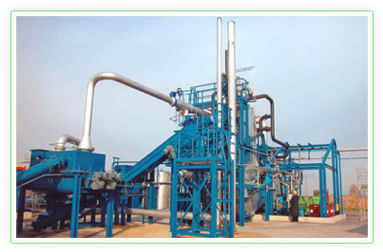
Controlled Pyrolysis: Creating a Robust Scalable Composite Recycling Technology
Evaluate and validate the conditions of controlled pyrolysis to enable a successful business case by optimizing feedstock and operational parameters for controlled pyrolysis. This technology utilizes the inherent energy in composites for fuel and preserves the structural value of glass fiber and carbon fiber for reuse. It can also be used for recycling other waste streams at the same facility, thus spreading capital risk and recovery across multiple industries and achieving economy of scale.
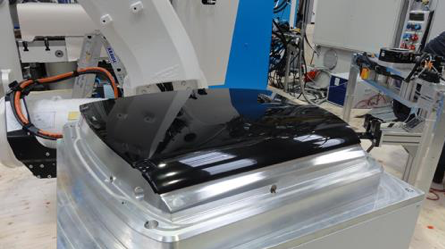
Development of rCF Thermoplastic Non-woven Prepreg for Automotive Class A Body Panels with Compression Molding
Focused on the development of processing and material technologies that provide automotive Class A surface appearance and suitable mechanical properties for automotive body panels utilizing a thermoplastic matrix reinforced with discontinuous recycled carbon fibers (rCF). Additionally, research will investigate and develop fast cycle processes such as induction heating and also develop a capability to manufacture polyamide materials for on-line class A painting.
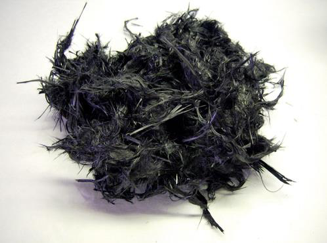
Automotive Carbon Fiber Prepeg Manufacturing Scrap
Address the challenges of creating consistent recycled carbon fiber reinforced thermoplastics for use in vehicle lightweighting applications. Through the use of innovative and novel enabling technologies research will characterize and validate materials to meet the growing demand for cost effective carbon fiber needed for vehicle weight reductions to improve fuel economy, reduce emissions, and extend electric vehicle range.
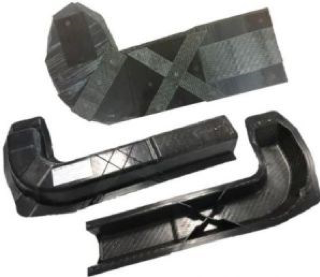
Automated Preform Manufacturing Equipment
The most significant near-term issue facing manufacturers in the recycling of high-volume carbon fiber pre-preg is the re-formatting of the trim (manufacturing offal) into a usable near-net shaped charge (or preform) at high efficiency. ORNL is collaborating to develop a combination chop, collate, and placement machine system that can address the unique challenges of re-purposing carbon-epoxy pre-preg.
Multiple Stream Low Cost Recycling Method
The composite industry faces a significant challenge of recycling of production waste and End-of-Life parts. Because of the costs of collection, resizing and method of recovery, there does not appear to be an economic solution (aside from using the composite for energy production by pyrolysis) for fiberglass based and foam/balsa cored structures such as those used in Wabash trailers, marine craft and wind turbine blades. ORNL is working in collaboration to develop a method that allows for any type of composite waste in any type of form to be reprocessed to make a high-performance composite.

Development of Additively Manufactured Tool and Preforms Made with Reclaimed Carbon Fibers
Using big area additive manufacturing to demonstrate how tooling manufacturing can be used to make preforms and parts. This process utilizes reclaimed carbon fiber in the tooling and preforms to produce a lightweight automotive part. Combining reclaimed carbon fiber with 3D printing processes will greatly reduce the manufacturing time and cost demonstrating the viability of composite parts in vehicle light weighting.
Carbon Fiber Reinforced Polyolefin Body Panels
Carbon fiber reinforced plastics offer excellent specific stiffness and when derived from reclaimed/recycled carbon fiber (rCF) compounded with inexpensive polyolefins (PO) for injection molding have the potential to meet both performance and affordability targets for lightweight paintable vertical body panels. ORNL is collaborating to develop lightweight body panels for automobiles, made from polyolefin.