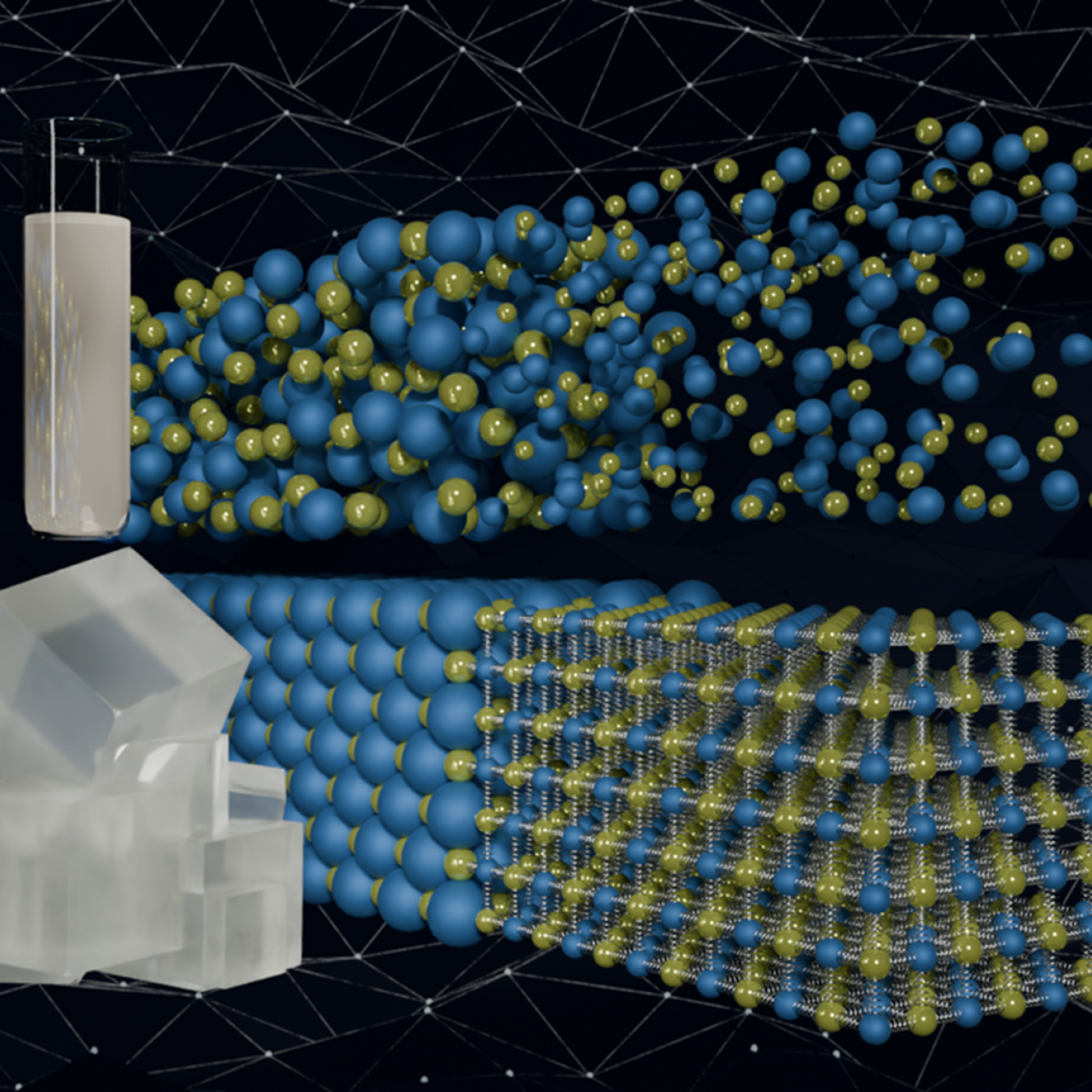
Filter News
Area of Research
- Advanced Manufacturing (7)
- Biology and Environment (11)
- Computer Science (1)
- Energy Science (36)
- Fusion and Fission (4)
- Isotope Development and Production (1)
- Isotopes (1)
- Materials (46)
- Materials Characterization (1)
- Materials for Computing (6)
- Materials Under Extremes (1)
- National Security (2)
- Neutron Science (16)
- Nuclear Science and Technology (3)
- Supercomputing (10)
News Type
News Topics
- (-) 3-D Printing/Advanced Manufacturing (48)
- (-) Big Data (8)
- (-) Materials Science (56)
- Advanced Reactors (12)
- Artificial Intelligence (35)
- Bioenergy (25)
- Biology (26)
- Biomedical (17)
- Biotechnology (10)
- Buildings (15)
- Chemical Sciences (35)
- Clean Water (2)
- Composites (12)
- Computer Science (63)
- Coronavirus (17)
- Critical Materials (11)
- Cybersecurity (17)
- Education (3)
- Element Discovery (1)
- Energy Storage (43)
- Environment (38)
- Exascale Computing (13)
- Fossil Energy (1)
- Frontier (16)
- Fusion (17)
- Grid (16)
- High-Performance Computing (32)
- Isotopes (20)
- ITER (2)
- Machine Learning (13)
- Materials (60)
- Mercury (2)
- Microelectronics (1)
- Microscopy (17)
- Molten Salt (3)
- Nanotechnology (29)
- National Security (18)
- Neutron Science (54)
- Nuclear Energy (28)
- Partnerships (31)
- Physics (26)
- Polymers (13)
- Quantum Computing (13)
- Quantum Science (31)
- Security (12)
- Simulation (10)
- Space Exploration (3)
- Statistics (1)
- Summit (22)
- Transportation (26)
Media Contacts
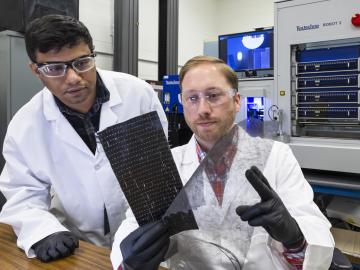
Researchers at ORNL have developed an innovative new technique using carbon nanofibers to enhance binding in carbon fiber and other fiber-reinforced polymer composites – an advance likely to improve structural materials for automobiles, airplanes and other applications that require lightweight and strong materials.

Recent advancements at ORNL show that 3D-printed metal molds offer a faster, more cost-effective and flexible approach to producing large composite components for mass-produced vehicles than traditional tooling methods.

Analyzing massive datasets from nuclear physics experiments can take hours or days to process, but researchers are working to radically reduce that time to mere seconds using special software being developed at the Department of Energy’s Lawrence Berkeley and Oak Ridge national laboratories.

Working at nanoscale dimensions, billionths of a meter in size, a team of scientists led by ORNL revealed a new way to measure high-speed fluctuations in magnetic materials. Knowledge obtained by these new measurements could be used to advance technologies ranging from traditional computing to the emerging field of quantum computing.

P&G is using simulations on the ORNL Summit supercomputer to study how surfactants in cleaners cause eye irritation. By modeling the corneal epithelium, P&G aims to develop safer, concentrated cleaning products that meet performance and safety standards while supporting sustainability goals.

Researchers with the Department of Energy’s Oak Ridge National Laboratory and Sierra Space Corporation have developed a new silicon-carbide-based thermal protection system, or TPS, for reusable commercial spacecraft.

Researchers at ORNL are using advanced manufacturing techniques to revitalize the domestic production of very large metal parts that weigh at least 10,000 pounds each and are necessary for a variety of industries, including energy.

A study led by the Department of Energy’s Oak Ridge National Laboratory details how artificial intelligence researchers created an AI model to help identify new alloys used as shielding for housing fusion applications components in a nuclear reactor. The findings mark a major step towards improving nuclear fusion facilities.

A team led by scientists at ORNL identified and demonstrated a method to process a plant-based material called nanocellulose that reduced energy needs by a whopping 21%, using simulations on the lab’s supercomputers and follow-on analysis.
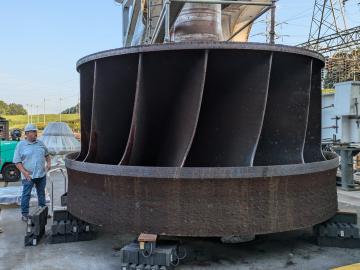
ORNL is working with industry partners to develop a technique that combines 3D printing and conventional machining to produce large metal parts for energy applications. The project, known as Rapid Research on Universal Near Net Shape Fabrication Strategies for Expedited Runner Systems, or Rapid RUNNERS, recently received $15 million in funding from DOE.