Project Details
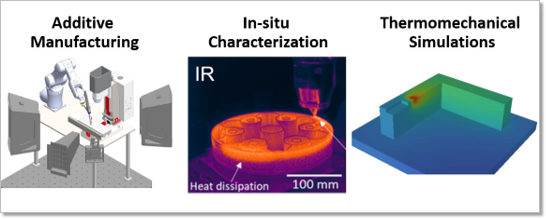
Oak Ridge National Laboratory is taking the 3D printing revolution to even greater heights.
ORNL is developing an autonomous additive manufacturing lab, accelerating the ability to print complex metal components that can be used with confidence in safety-critical applications such as aircraft and clean energy generation. Through an INTERSECT Self-Driven Processes, Experiments, Laboratories (SPEL) project, researchers are creating an autonomous system to adaptively control the additive manufacturing (AM) printing process using state-of-the art robotics, in-situ characterization, simulations, and applied math methods.
By lowering the barriers for coordinating once-siloed resources across ORNL, INTERSECT is transforming the possibilities for collaboration and greatly increasing the speed of discovery. Rather than running one experiment using the resources of one facility, researchers can now leverage the full spectrum of resources available across the lab at once in a single experiment.
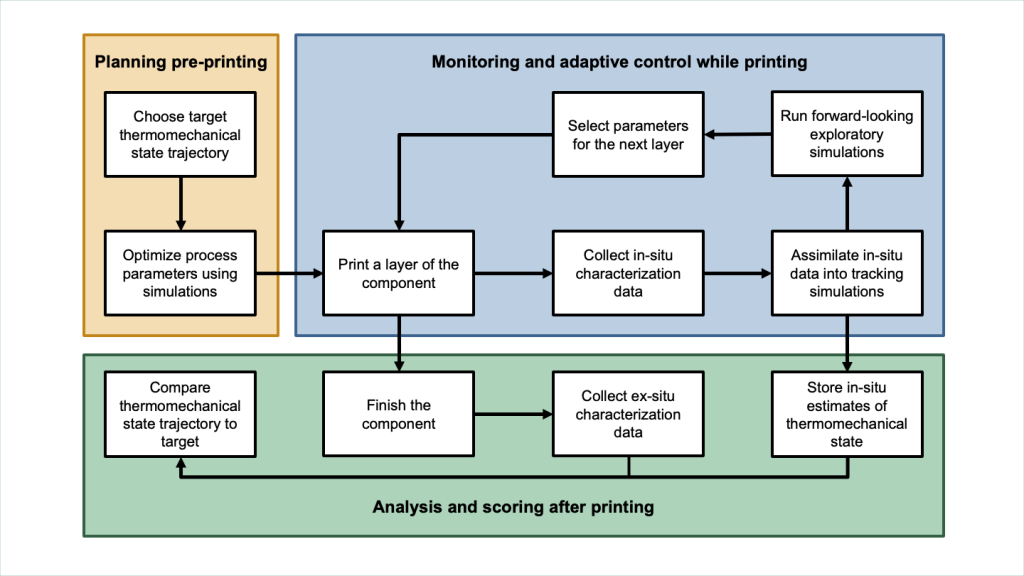
The autonomous additive manufacturing system uses INTERSECT technologies to pull together the combined capabilities of three ORNL user facilities: the Manufacturing Demonstration Facility (MDF), the Oak Ridge Leadership Computing Facility (OLCF), and the Spallation Neutron Source (SNS). The result is a powerful research platform that ORNL scientists can use to enable the deployment of crucial clean energy infrastructure components such as hydropower turbines.
Through the diverse set of INTERSECT microservices, ORNL is leading the way to improve interconnected workflows for critical scientific capabilities that continue to advance the future of additive manufacturing.
