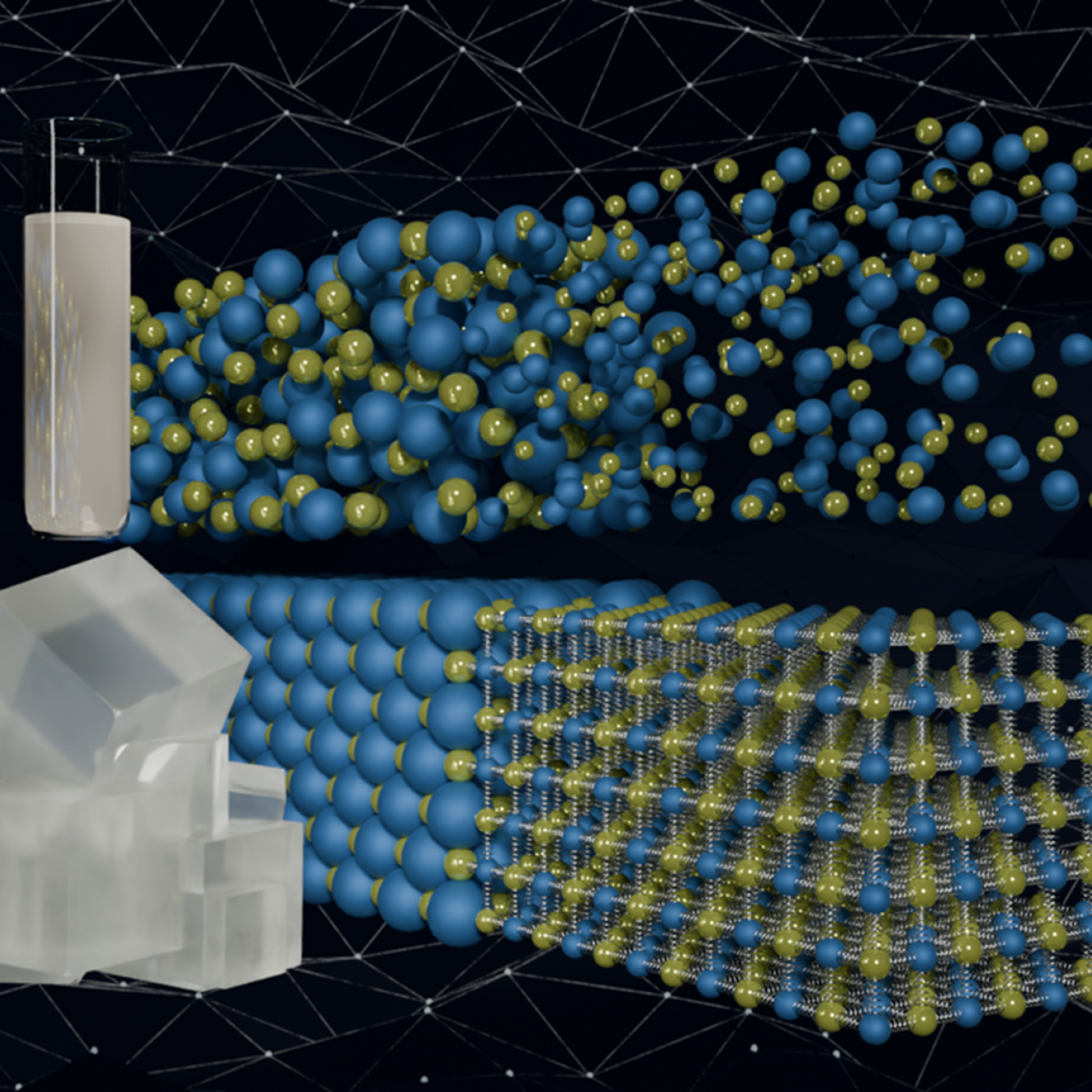
Filter News
Area of Research
- Advanced Manufacturing (22)
- Biology and Environment (20)
- Biology and Soft Matter (1)
- Building Technologies (1)
- Energy Science (90)
- Fusion and Fission (7)
- Fusion Energy (1)
- Materials (51)
- Materials for Computing (8)
- National Security (4)
- Neutron Science (9)
- Nuclear Science and Technology (4)
- Supercomputing (10)
News Topics
- (-) 3-D Printing/Advanced Manufacturing (147)
- (-) Chemical Sciences (86)
- Advanced Reactors (40)
- Artificial Intelligence (131)
- Big Data (79)
- Bioenergy (112)
- Biology (128)
- Biomedical (73)
- Biotechnology (39)
- Buildings (74)
- Clean Water (33)
- Composites (35)
- Computer Science (226)
- Coronavirus (48)
- Critical Materials (29)
- Cybersecurity (35)
- Education (5)
- Element Discovery (1)
- Emergency (4)
- Energy Storage (114)
- Environment (218)
- Exascale Computing (67)
- Fossil Energy (8)
- Frontier (64)
- Fusion (67)
- Grid (74)
- High-Performance Computing (130)
- Hydropower (12)
- Irradiation (3)
- Isotopes (62)
- ITER (9)
- Machine Learning (68)
- Materials (157)
- Materials Science (158)
- Mathematics (12)
- Mercury (12)
- Microelectronics (4)
- Microscopy (56)
- Molten Salt (10)
- Nanotechnology (64)
- National Security (86)
- Neutron Science (171)
- Nuclear Energy (122)
- Partnerships (68)
- Physics (69)
- Polymers (35)
- Quantum Computing (53)
- Quantum Science (93)
- Security (31)
- Simulation (65)
- Software (1)
- Space Exploration (26)
- Statistics (4)
- Summit (71)
- Transportation (103)
Media Contacts
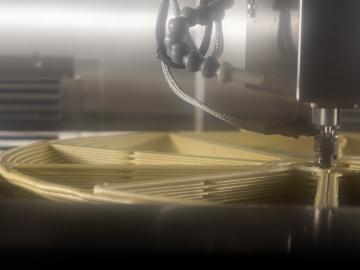
ORNL and JuggerBot 3D, an industrial 3D printer equipment manufacturer, have launched their second research and development collaboration through the Manufacturing Demonstration Facility Technical Collaboration Program.
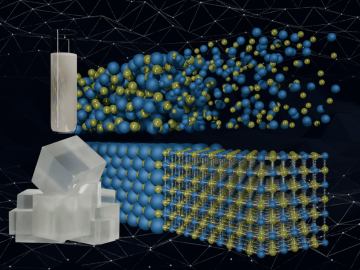
Scientists have developed a new machine learning approach that accurately predicted critical and difficult-to-compute properties of molten salts, materials with diverse nuclear energy applications.
Using the now-decommissioned Summit supercomputer, researchers at ORNL ran the largest and most accurate molecular dynamics simulations yet of the interface between water and air during a chemical reaction. The simulations have uncovered how water controls such chemical reactions by dynamically coupling with the molecules involved in the process.

Recent advancements at ORNL show that 3D-printed metal molds offer a faster, more cost-effective and flexible approach to producing large composite components for mass-produced vehicles than traditional tooling methods.

UT-Battelle has contributed up to $475,000 for the purchase and installation of advanced manufacturing equipment to support a program at Tennessee’s Oak Ridge High School that gives students direct experience with the AI- and robotics-assisted workplace of the future.

Scientists at ORNL have developed a vacuum-assisted extrusion method that reduces internal porosity by up to 75% in large-scale 3D-printed polymer parts. This new technique addresses the critical issue of porosity in large-scale prints but also paves the way for stronger composites.

The University of Oklahoma and Oak Ridge National Laboratory, the Department of Energy’s largest multi-program science and energy laboratory, have entered a strategic collaboration to establish a cutting-edge additive manufacturing center.

Inspired by a visit to ORNL’s Manufacturing Demonstration Facility, Jonaaron Jones launched a career in additive manufacturing that led to founding Volunteer Aerospace and now leading Beehive Industries’ external parts business. Through close collaboration with MDF, Jones has helped drive innovation in defense, aviation and energy, while growing high-tech jobs and strengthening the U.S. manufacturing base.

During his first visit to Oak Ridge National Laboratory, Energy Secretary Chris Wright compared the urgency of the Lab’s World War II beginnings to today’s global race to lead in artificial intelligence, calling for a “Manhattan Project 2.”

By editing the polymers of discarded plastics, ORNL chemists have found a way to generate new macromolecules with more valuable properties than those of the starting material.