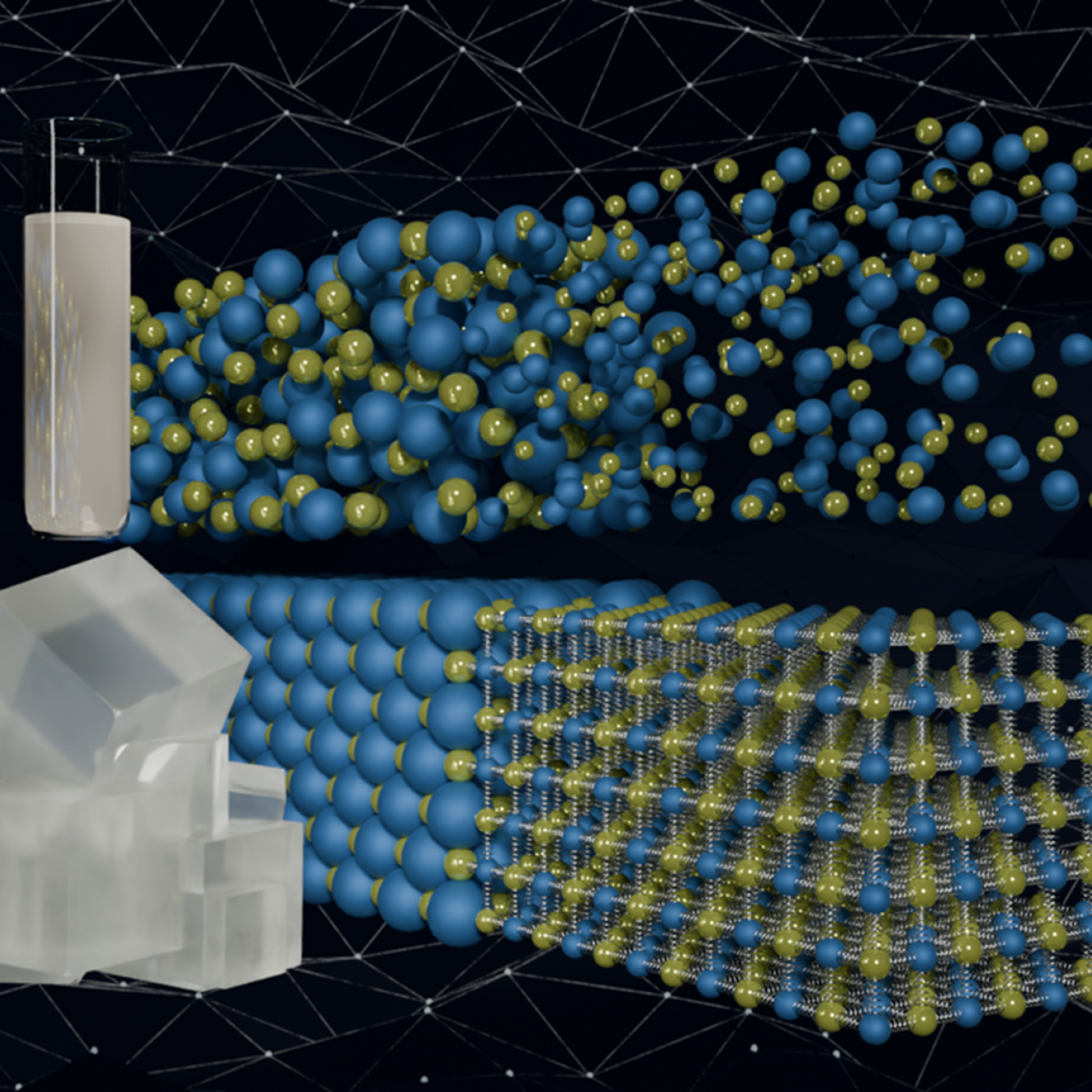
Filter News
Area of Research
- Advanced Manufacturing (18)
- Biology and Environment (14)
- Building Technologies (1)
- Computer Science (2)
- Energy Science (119)
- Energy Sciences (1)
- Fuel Cycle Science and Technology (1)
- Fusion and Fission (13)
- Fusion Energy (8)
- Isotope Development and Production (2)
- Isotopes (5)
- Materials (49)
- Materials for Computing (8)
- National Security (7)
- Neutron Science (13)
- Nuclear Science and Technology (19)
- Nuclear Systems Modeling, Simulation and Validation (2)
- Supercomputing (14)
- Transportation Systems (2)
News Type
News Topics
- (-) 3-D Printing/Advanced Manufacturing (82)
- (-) Advanced Reactors (25)
- (-) Energy Storage (75)
- (-) Irradiation (2)
- (-) Molten Salt (8)
- (-) Nuclear Energy (47)
- (-) Space Exploration (13)
- (-) Transportation (62)
- Artificial Intelligence (51)
- Big Data (25)
- Bioenergy (42)
- Biology (47)
- Biomedical (28)
- Biotechnology (14)
- Buildings (36)
- Chemical Sciences (48)
- Clean Water (16)
- Composites (23)
- Computer Science (105)
- Coronavirus (28)
- Critical Materials (23)
- Cybersecurity (20)
- Education (3)
- Element Discovery (1)
- Emergency (1)
- Environment (86)
- Exascale Computing (14)
- Fossil Energy (2)
- Frontier (17)
- Fusion (26)
- Grid (38)
- High-Performance Computing (44)
- Hydropower (6)
- Isotopes (25)
- ITER (5)
- Machine Learning (27)
- Materials (96)
- Materials Science (90)
- Mathematics (3)
- Mercury (5)
- Microelectronics (1)
- Microscopy (28)
- Nanotechnology (41)
- National Security (21)
- Neutron Science (81)
- Partnerships (33)
- Physics (30)
- Polymers (23)
- Quantum Computing (18)
- Quantum Science (43)
- Security (13)
- Simulation (19)
- Statistics (2)
- Summit (30)
Media Contacts
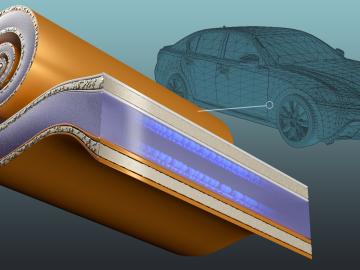
Strengthening the competitiveness of the U.S. transportation industry depends on developing domestic EV batteries that combine rapid charging with long-range performance — two goals that often conflict. Researchers at ORNL have addressed this challenge by redesigning a key battery component, enabling fast, 10-minute charging while improving energy density and reducing reliance on copper.

Recent advancements at ORNL show that 3D-printed metal molds offer a faster, more cost-effective and flexible approach to producing large composite components for mass-produced vehicles than traditional tooling methods.

Analyzing massive datasets from nuclear physics experiments can take hours or days to process, but researchers are working to radically reduce that time to mere seconds using special software being developed at the Department of Energy’s Lawrence Berkeley and Oak Ridge national laboratories.

Scientists at ORNL have developed a vacuum-assisted extrusion method that reduces internal porosity by up to 75% in large-scale 3D-printed polymer parts. This new technique addresses the critical issue of porosity in large-scale prints but also paves the way for stronger composites.
Scientists at ORNL have developed a method that can track chemical changes in molten salt in real time — helping to pave the way for the deployment of molten salt reactors for energy production.

Researchers with the Department of Energy’s Oak Ridge National Laboratory and Sierra Space Corporation have developed a new silicon-carbide-based thermal protection system, or TPS, for reusable commercial spacecraft.

Scientists at ORNL are studying the failure mechanisms of a new solid electrolyte battery to enhance long-term storage for renewable energy, aiming to make wind and solar power more reliable for the electric grid.

Oak Ridge National Laboratory researchers are using a new bioderived material to 3D print custom roosting structures for endangered bats.

Researchers have developed and 3D printed the lightest crack-free alloy capable of operating without melting at temperatures above 2,400 degrees Fahrenheit, which could enable additively manufactured turbine blades to better handle extreme temperatures, reducing the carbon footprint of gas turbine engines such as those used in airplanes.

Researchers at ORNL are using advanced manufacturing techniques to revitalize the domestic production of very large metal parts that weigh at least 10,000 pounds each and are necessary for a variety of industries, including energy.