office of Science is working to address some of the most pressing challenges of our time. For more information, visit energy.gov/science. — Lawrence Bernard