Invention Reference Number
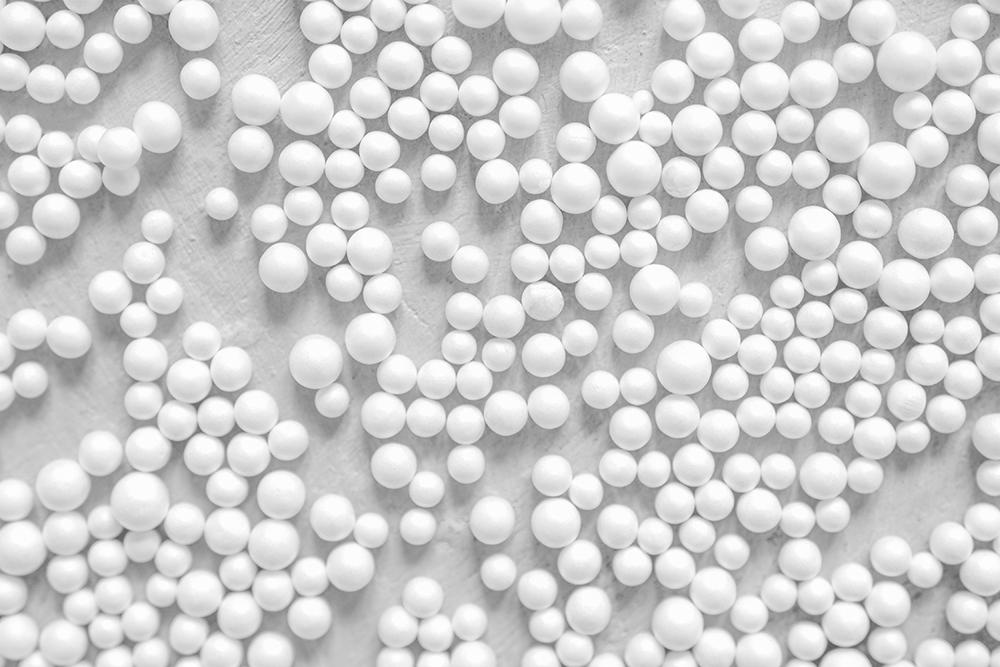
ORNL researchers have developed a new set of methods for producing thermal insulation foam in which the resulting materials’ thermal conductivity is not directly tied to material density. These new capabilities will enable production of a range of high-performance materials for applications in commercial and residential buildings, cold-storage transportation, and beyond. The new materials are made by incorporating variable amounts of two sources of porosity, porous hollow glass spheres (PHGS) and expandable thermoplastic microspheres (EMS), with synergistic effects. In addition to allowing for similar thermal conductivity across a range of densities, these two sources will reduce the use of environmentally harmful physical foaming agents in commercial insulation material.
Description
Increased focus on improved energy efficiency is driving the continued development of advanced thermal insulating materials. Modern thermal insulating materials are typically made from a thermoplastic or thermoset matrix with an embedded low conductivity filler such as silica. The use of a polymer-based matrix offers a range of benefits, including processability, mechanical stability, and easy incorporation of fillers for altered material properties. The use of these fillers has an important impact on the resultant material’s physical characteristics like thermal conductivity, physical stability and density, and flame retardancy.
Physical foaming agents are also usually added to increase porosity and thermal resistivity of commercial insulation material, but these foaming agents are traditionally made from chlorinated hydrocarbons that deplete ozone and accumulate in the environment, damaging bacterial and animal ecosystems through mutagenic and carcinogenic effects. ORNL’s new method describes the use of more environmentally friendly agents including PHGS and EMS. PHGS function as a lightweight filler with low thermal conductivity, while EMS add needed porosity to the structure without use of environmentally harmful foaming agents. The ratio of these components can be varied to control composites’ microstructure, thermal and physical qualities, and density. In addition to the compositional flexibility offered by this method, the fabrication protocol is similar to existing commercial practices. This similarity affords manufactures an easy transition to large-scale production of materials for a wide range of applications.
Benefits
- Improved living space utilization due to improved thermal insulation qualities
- Improved flexibility in material qualities
Applications and Industries
- Residential and commercial insulation
- Cold-storage transportation
- Refrigeration and heating devices
Contact
To learn more about this technology, email partnerships@ornl.gov or call 865-574-1051.