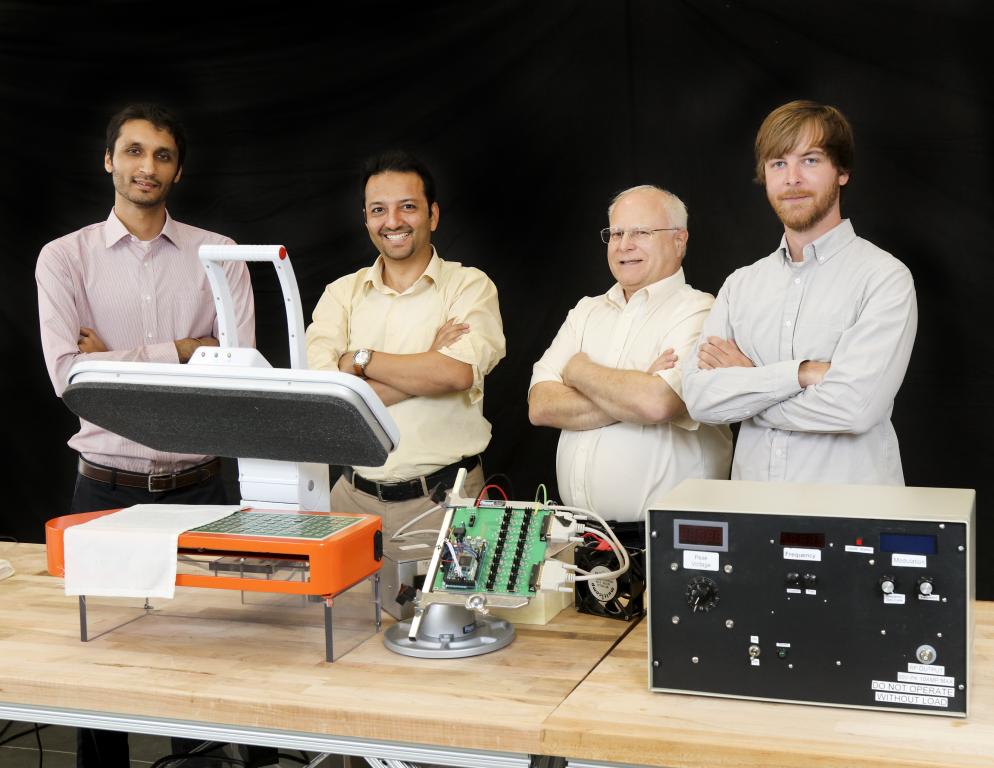
The development of the ultrasonic clothes dryer at Oak Ridge National Laboratory is a prime example of collaboration among various divisions at the lab—drawing upon the expertise necessary no matter where a scientist sits to transform a well-researched idea into a great invention.
When researchers in the Energy and Transportation Science Division (ETSD) decided to turn the experiments they had been conducting—on the use of ultrasonic transducers to nebulize water—into a demonstration of how the technology could be applied to drying clothes, their mechanical engineering background was key to achieving success.
The process involves piezoelectric transducers placed in direct contact with wet fabric, generating high frequency vibrations that atomize water, turning it into a mist. Taking thermal heat out of the drying process could result in significant energy savings compared with conventional clothes dryers that rely on heated air.
But scaling the project up from an experiment on a tiny square of fabric to a demonstration of a full-size press-style dryer required more sophisticated electronics and controls.
That’s when the Electrical and Electronics Systems Research (EESR) Division answered ESTD’s call for assistance. Both organizations are part of the Energy and Environmental Sciences Directorate.
After examining the setup by principal investigator Ayyoub Momen and researcher Viral Patel in ETSD’s Building Equipment Research Group, the electrical engineers and other researchers in EESR’s Sensors and Embedded Systems (SES) Group assisted with the electronics and some of the physics aspects of the transducers. They designed and built a series of amplifiers and electronic drivers as the researchers tested various frequencies, wave shapes, amplitudes, and voltage levels to help determine the best kind of piezoelectric transducers to use in the demonstration.
EESR also had students available who were able to work on the project—with guidance—on such tasks as drawing up schematics and producing needed equipment, noted Roger Kisner, who led the SES group effort. Participating were Christi Johnson, a staff member currently working on an MS in Electrical Engineering; Frederick Kyle Reed, pursuing a PhD in Electrical Engineering; and Evan Schlenker, who holds a BS in Electrical Engineering and who will begin pursuing a degree in the same area in the fall of 2016.
Later, SES called on Reed’s services to develop, simulate, mount, and test circuits.
Momen said that about 80% of the work on the prototype dryer was performed in Kisner’s lab space.
“From the first day, the SES group was very impactful on the project,” Momen said, adding that SES identified the correct commercial amplifier for the prototype and later designed and built three custom amplifiers that significantly boosted the efficiency of the demonstration.
“That’s what we do in this group: We get so involved that sometimes you can’t distinguish us,” Kisner said. “We want these projects to succeed. And so we’re not just a support technician who comes in; we become a researcher with the original team and drive the work forward.”
“We tend to have a very wide background in our group, with expertise in electronics, electrical systems, optics, whatever needs to be brought to bear,” Kisner said. “We tend to do a lot of rapid prototyping of things.
“Someone might come to us and say, ‘I’m building a new whatever-it-is, and no one’s ever done this before. Can you quickly put together something that would achieve the following things?’ And then we might respond, ‘Oh, I’ve never heard of it. Let’s do it.’ And then we step out and do what it takes to make it work,” said Kisner, who is a Distinguished R&D Staffer and Distinguished Inventor at ORNL.
Next up for the dryer project is studying the feasibility of moving to a drum-type application typical in residential dryers. One challenge to that scale-up is the requirement that the clothes and the transducers come in contact with each other. Momen said coupling can be accomplished through several means, from relying on the weight of the clothes to adding a bit more centrifugal force or backing reinforcement.
The energy savings potential is enormous because conventional clothes dryers using thermal heat currently consume about 1% of the energy used in the United States, Momen noted.
Using an ultrasonic process instead could cut drying time in half and use perhaps one-tenth of the power, with resulting savings in energy, cost, and time, Kisner said.
The invention can be scaled up to industrial applications, with the potential for collaboration with the pulp and paper industry for use in drying tons of pulp at a time or with carpet manufacturers in fiber drying, the researchers said.
ORNL is managed by UT-Battelle for DOE’s Office of Science, the single largest supporter of basic research in the physical sciences in the United States. DOE’s Office of Science is working to address some of the most pressing challenges of our time. For more information, please visit science.energy.gov. -- by Stephanie Seay