
Propulsion Materials Improve Powertrains
With new federal regulations in place for automobile fuel economy and greenhouse gas emissions and more stringent heavy-duty truck standards anticipated, the need for high performance powertrain materials is critical. Oak Ridge National Laboratory’s Propulsion Materials program is designed to identify and develop advanced materials and processes that improve powertrain system efficiency and reduce emissions.
ORNL researchers, in close collaboration with US industry, are focusing on materials for advanced engines, hybrid and electric drive systems, and vehicle exhaust systems. These materials promote a variety of performance benefits, including lightweighting, emissions reduction, thermal management, and corrosion mitigation. A key area of focus is materials that function reliably under the increased operating temperatures and pressures in turbo-charged engines and other high efficiency vehicle technologies.
The program utilizes ORNL’s unique suite of materials processing, characterization, and testing capabilities, including its neutron science, high resolution microscopy, mechanical properties, and engine testing facilities. Advanced computer modeling methods are being employed to design and improve critical materials for specific applications. The result is more rapid delivery of a wide range of advanced technologies that enable US manufacturing of clean, reliable, and fuel efficient vehicles. The Department of Energy's (DOE) Vehicle Technologies Office and industry are the primary sponsors of this research.
Materials for High-efficiency Engines
Researchers are working on solutions for friction and wear, advanced exhaust valve and turbo housing alloys, higher temperature cast aluminum, piezoelectric fuel injectors, materials and fuel compatibility, and coatings and surface treatments.
ORNL has developed new exhaust valve alloys with reduced nickel content for use in applications up to 870°C. The alloys function at higher temperatures and can be manufactured at lower cost than conventional materials.
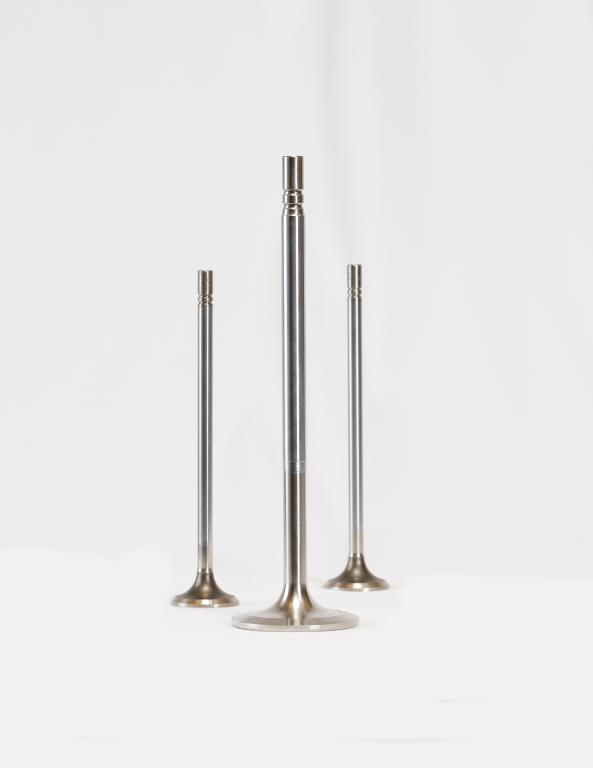
Materials for Energy Recovery and Exhaust Aftertreatment
Current projects in this area focus on diesel particulate filters, exhaust gas recirculation, catalyst materials, thermoelectric materials, higher temperature exhaust manifolds, and advanced turbochargers.
ORNL is working with nine American diesel engine manufacturers to address an industry-wide problem in a key emissions control component. Researchers are using neutron tomography, microscopy, and other nondestructive methods to gain a better understanding of fouling and corrosion in diesel engine heat exchangers.
Materials for Electric and Hybrid Drive Systems
High-temperature power electronics materials, non-rare earth magnetic materials, improved organic dielectrics, and materials for electric drive motors are just a few of the ways ORNL is developing better materials for electric vehicles.
Researchers discovered a new iron and aluminum based ferromagnetic material for use in electric motors and other vehicle applications. This new material could reduce US dependence on rare earth magnetic materials, which are primarily available through foreign imports.
Materials by Design
Researchers use sophisticated tools like integrated computational materials engineering (ICME) in the development and characterization of advanced cast and wrought alloys, novel catalysts, and thermoelectric and piezoelectric materials.
ORNL’s materials property modeling accurately predicted outstanding properties for a specific composition of high performance thermoelectric material, which had been previously overlooked. The material can be used to increase efficiency by converting waste heat to electricity.