Invention Reference Number
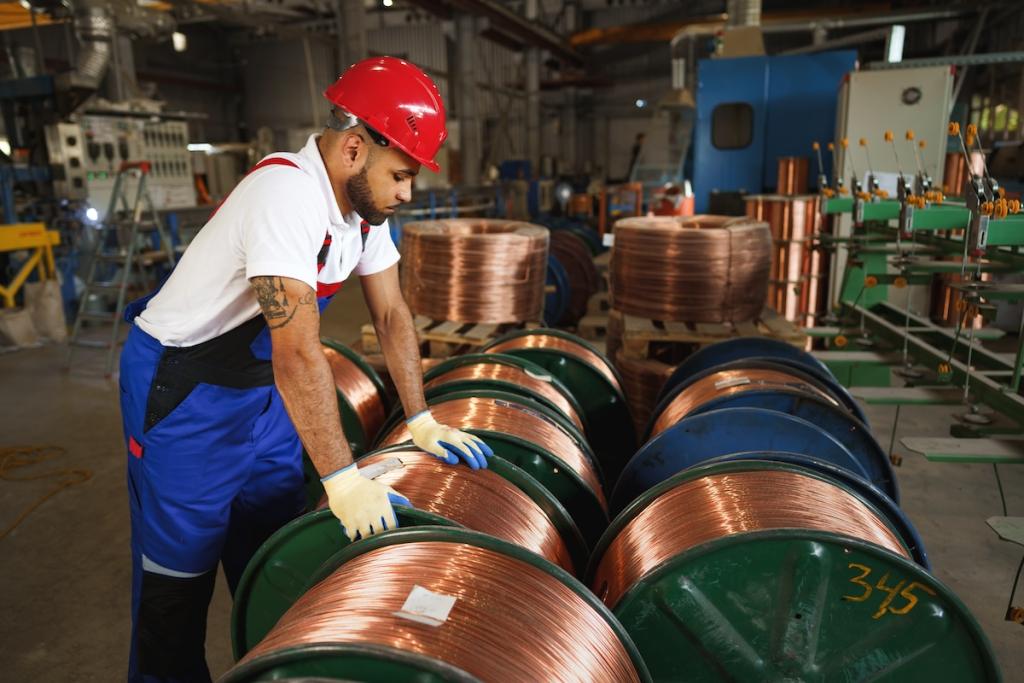
Hybrid manufacturing combining additive and traditional processes can alter the interface condition of material through thermal history modification, deposition energy density, and interface surface preparation through machining to prevent interface cracking. The combination of these manufacturing systems enables a variety of manufacturing options that would otherwise be impossible, such as machining at temperatures above 500 degrees Celsius. This technology will be used to alter the thermal history of the articles to prevent interface cracking between printed copper and steel.
Description:
This technology will increase the thermal response of tooling through the integration of copper and copper alloys within a steel tool, preventing cracking that tends to occur due to the differences in material properties between copper and steel, compromising the integrity of the interface. Additive manufacturing (AM) enables the incremental buildup of monolithic components with a variety of materials, and material deposition locations. This technology alters the interface through thermal history modification, deposition energy density, and interface surface preparation to prevent interface cracking. This does not include a transition zone of a differing material or a graded section which is current state-of-the-art to prevent interface cracking. Negating this transition zone further increases the thermal response between the materials, requires less distance through the interface transition, and minimizes the cracking in the transition zone.
Benefits:
- Better performance
- Less cost, faster cycle times
- More efficient
- High performance and quality that current state-of-the-art manufacturing cannot achieve
Applications and Industries:
- Tooling industry
- Any industry seeking custom tooling needs
- Fusion energy
- Aerospace
Contact:
To learn more about this technology, email partnerships@ornl.gov or call 865-574-1051.