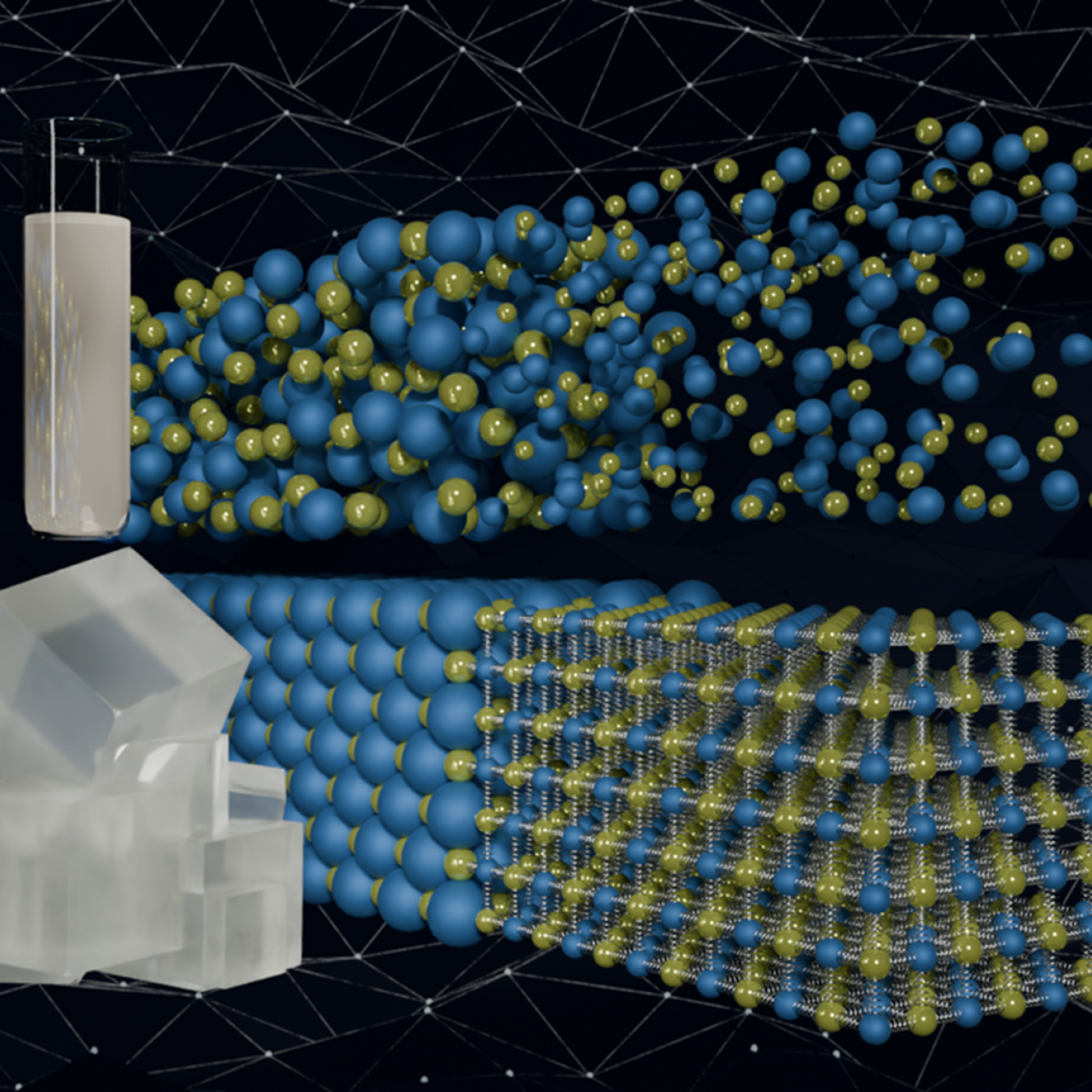
Filter News
Area of Research
- Advanced Manufacturing (23)
- Biological Systems (2)
- Biology and Environment (76)
- Building Technologies (1)
- Computational Biology (1)
- Computational Engineering (1)
- Computer Science (3)
- Electricity and Smart Grid (1)
- Energy Science (143)
- Fuel Cycle Science and Technology (1)
- Functional Materials for Energy (2)
- Fusion and Fission (32)
- Fusion Energy (12)
- Isotope Development and Production (1)
- Isotopes (8)
- Materials (154)
- Materials Characterization (2)
- Materials for Computing (23)
- Materials Under Extremes (1)
- National Security (32)
- Neutron Science (49)
- Nuclear Science and Technology (37)
- Nuclear Systems Modeling, Simulation and Validation (1)
- Quantum information Science (3)
- Supercomputing (86)
- Transportation Systems (1)
News Topics
- (-) 3-D Printing/Advanced Manufacturing (146)
- (-) Bioenergy (112)
- (-) Cybersecurity (35)
- (-) Materials (157)
- (-) Materials Science (158)
- (-) Mercury (12)
- (-) Nuclear Energy (122)
- (-) Summit (71)
- Advanced Reactors (40)
- Artificial Intelligence (131)
- Big Data (79)
- Biology (128)
- Biomedical (73)
- Biotechnology (39)
- Buildings (74)
- Chemical Sciences (86)
- Clean Water (33)
- Composites (35)
- Computer Science (226)
- Coronavirus (48)
- Critical Materials (29)
- Education (5)
- Element Discovery (1)
- Emergency (4)
- Energy Storage (114)
- Environment (218)
- Exascale Computing (67)
- Fossil Energy (8)
- Frontier (64)
- Fusion (66)
- Grid (74)
- High-Performance Computing (130)
- Hydropower (12)
- Irradiation (3)
- Isotopes (62)
- ITER (9)
- Machine Learning (68)
- Mathematics (12)
- Microelectronics (4)
- Microscopy (56)
- Molten Salt (10)
- Nanotechnology (64)
- National Security (86)
- Neutron Science (171)
- Partnerships (68)
- Physics (69)
- Polymers (35)
- Quantum Computing (53)
- Quantum Science (92)
- Security (31)
- Simulation (65)
- Software (1)
- Space Exploration (26)
- Statistics (4)
- Transportation (103)
Media Contacts
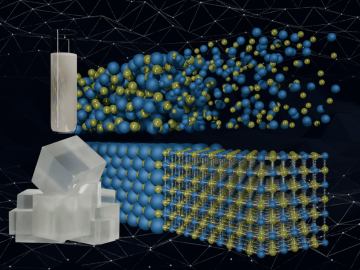
Scientists have developed a new machine learning approach that accurately predicted critical and difficult-to-compute properties of molten salts, materials with diverse nuclear energy applications.
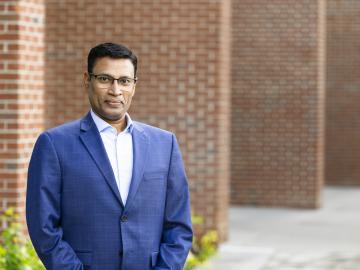
From decoding plant genomes to modeling microbial behavior, computational biologist Priya Ranjan builds computational tools that turn extensive biological datasets into real-world insights. These tools transform the way scientists ask and answer complex biological questions that advance biotechnology breakthroughs and support cultivation of better crops for energy and food security.
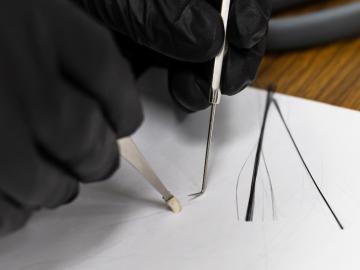
Stronger than steel and lighter than aluminum, carbon fiber is a staple in aerospace and high-performance vehicles — and now, scientists at ORNL have found a way to make it even stronger.
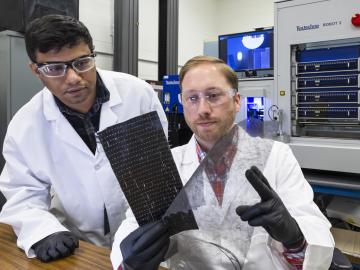
Researchers at ORNL have developed an innovative new technique using carbon nanofibers to enhance binding in carbon fiber and other fiber-reinforced polymer composites – an advance likely to improve structural materials for automobiles, airplanes and other applications that require lightweight and strong materials.
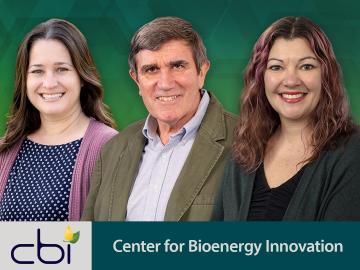
The Center for Bioenergy Innovation, or CBI, at the Department of Energy’s Oak Ridge National Laboratory has promoted Melissa Cregger and Carrie Eckert to serve as chief science officers, advancing the center’s mission of innovations for new domestic biofuels, chemicals and materials.

As the focus on energy resiliency and competitiveness increases, the development of advanced materials for next-generation, commercial fusion reactors is gaining attention. A recent paper examines a promising candidate for these reactors: ultra-high-temperature ceramics, or UHTCs.

Recent advancements at ORNL show that 3D-printed metal molds offer a faster, more cost-effective and flexible approach to producing large composite components for mass-produced vehicles than traditional tooling methods.

UT-Battelle has contributed up to $475,000 for the purchase and installation of advanced manufacturing equipment to support a program at Tennessee’s Oak Ridge High School that gives students direct experience with the AI- and robotics-assisted workplace of the future.

Analyzing massive datasets from nuclear physics experiments can take hours or days to process, but researchers are working to radically reduce that time to mere seconds using special software being developed at the Department of Energy’s Lawrence Berkeley and Oak Ridge national laboratories.

Scientists at ORNL have developed a vacuum-assisted extrusion method that reduces internal porosity by up to 75% in large-scale 3D-printed polymer parts. This new technique addresses the critical issue of porosity in large-scale prints but also paves the way for stronger composites.