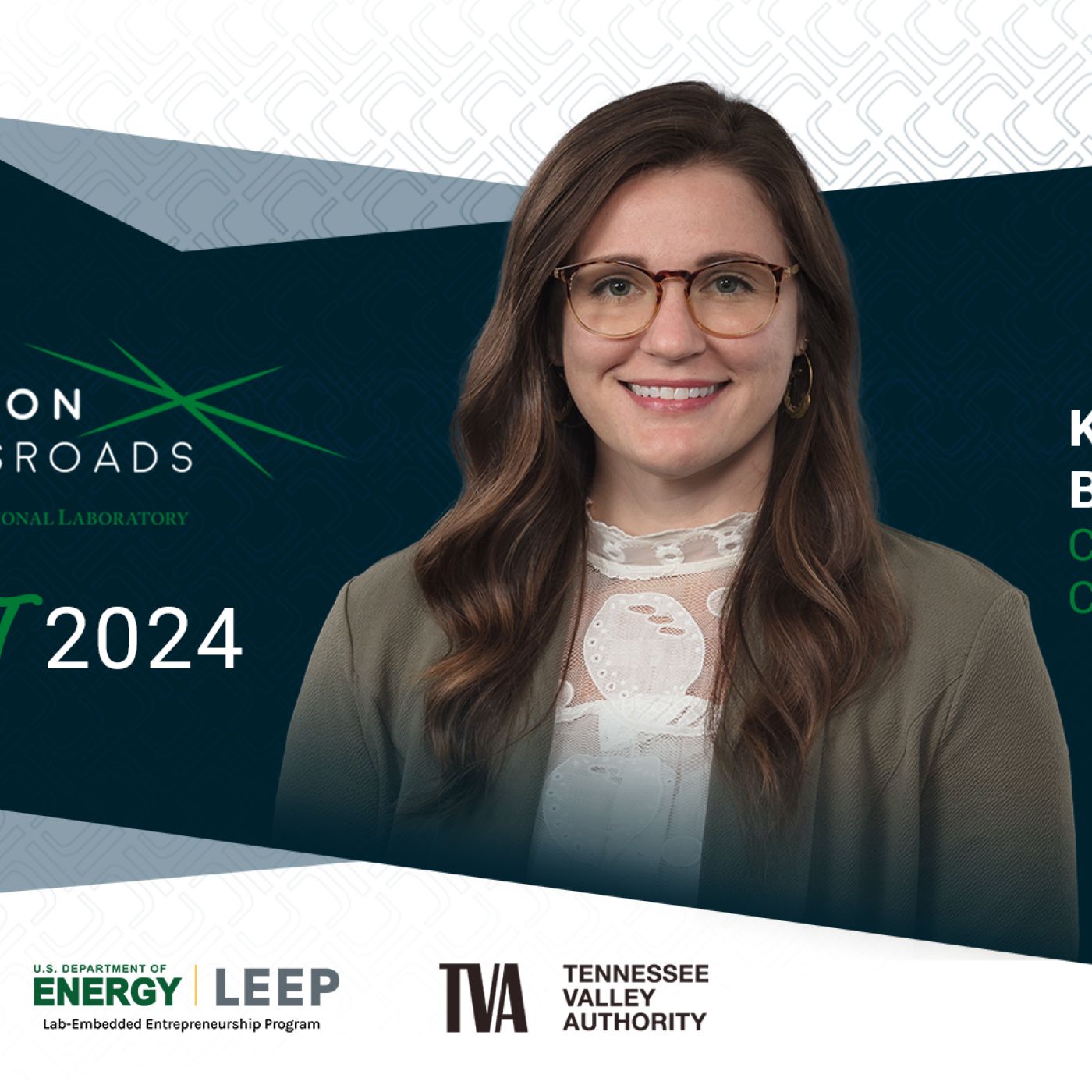
Filter News
Area of Research
News Topics
- (-) 3-D Printing/Advanced Manufacturing (10)
- (-) Biomedical (3)
- (-) Composites (3)
- (-) Grid (7)
- (-) Materials Science (12)
- Advanced Reactors (6)
- Artificial Intelligence (8)
- Big Data (8)
- Bioenergy (4)
- Biology (5)
- Buildings (8)
- Chemical Sciences (2)
- Clean Water (5)
- Climate Change (3)
- Computer Science (19)
- Coronavirus (4)
- Critical Materials (3)
- Cybersecurity (1)
- Decarbonization (1)
- Energy Storage (10)
- Environment (11)
- Exascale Computing (1)
- Fusion (3)
- High-Performance Computing (4)
- Hydropower (5)
- Irradiation (1)
- Isotopes (1)
- Machine Learning (5)
- Materials (11)
- Microscopy (5)
- Molten Salt (1)
- Nanotechnology (4)
- National Security (3)
- Neutron Science (10)
- Nuclear Energy (9)
- Partnerships (1)
- Physics (3)
- Polymers (2)
- Quantum Science (5)
- Simulation (2)
- Space Exploration (6)
- Summit (3)
- Sustainable Energy (8)
- Transportation (9)
Media Contacts
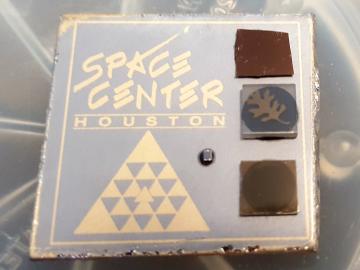
To study how space radiation affects materials for spacecraft and satellites, Oak Ridge National Laboratory scientists sent samples to the International Space Station. The results will inform design of radiation-resistant magnetic and electronic systems.
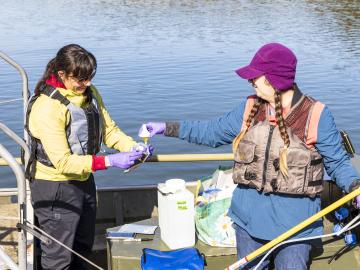
Researchers at Oak Ridge National Laboratory are using a novel approach in determining environmental impacts to aquatic species near hydropower facilities, potentially leading to smarter facility designs that can support electrical grid reliability.
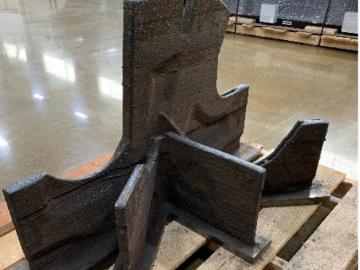
Oak Ridge National Laboratory researchers recently used large-scale additive manufacturing with metal to produce a full-strength steel component for a wind turbine, proving the technique as a viable alternative to
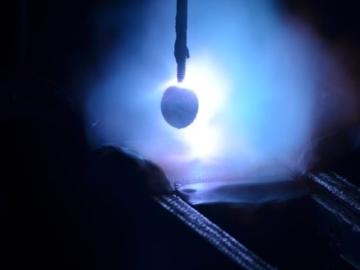
Researchers at Oak Ridge National Laboratory demonstrated that an additively manufactured polymer layer, when applied to carbon fiber reinforced plastic, or CFRP, can serve as an effective protector against aircraft lightning strikes.
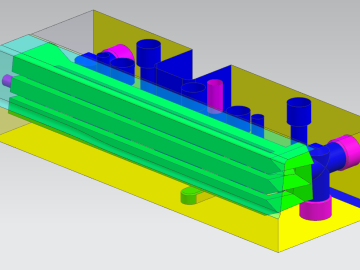
Researchers demonstrated that an additively manufactured hot stamping die can withstand up to 25,000 usage cycles, proving that this technique is a viable solution for production.

Researchers at Oak Ridge National Laboratory proved that a certain class of ionic liquids, when mixed with commercially available oils, can make gears run more efficiently with less noise and better durability.

A team including Oak Ridge National Laboratory and University of Tennessee researchers demonstrated a novel 3D printing approach called Z-pinning that can increase the material’s strength and toughness by more than three and a half times compared to conventional additive manufacturing processes.

Using additive manufacturing, scientists experimenting with tungsten at Oak Ridge National Laboratory hope to unlock new potential of the high-performance heat-transferring material used to protect components from the plasma inside a fusion reactor. Fusion requires hydrogen isotopes to reach millions of degrees.

A new method developed at Oak Ridge National Laboratory improves the energy efficiency of a desalination process known as solar-thermal evaporation.
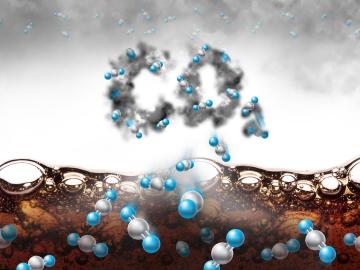
Oak Ridge National Laboratory has teamed with Cornell College and the University of Tennessee to study ways to repurpose waste soft drinks for carbon capture that could help cut carbon dioxide emissions.