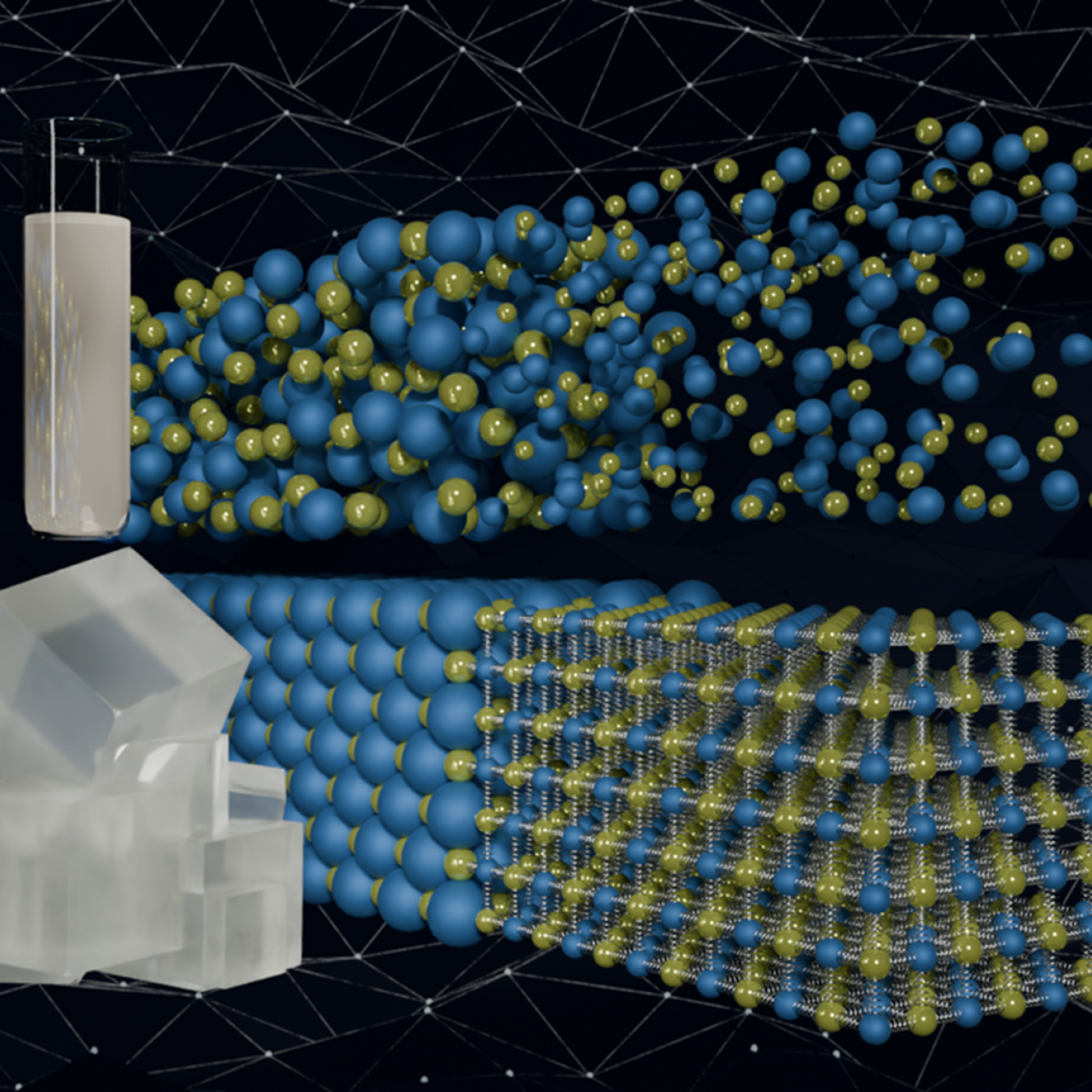
Filter News
Area of Research
News Topics
- (-) 3-D Printing/Advanced Manufacturing (146)
- (-) Composites (35)
- (-) Critical Materials (29)
- (-) Fusion (66)
- Advanced Reactors (40)
- Artificial Intelligence (131)
- Big Data (79)
- Bioenergy (112)
- Biology (128)
- Biomedical (73)
- Biotechnology (39)
- Buildings (74)
- Chemical Sciences (86)
- Clean Water (33)
- Computer Science (226)
- Coronavirus (48)
- Cybersecurity (35)
- Education (5)
- Element Discovery (1)
- Emergency (4)
- Energy Storage (114)
- Environment (218)
- Exascale Computing (67)
- Fossil Energy (8)
- Frontier (64)
- Grid (74)
- High-Performance Computing (130)
- Hydropower (12)
- Irradiation (3)
- Isotopes (62)
- ITER (9)
- Machine Learning (68)
- Materials (157)
- Materials Science (158)
- Mathematics (12)
- Mercury (12)
- Microelectronics (4)
- Microscopy (56)
- Molten Salt (10)
- Nanotechnology (64)
- National Security (86)
- Neutron Science (171)
- Nuclear Energy (122)
- Partnerships (68)
- Physics (69)
- Polymers (35)
- Quantum Computing (53)
- Quantum Science (93)
- Security (31)
- Simulation (65)
- Software (1)
- Space Exploration (26)
- Statistics (4)
- Summit (71)
- Transportation (103)
Media Contacts

John joined the MPEX project in 2019 and has served as project manager for several organizations within ORNL.

The award was given in “recognition of his lifelong leadership in fusion technology for plasma fueling systems in magnetically confined fusion systems.”

At ORNL, a group of scientists used neutron scattering techniques to investigate a relatively new functional material called a Weyl semimetal. These Weyl fermions move very quickly in a material and can carry electrical charge at room temperature. Scientists think that Weyl semimetals, if used in future electronics, could allow electricity to flow more efficiently and enable more energy-efficient computers and other electronic devices.

Seven entrepreneurs comprise the next cohort of Innovation Crossroads, a DOE Lab-Embedded Entrepreneurship Program node based at ORNL. The program provides energy-related startup founders from across the nation with access to ORNL’s unique scientific resources and capabilities, as well as connect them with experts, mentors and networks to accelerate their efforts to take their world-changing ideas to the marketplace.

The world’s fastest supercomputer helped researchers simulate synthesizing a material harder and tougher than a diamond — or any other substance on Earth. The study used Frontier to predict the likeliest strategy to synthesize such a material, thought to exist so far only within the interiors of giant exoplanets, or planets beyond our solar system.
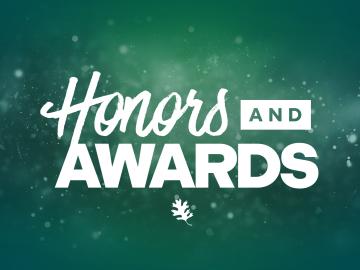
Two additive manufacturing researchers from ORNL received prestigious awards from national organizations. Amy Elliott and Nadim Hmeidat, who both work in the Manufacturing Science Division, were recognized recently for their early career accomplishments.

Two ORNL teams recently completed Cohort 18 of Energy I-Corps, an immersive two-month training program where the scientists define their technology’s value propositions, conduct stakeholder discovery interviews and develop viable market pathways.

Brian Sanders is focused on impactful, multidisciplinary science at Oak Ridge National Laboratory, developing solutions for everything from improved imaging of plant-microbe interactions that influence ecosystem health to advancing new treatments for cancer and viral infections.

Brittany Rodriguez never imagined she would pursue a science career at a Department of Energy national laboratory. However, after some encouraging words from her mother, input from key mentors at the University of Texas Rio Grande Valley, or UTRGV, and a lot of hard work, Rodriguez landed at DOE’s Manufacturing Demonstration Facility, or MDF, at Oak Ridge National Laboratory.
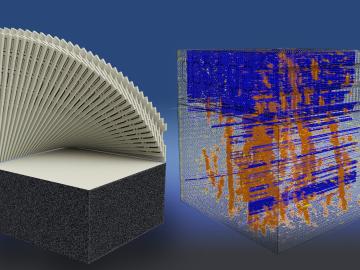
The Department of Energy’s Oak Ridge National Laboratory has publicly released a new set of additive manufacturing data that industry and researchers can use to evaluate and improve the quality of 3D-printed components. The breadth of the datasets can significantly boost efforts to verify the quality of additively manufactured parts using only information gathered during printing, without requiring expensive and time-consuming post-production analysis.