Invention Reference Number
Related Links
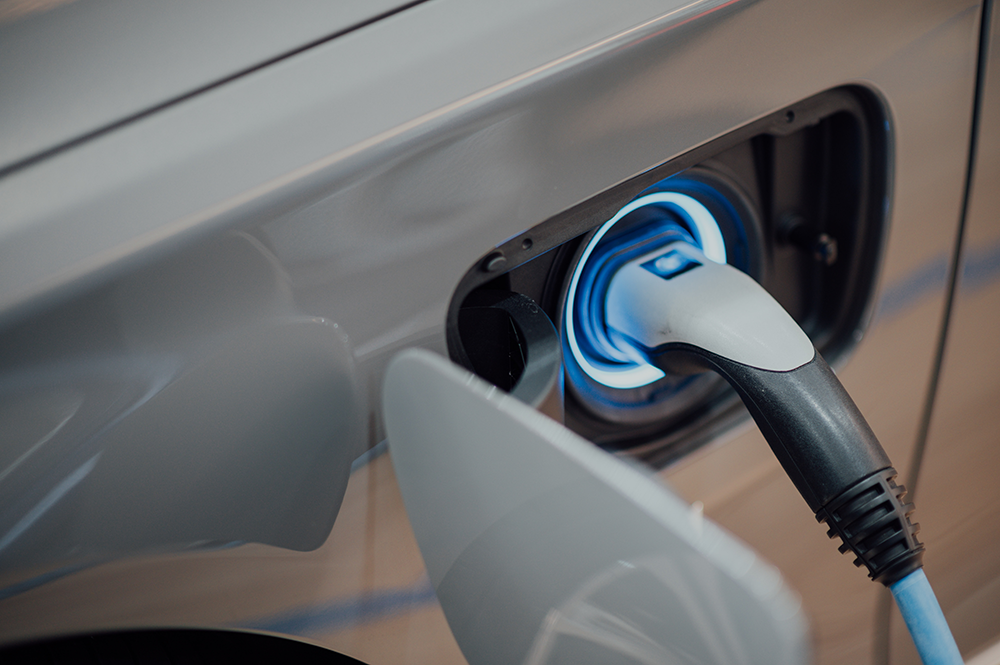
ORNL has developed a new hydrothermal synthesis route to generate high quality battery cathode precursors. The new route offers excellent compositional control, homogenous spherical morphologies, and an ammonia-free co-precipitation process. Precursors synthesized with this method also boast high tap densities, which will generate significant savings by increasing the amount of active material loaded into battery electrodes and reducing the necessary amount of electrode layers in battery cells.
Description
With the shift towards an increasingly technology-filled world, with smart devices in every hand and electric vehicles replacing gas-powered cars, sustainable and efficient battery technology is of utmost importance. Present-day batteries rely on cobalt-containing cathodes to reach high capacities but suffer from voltage drop and thermal instability. Furthermore, global cobalt reserves are depleting at a growing rate, threatening the future of traditional battery precursor manufacturing and increasing demand for new solutions.
Current battery precursors are generally made using Continuous Stirred Tank Reactor co-precipitation. This method uses ammonia as a chelating agent to control the particle size and morphology of precursor materials during co-precipitation, but suffers from low tap densities with some precursor materials. The use of ammonia in this process is also cost-intensive and requires large amounts of water for filtration and product washing. The process also contributes to toxic waste production, which damages animal habitats, harms biodiversity, and adversely affects human health.
The new hydrothermal co-precipitation method developed at ORNL addresses all these issues, boasting uniform spherical morphology and excellent compositional control. These advances lead to greatly improved tap density, while the elimination of ammonia from the co-precipitation process will significantly reduce water usage and toxic waste production.
Benefits
- More efficient and cost-effective production of battery cathode precursors
- Ammonia-free co-precipitation process greatly reduces water use and eliminates toxic waste generation
- New method promises improved thermal stability and reduced voltage drop
Applications and Industries
- Battery manufacturing companies
- Electric vehicle manufacturers
Contact
To learn more about this technology, email partnerships@ornl.gov or call 865-574-1051.