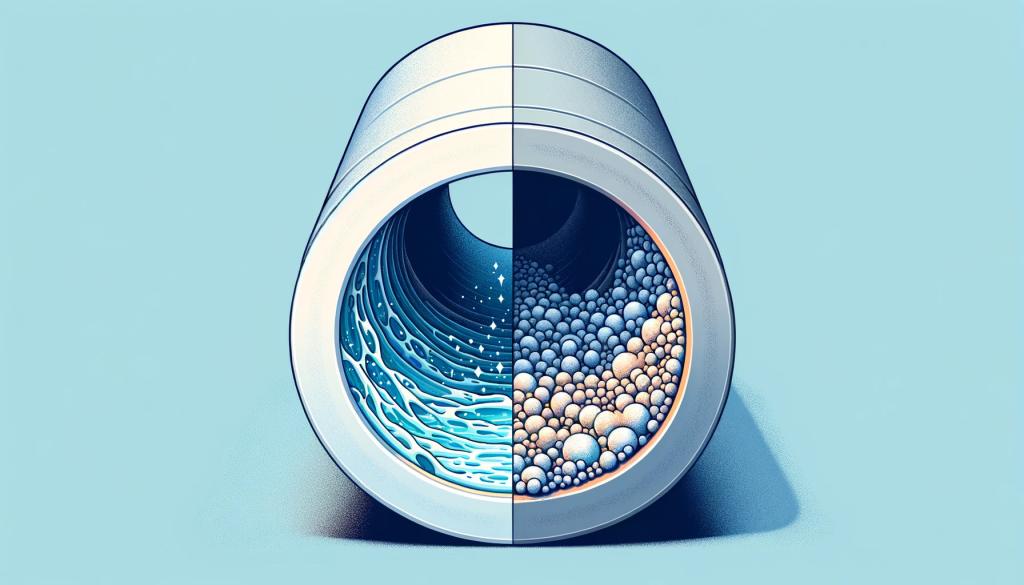
Collaborative research that combined experiments at Yale University and molecular dynamics simulations at the Department of Energy’s Oak Ridge National Laboratory provides new insights into solving a major technical obstacle to efficient and sustainable industrial operations.
Silicon is the second most abundant element in the Earth’s crust, and in natural water sources it is commonly found in the form of dissolved silicic acid. Under certain pH and temperature conditions in industrial feed water, the acid can become oversaturated and insoluble, precipitating a substance, called silica scale, that encrusts equipment. This unwanted coating fouls the surfaces of various engineering systems, such as reverse osmosis desalination water-treatment membranes, heat exchanger components and plant pipelines.
“One way to combat the silica is to adjust the pH of the water, but this process is quite expensive and makes other forms of inorganic scaling, such as gypsum and calcite, worse,” said ORNL’s Vyacheslav “Slava” Bryantsev. “Recently, people have been using silica-inhibiting polymers, or antiscalants, all of which are proprietary. We know these antiscalants are possibly a class of polyamine-type systems that somewhat impede silica scaling, but how they work and how to improve on their existing properties have been poorly understood.”
Previous studies on the performance of polymeric silica antiscalants have varied widely from hindering to accelerating the formation of silica scale. “Ours was the first systematic investigation into the role of molecular structures and functional groups of polymeric antiscalants in stabilizing oversaturated silicic acid solutions,” Bryantsev said.
A paper titled “Molecular Design of Functional Polymers for Silica Scale Inhibition” published in Environmental Science & Technology provides details of the study.
The Yale scientists synthesized a series of nitrogen-containing polymers as silica antiscalants and tested their performance in an oversaturated silicic acid solution. They discovered enormous differences in effectiveness among similar types of antiscalants.
“Working closely with our colleagues at ORNL, we were able to determine that the variations were due to the specific physical and chemical properties of the polymers,” Yale’s Masashi Kaneda said. “The approach and the outcome are notable because we provided an understanding of the mechanisms involved in mitigating silica scaling through the use of polymeric antiscalants in water treatment processes.”
A polymer is a large molecule composed of repeating units, called monomers, that are linked together by chemical bonds to form a structural chain, or backbone. As monomers containing functional groups engage in a polymerization reaction, they merge into a larger polymer, imparting distinct functionalities to the resulting structural chain.
Water-soluble chemical compounds called amines and amides are incorporated into polymers to form antiscalants because of their ability to stabilize and suspend silica. When a positively charged hydrogen ion is added to an amine molecule, the amine is said to be protonated. Protonation can increase the molecule’s water solubility and reactivity.
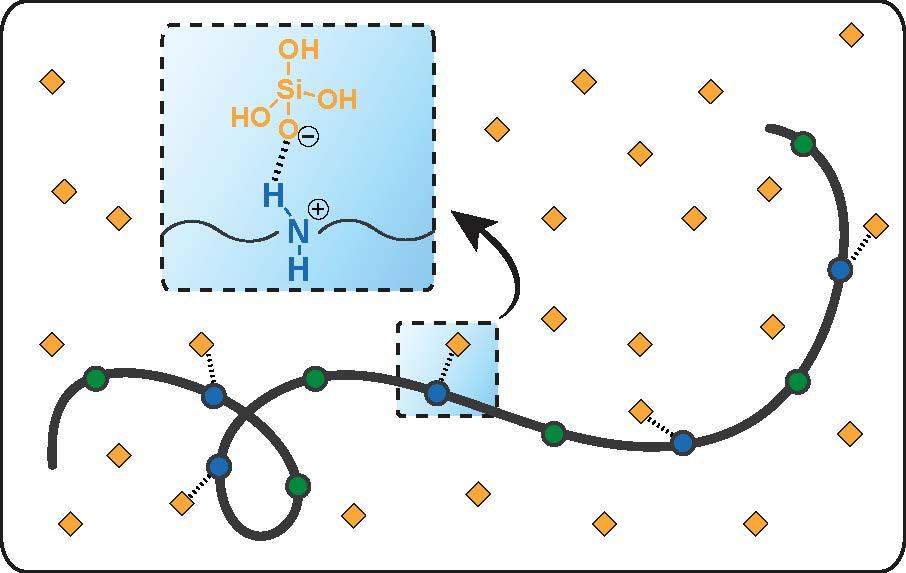
In the Yale-ORNL study, the scientists discovered that polymers with charged amine and uncharged amide groups in their backbones exhibit superior silica scale inhibition performance, retaining up to 430 parts per million of reactive silica intact for eight hours under neutral pH conditions. However, monomers of these amine- and amide-containing polymers, along with polymers containing only amine and amide functionalities, presented insignificant inhibition.
“We needed to answer why the polymers we designed for the experiment worked, while the monomers did not,” said ORNL’s Deng Dong. “To identify the design parameters, we conducted molecular dynamics simulations that we believed would enable us to understand the mechanisms behind the phenomena.”
The simulations revealed strong binding between the deprotonated silicic acid and a polymer when the amine groups in the polymer were protonated.
“ORNL’s contribution enabled us to discover that certain functional groups in the polymer chain synergistically contribute to the scale inhibition process,” said Yale’s Mingjiang Zhong.
Zhong added that silica scaling is quite different from other scaling processes.
“Although current efforts are focused on solving the silica scale problem through the water-treatment process, the ideal case will be to add one type of antiscalant to inhibit all types of scale formation, not just silica,” Zhong said. “However, to the best of our knowledge, so far there is no such antiscalant. The molecular understanding we gained from our research will guide us toward discovering a universal solution.”
This study was supported by the National Alliance for Water Innovation, funded by DOE’s Office of Energy Efficiency and Renewable Energy, Industrial Efficiency and Decarbonization Office. This research used resources of the Oak Ridge Leadership Computing Facility at ORNL and resources of the National Energy Research Scientific Computing Center located at Lawrence Berkeley National Laboratory. The OLCF and NERSC are DOE Office of Science user facilities.
UT-Battelle manages ORNL for DOE’s Office of Science. The single largest supporter of basic research in the physical sciences in the United States, the Office of Science is working to address some of the most pressing challenges of our time. For more information, please visit energy.gov/science. — Scott Gibson