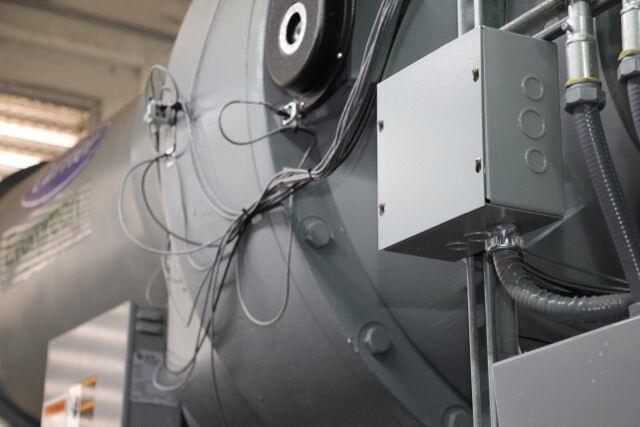
In a career spanning the development of acoustic measuring systems for large-scale projects like ultra-quiet submarines, Randall Wetherington has seen Moore’s Law in action: because of rapid technological advancements, systems that might have cost thousands of dollars to build can now be replaced with a similar version using off-the-shelf hardware costing less than $50.
Wetherington, a researcher in the Electrical and Electronics Systems Research Division, recognized the potential of one such low-cost item—single-board microcomputers—coupled with audio adapters to create a much more cost-effective sensor for monitoring vibrations on industrial machinery.
The device is ideal for detecting issues with equipment containing rotating parts before a minor problem becomes a catastrophic failure. “Machines that have rotating parts in them tend to vibrate,” Wetherington noted. “They vibrate when they’re happy and well, but they also vibrate when they’re unhappy and sick, such as when surfaces start degrading or a bearing is breaking down.”
Using a microphone to capture sound is similar to the function of an accelerometer, he said, in that you’re converting the sound—in this case, vibrations—into a signal that you can then read and analyze with a computer.
“By combining these two little consumer-based gadgets, I can now make the kind of measurements that would have cost hundreds of thousands of dollars previously,” Wetherington said. Bringing the cost down for such a data acquisition system also makes monitoring feasible on other types of equipment: it might be employed on high-speed compressors, electrical generation equipment, inside jet engines, on a commercial air conditioning system, or on board vehicles.
“If you employ this on machines when they’re healthy, you can start listening for how the sound changes and can make a check or repair decision,” Wetherington said. “The faster a machine spins, the more kinetic energy there is, and if it fails it will likely tear itself apart.”
Measuring vibrations on very expensive equipment is crucial, he said. Windmills are another potential application, particularly as larger windmills—generating as much as 1 MW—are deployed to meet renewable energy targets.
Wetherington and his colleagues in the Electro-Mechanical Systems (EMS) Group are currently testing the device on the chillers that keep Oak Ridge National Laboratory’s (ORNL’s) Titan supercomputer running. That system installed in the basement of ORNL’s Building 5600 has been streaming data on 20 channels 24 hours a day for more than 2 years, he noted (see photos).
For the test, Wetherington collaborated with another EMS Group scientist, Larry Phillips, and with Blake Van Hoy, an EMS researcher with expertise on machinery vibrations. The microcontroller boards being used are available online for as little as $35 apiece, with hundreds of models to choose from, Wetherington noted. Daniel Lizama Molina, a mechanical engineering PhD student working with the EESR Division, is currently testing out the capabilities of some newer models.
Future R&D on the project could involve adding more analytics capabilities to the card so that it is a totally self-contained device, thus eliminating the need to send data to a computer for interpretation.