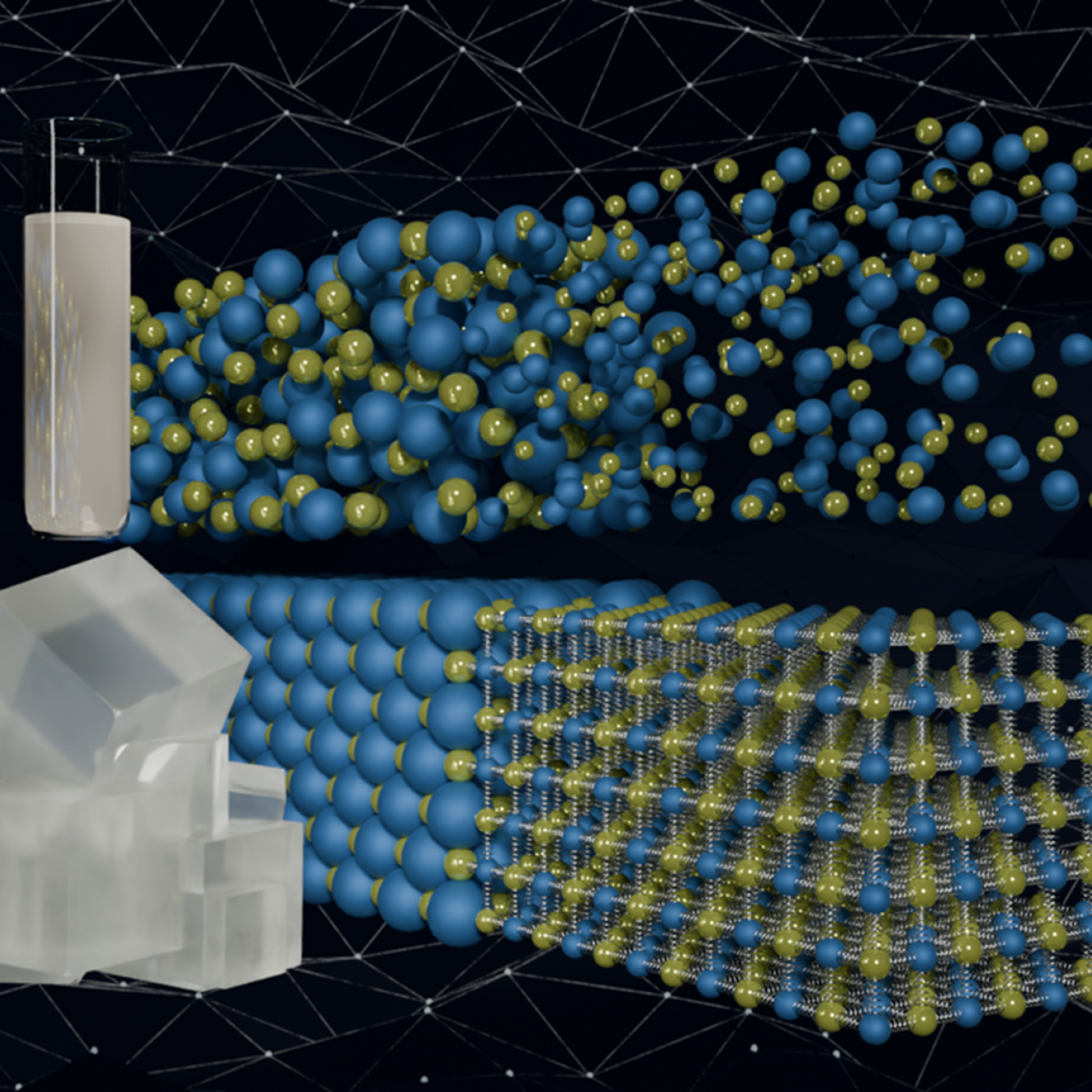
Filter News
Area of Research
- Advanced Manufacturing (7)
- Biology and Environment (11)
- Computational Engineering (1)
- Energy Science (32)
- Fuel Cycle Science and Technology (1)
- Fusion and Fission (9)
- Fusion Energy (1)
- Isotope Development and Production (1)
- Isotopes (2)
- Materials (16)
- Materials for Computing (2)
- National Security (4)
- Neutron Science (8)
- Nuclear Science and Technology (8)
- Supercomputing (8)
News Type
News Topics
- (-) 3-D Printing/Advanced Manufacturing (48)
- (-) Biomedical (17)
- (-) Nuclear Energy (28)
- Advanced Reactors (12)
- Artificial Intelligence (35)
- Big Data (8)
- Bioenergy (25)
- Biology (26)
- Biotechnology (10)
- Buildings (15)
- Chemical Sciences (35)
- Clean Water (2)
- Composites (12)
- Computer Science (63)
- Coronavirus (17)
- Critical Materials (11)
- Cybersecurity (17)
- Education (3)
- Element Discovery (1)
- Energy Storage (43)
- Environment (38)
- Exascale Computing (13)
- Fossil Energy (1)
- Frontier (16)
- Fusion (17)
- Grid (16)
- High-Performance Computing (32)
- Isotopes (20)
- ITER (2)
- Machine Learning (13)
- Materials (60)
- Materials Science (56)
- Mercury (2)
- Microelectronics (1)
- Microscopy (17)
- Molten Salt (3)
- Nanotechnology (29)
- National Security (18)
- Neutron Science (54)
- Partnerships (31)
- Physics (26)
- Polymers (13)
- Quantum Computing (13)
- Quantum Science (31)
- Security (12)
- Simulation (10)
- Space Exploration (3)
- Statistics (1)
- Summit (22)
- Transportation (26)
Media Contacts

Recent advancements at ORNL show that 3D-printed metal molds offer a faster, more cost-effective and flexible approach to producing large composite components for mass-produced vehicles than traditional tooling methods.

Analyzing massive datasets from nuclear physics experiments can take hours or days to process, but researchers are working to radically reduce that time to mere seconds using special software being developed at the Department of Energy’s Lawrence Berkeley and Oak Ridge national laboratories.

Researchers with the Department of Energy’s Oak Ridge National Laboratory and Sierra Space Corporation have developed a new silicon-carbide-based thermal protection system, or TPS, for reusable commercial spacecraft.

Researchers at ORNL are using advanced manufacturing techniques to revitalize the domestic production of very large metal parts that weigh at least 10,000 pounds each and are necessary for a variety of industries, including energy.

A team led by scientists at ORNL identified and demonstrated a method to process a plant-based material called nanocellulose that reduced energy needs by a whopping 21%, using simulations on the lab’s supercomputers and follow-on analysis.
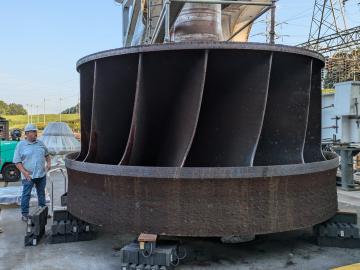
ORNL is working with industry partners to develop a technique that combines 3D printing and conventional machining to produce large metal parts for energy applications. The project, known as Rapid Research on Universal Near Net Shape Fabrication Strategies for Expedited Runner Systems, or Rapid RUNNERS, recently received $15 million in funding from DOE.

Researchers for the first time documented the specific chemistry dynamics and structure of high-temperature liquid uranium trichloride salt, a potential nuclear fuel source for next-generation reactors.

ORNL researchers completed successful testing of a gallium nitride transistor for use in more accurate sensors operating near the core of a nuclear reactor. This is an important technical advance particularly for monitoring new, compact.
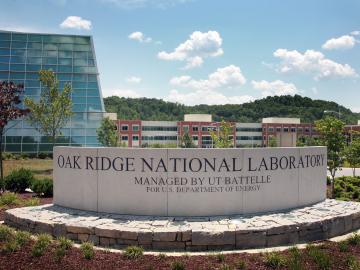
Two different teams that included Oak Ridge National Laboratory employees were honored Feb. 20 with Secretary’s Honor Achievement Awards from the Department of Energy. This is DOE's highest form of employee recognition.

Corning uses neutron scattering to study the stability of different types of glass. Recently, researchers for the company have found that understanding the stability of the rings of atoms in glass materials can help predict the performance of glass products.