
Filter News
Area of Research
- (-) Advanced Manufacturing (34)
- (-) Biology and Environment (177)
- Biological Systems (18)
- Biology and Soft Matter (5)
- Building Technologies (12)
- Chemical and Engineering Materials (4)
- Chemistry and Physics at Interfaces (11)
- Clean Energy (522)
- Climate and Environmental Systems (14)
- Computational Biology (6)
- Computational Chemistry (5)
- Computational Engineering (5)
- Computer Science (19)
- Data (1)
- Earth Sciences (1)
- Electricity and Smart Grid (3)
- Energy Frontier Research Centers (14)
- Energy Sciences (5)
- Fossil Energy (3)
- Fuel Cycle Science and Technology (3)
- Functional Materials for Energy (16)
- Fusion and Fission (54)
- Fusion Energy (17)
- Geographic Information Science and Technology (3)
- Isotope Development and Production (3)
- Isotopes (35)
- Materials (433)
- Materials Characterization (2)
- Materials for Computing (36)
- Materials Synthesis from Atoms to Systems (13)
- Materials Under Extremes (12)
- Mathematics (1)
- National Security (79)
- Neutron Data Analysis and Visualization (4)
- Neutron Science (190)
- Nuclear Science and Technology (74)
- Nuclear Systems Modeling, Simulation and Validation (3)
- Nuclear Systems Technology (1)
- Quantum Condensed Matter (4)
- Quantum information Science (9)
- Reactor Technology (1)
- Renewable Energy (4)
- Sensors and Controls (5)
- Supercomputing (311)
- Transportation Systems (11)
News Topics
- 3-D Printing/Advanced Manufacturing (33)
- Advanced Reactors (2)
- Artificial Intelligence (10)
- Big Data (9)
- Bioenergy (46)
- Biology (73)
- Biomedical (16)
- Biotechnology (13)
- Buildings (2)
- Chemical Sciences (11)
- Clean Water (11)
- Climate Change (40)
- Composites (8)
- Computer Science (20)
- Coronavirus (13)
- Critical Materials (1)
- Cybersecurity (2)
- Decarbonization (19)
- Energy Storage (7)
- Environment (89)
- Exascale Computing (4)
- Frontier (3)
- Fusion (2)
- Grid (3)
- High-Performance Computing (20)
- Hydropower (8)
- Isotopes (2)
- Machine Learning (9)
- Materials (17)
- Materials Science (11)
- Mathematics (3)
- Mercury (7)
- Microscopy (10)
- Molten Salt (1)
- Nanotechnology (7)
- National Security (3)
- Net Zero (2)
- Neutron Science (6)
- Nuclear Energy (3)
- Partnerships (5)
- Physics (2)
- Polymers (2)
- Renewable Energy (1)
- Security (2)
- Simulation (14)
- Space Exploration (1)
- Summit (10)
- Sustainable Energy (34)
- Transformational Challenge Reactor (2)
- Transportation (3)
Media Contacts

Using additive manufacturing, scientists experimenting with tungsten at Oak Ridge National Laboratory hope to unlock new potential of the high-performance heat-transferring material used to protect components from the plasma inside a fusion reactor. Fusion requires hydrogen isotopes to reach millions of degrees.
A team of scientists led by Oak Ridge National Laboratory have discovered the specific gene that controls an important symbiotic relationship between plants and soil fungi, and successfully facilitated the symbiosis in a plant that
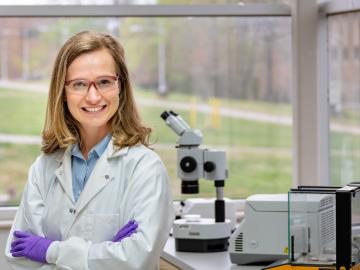
Amber McBride is using her expertise in nanotechnology, drug delivery, and disease models to research fundamental challenges in human health in the ORNL Biosciences Division.

OAK RIDGE, Tenn., May 8, 2019—Oak Ridge National Laboratory and Lincoln Electric (NASDAQ: LECO) announced their continued collaboration on large-scale, robotic additive manufacturing technology at the Department of Energy’s Advanced Manufacturing InnovationXLab Summit.
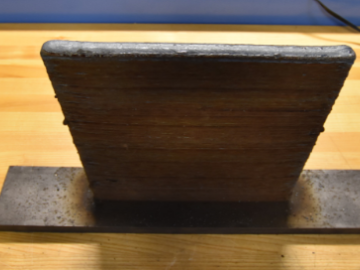
A novel additive manufacturing method developed by researchers at Oak Ridge National Laboratory could be a promising alternative for low-cost, high-quality production of large-scale metal parts with less material waste.
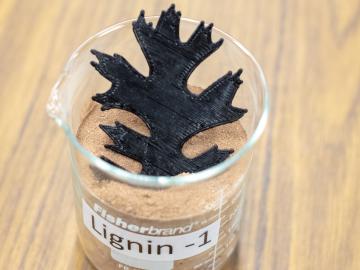
Scientists at the Department of Energy’s Oak Ridge National Laboratory have created a recipe for a renewable 3D printing feedstock that could spur a profitable new use for an intractable biorefinery byproduct: lignin.
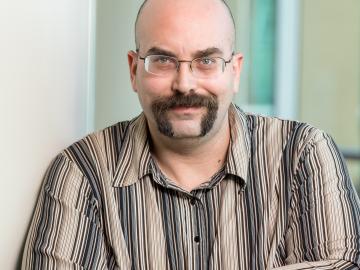
Attracted to biology, math, and physics as a young student, Omar Demerdash decided that when the time came to narrow his academic interests he wouldn’t pick and choose: he’d pursue them all. Today he’s using his expertise in computational biophysics to model and analyze how molecules interact with p...
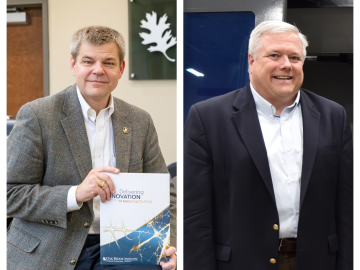
Two leaders in US manufacturing innovation, Thomas Kurfess and Scott Smith, are joining the Department of Energy’s Oak Ridge National Laboratory to support its pioneering research in advanced manufacturing.

The construction industry may soon benefit from 3D printed molds to make concrete facades, promising lower cost and production time. Researchers at Oak Ridge National Laboratory are evaluating the performance of 3D printed molds used to precast concrete facades in a 42-story buildin...