Invention Reference Number
Licensing Contact
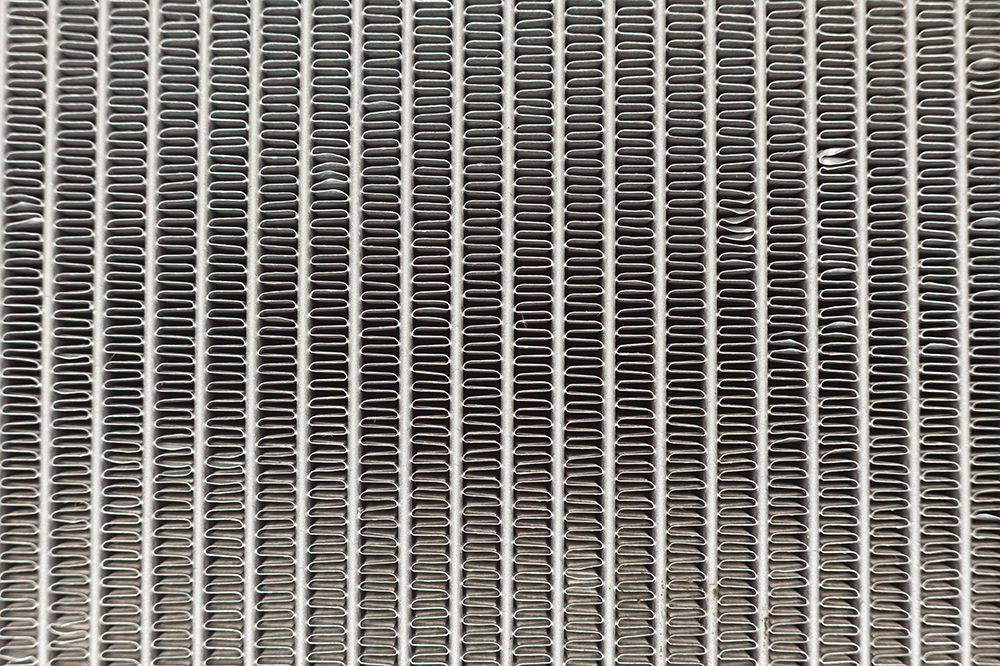
ORNL researchers are changing the state-of-the-art of polymer printing binders for ceramics in additive manufacturing, or 3D printing. Current technology requires a binder, usually a powder bed of ceramic material, that is built up into layers several times until achieving a 3D form. The 3D binder must be cured and de-binded, so that the binder material is then discarded. This invention is a method that allows 3D printing without sacrificing the binder, using preceramic polymers, producing high yield and saving several steps in the process. Their innovation is the use of preceramic polymers in the system and using crosslinkers and catalysts in the powder, which has never been accomplished.
Description
Silicon carbide (SiC) has excellent physical, thermal, and mechanical properties making it very attractive for many applications such as heat exchangers, high-temperature seals and valves, armor, mirrors and optics, and electronics. This can be used in additive manufacturing, which requires use of a binder to strengthen the printed parts. But the binder eventually becomes weak and burns out. By incorporating a pre-ceramic polymer such as SiC in the binder solution, the weak parts (known as brown parts) are made stronger, and post-processing can be accelerated. The preceramic polymer binder can convert to the same material as the printed material or convert to a compatible composite material. Usually at least five or more steps are needed for polymer infiltration, but this eliminates at least one step. Also, the part being printed will be stronger. None of the current technologies for AM methods for shaping complex ceramic forms can achieve this. Finally, utilizing this preceramic polymer as a non-sacrificial binder make it possible to tune the final properties for shrinkage, density, strength, and thermal activity.
Applications and Industries
- Insulators
- Heat exchangers
- Seals
- Industrial heating processes
- Composites with chopped fibers
- Any industry using additive manufacturing of parts
Benefits
- More efficient 3D printing
- Enhancements save time, money two-fold
- Reduces steps needed for 3D printing
- Maintains binder material