Jonathan Harter, a technical professional in ORNL’s Energy Science and Technology Directorate, uses a robot and other automated methods to disassemble electric vehicle batteries for recycling or reuse in the electric grid. Credit: Carlos Jones/ORNL, U.S. Dept. of Energy
After being stabilized in an ambulance as he struggled to breathe, Jonathan Harter hit a low point. It was 2020, he was very sick with COVID-19, and his job as a lab technician at Oak Ridge National Laboratory was ending along with his research funding.
“It was a weird situation where I felt a little bit powerless — again. I thought, ‘If I don’t create an opportunity for myself, I’m done,’” he said.
Harter had been in challenging spots before. A first-generation college student from the local Tennessee hamlet of Walland, Harter was selected for an ORNL robotics internship in 2016 that helped pay his way through nearby Pellissippi State Community College. When the internship ended, he had to convince his ORNL supervisor to fund him for the first time through another internship.
It worked, and Harter has continued tackling tough challenges at ORNL ever since. His initiative and perseverance have frequently enabled him to turn dead ends into possibilities. Today he is a technical professional in the Energy Science and Technology Directorate, specializing in electronics recycling and high-voltage technologies.
“I knew I could learn quickly. I just needed a few people to believe in me and trust me to do important things,” said Harter. “If you throw me into the fire, I figure it out.”
The first to hand Harter a big assignment was now-retired ORNL senior researcher Tim McIntyre, who was developing automation processes and controls for recovering critical materials from hard drives and electric vehicle, or EV, batteries. Harter credits McIntyre with providing him opportunities as an intern for meaningful responsibility and research, including developing projects and inventing disassembly methods and processes.
After Harter became a lab technician, McIntyre helped him improve his technical communication skills by sharing presentation and reporting duties. McIntyre encouraged Harter to act as a liaison with recycling companies to learn more about their needs, the technology they might adopt and details of their business operations. In many cases, companies indicated they were shredding entire batteries or hard drives for disposal without separating components for reuse.
Automated disassembly is safer and improves the quality and value of extracted materials such as copper and aluminum. “We like to talk about recovering the value instead of recycling,” said Harter, who earned two patents in the process.
McIntyre and Harter demonstrated the fast, efficient recovery of rare earth magnets from hard drives for direct reuse, which is the goal for both profitability and environmental benefit. They also developed automated processes to recover materials and components from EV drivetrains and automotive lithium-ion batteries. The heart of the process is a large six-axis industrial robot arm with custom tooling. The duo chose an older, off-the-shelf robot to show that the process could be affordable for scrap shops, enabling more widespread adoption of advanced recycling. The robot’s pivoting, bright blue arm, with an “elbow” that bends above Harter’s head, is guided by a controller and machine vision as it unscrews the bolts on an energized EV battery assembly.
For Harter, who takes all the safety training he can, working with the automated robot was appealing partly because its use could protect workers in salvage yards and maintenance shops from handling dangerous voltages.
Harter still hadn’t given up on the classroom. Educational and career guidance during high school and college were scarce. Although he had completed associate’s degrees in electrical engineering technology and industrial automation, Harter discovered he had not been in the right academic track to transfer to the University of Tennessee.
He persevered, playing catch-up by taking more courses while working full time. But then the automation projects began winding down and McIntyre retired. That’s when Harter came down with COVID while considering job options. He was finishing project reports when he got the call from Madhu Chinthavali, then a group leader in ESTD. Chinthavali had taken note of Harter’s initiative and offered him the chance to try a new research direction.
“He learns fast,” said Chinthavali, now head of the Energy Systems Integration and Controls Section. “This environment needs people like him, because when research morphs, he has the aptitude and mindset to adapt to those needs and take full ownership of the things he’s responsible for.”
Working on power electronics, Harter began creating a test bed for grid systems components and adding automation capabilities to the Grid Research Integration and Deployment Center, or GRID-C. But he also helped stand up the facility during the COVID shutdown with the help of only a few colleagues working on-site.
“That’s what’s really fun about this place: I get to do some grunt work, which I enjoy, and I also get to develop lab space and invent new technology,” said Harter, who has also worked jobs in construction, remodeling and carpentry. “I can take the initiative to pursue the things I want.”
Now a technical professional after completing his bachelor’s degree last year, Harter is recycling his own skills by applying his high-voltage knowledge to automation. Today he leads a multifaceted new series of projects related to automated recycling of lithium-ion batteries, which is vital to ensuring environmental benefit throughout their life cycle and beyond.
For example, Harter is focusing on advanced diagnostics to identify individual or failing cells among the hundreds to thousands inside a single EV battery stack. And because used batteries often still retain useful capacity — even if not enough to run a car — Harter is developing methods for combining them to build residential energy storage units. These battery clusters could provide a secondary home energy source when high demand causes a spike in electricity prices, such as during heat waves.
“I’m excited that automated battery disassembly is finally starting to be recognized more widely as an important opportunity,” Harter said. “I can’t wait to develop new tooling to defeat certain joining technologies, take batteries apart really fast, and put together all the automation pieces. That is going to be fun.”
UT-Battelle manages ORNL for the Department of Energy’s Office of Science, the single largest supporter of basic research in the physical sciences in the United States. The Office of Science is working to address some of the most pressing challenges of our time. For more information, please visit energy.gov/science.
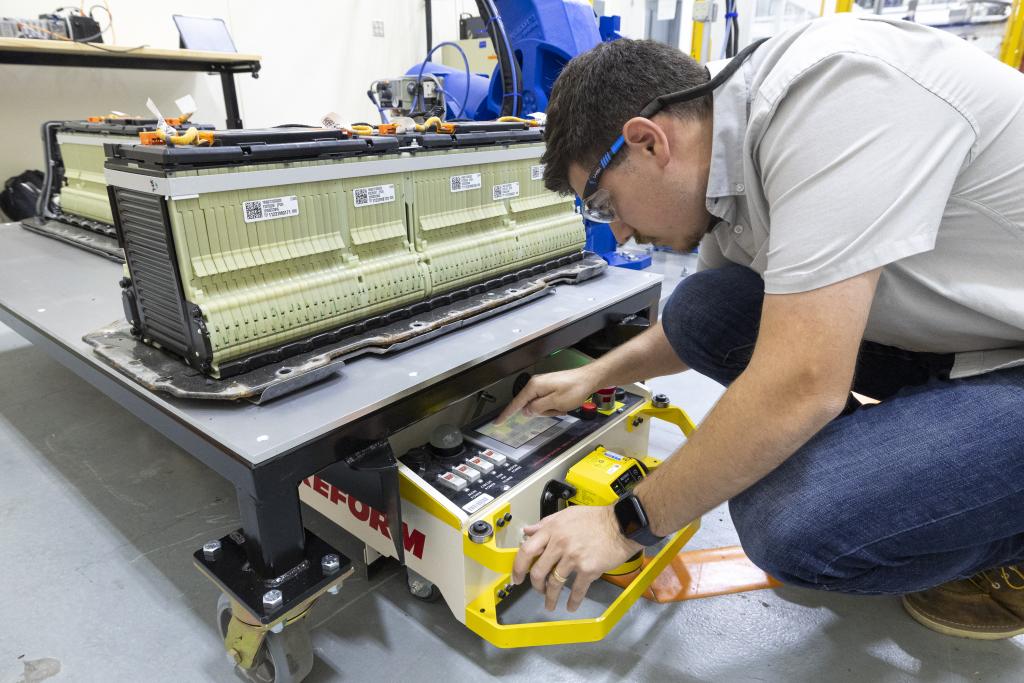