Invention Reference Number
Licensing Contact
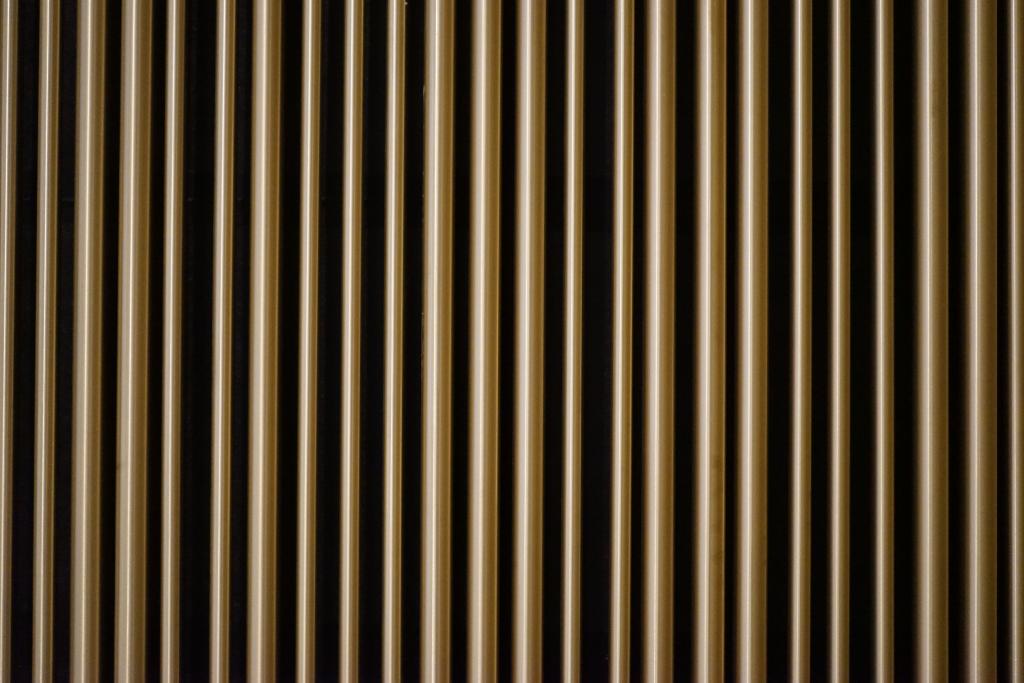
ORNL researchers have developed a novel surface treatment method for the metallic bipolar plates in hydrogen fuel cells and electrolyzers. The new method offers improved time and cost efficiency by providing an alternative to conventional coating techniques, which require high temperatures, strong vacuum conditions, and long deposition times. Surface treatment is a key step in metallic bipolar plate design, as it facilitates important structural and electrical transference functions. Efficient and easily producible hydrogen fuel cells will enable widespread adoption and provide an attractive alternative to internal combustion engines.
Description
Hydrogen fuel cells can efficiently produce CO2-free electrical power. Modern designs integrate several modular fuel cells into a stack for improved processibility and application flexibility. Bipolar plates separate individual cells in a stack, provide chemical and electrical conductance, and regulate heat and water transport. Because of these integral design functions, bipolar plates must be efficient, durable, and easily producible to make hydrogen energy technology viable.
Previous bipolar plate designs have used metals such as aluminum and titanium alloys as well as stainless steel, but these materials are vulnerable to corrosion and poor conductance over time. Addressing these challenges requires a coating over the metallic bipolar plate to ensure its long-term functionality. Several coating materials and methods have been proposed and utilized, but require high vacuum or temperature conditions, rare and expensive elements, and long deposition times.
To improve manufacturing cost and efficiency, ORNL has developed an open-air cold plasma nitridation coating process. Importantly, this process does not require vacuum conditions, making the method far more suitable for continuous manufacturing.
Applications and Industries
- Motor vehicles
- Power grid support
- Fossil fuel replacement
Benefits
- Improved processability
- Reduced cost compared with approaches using high-vacuum or precious materials