Invention Reference Number
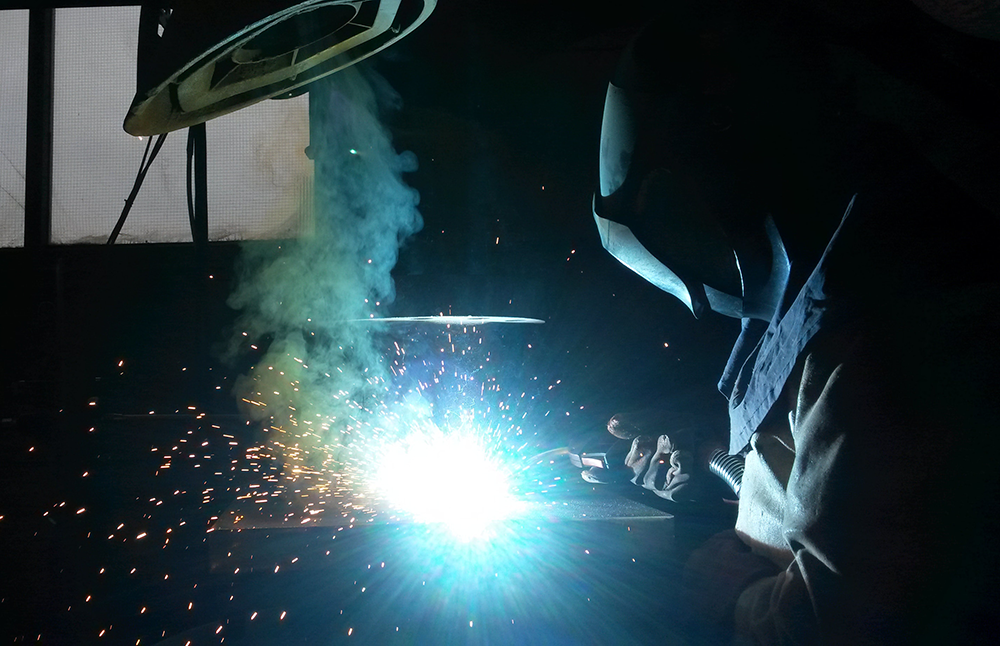
Welding high temperature and/or high strength materials for aerospace or automobile manufacturing is challenging. A conventional friction-based joining technique tool uses a specially designed pin that rotates under axial force and creates frictional heat that can consolidate a weld joint. However, the pin can deteriorate, impacting mechanical performance due to hook formation and limited weld size. This new technology welds materials without a pin, increasing the tool’s lifespan and performance, and avoiding cracking and deterioration in materials.
Description
This technology is a material joining process, called friction pressure welding, that uses a metal bonding tool that does not use a pin. Joining of high strength and/or high temperature for similar and/or dissimilar materials has been a critical challenge for automotive and aerospace applications. A current welding tool uses a pin, which create complex material flow and inhomogeneous microstructures, potentially lead to deteriorating mechanical joint performance. Also, large axial and latter stresses are focused on the pin when applying it to high strength materials, resulting in short tool life. Lower mechanical bonding strength can be a critical issue due to limited bonding area induced by the pin in conventional friction stir spot welding. The new tool applies pressure and rotates at the top of the material, and the heat generated by the interaction diffuses into the joint interface of the bottom material. This results in welding two metals into a solid without melting. This can be either a spot welding or continuous linear welding depending on the application. The materials being joined can be similar, such as magnesium alloys, aluminum, advanced and ultrahigh strength steels and composites, or dissimilar metals with different material combinations of different thicknesses. After joining, the tool retracts from the top material. Since there is no pin, there is no complex material flow during the joining step.
Applications and Industries
- Transportation industry
- Automotive industry
- Aerospace industry
Benefits
- Avoids cracking, deformations in welded metals
- Improves welded joint performance and tool life
- Useful for high strength and/or high temperature materials
- Can be used for spot welding or continuous linear welding
Contact
To learn more about this technology, email partnerships@ornl.gov or call 865-574-1051.