Filter News
Area of Research
News Type
News Topics
- (-) Biology (6)
- (-) Materials (17)
- 3-D Printing/Advanced Manufacturing (45)
- Advanced Reactors (2)
- Artificial Intelligence (3)
- Big Data (1)
- Bioenergy (12)
- Biomedical (3)
- Biotechnology (2)
- Buildings (24)
- Chemical Sciences (4)
- Clean Water (7)
- Climate Change (14)
- Composites (11)
- Computer Science (16)
- Coronavirus (7)
- Critical Materials (4)
- Cybersecurity (5)
- Decarbonization (19)
- Energy Storage (41)
- Environment (33)
- Fossil Energy (1)
- Grid (28)
- High-Performance Computing (3)
- Hydropower (2)
- Machine Learning (2)
- Materials Science (13)
- Mathematics (2)
- Mercury (2)
- Microelectronics (1)
- Microscopy (4)
- Nanotechnology (3)
- National Security (1)
- Net Zero (2)
- Neutron Science (2)
- Nuclear Energy (3)
- Partnerships (4)
- Polymers (6)
- Quantum Science (1)
- Security (3)
- Simulation (2)
- Space Exploration (3)
- Statistics (1)
- Summit (2)
- Sustainable Energy (41)
- Transportation (43)
Media Contacts
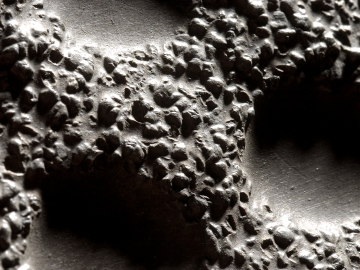
For more than 100 years, Magotteaux has provided grinding materials and castings for the mining, cement and aggregates industries. The company, based in Belgium, began its international expansion in 1968. Its second international plant has been a critical part of the Pulaski, Tennessee, economy since 1972.
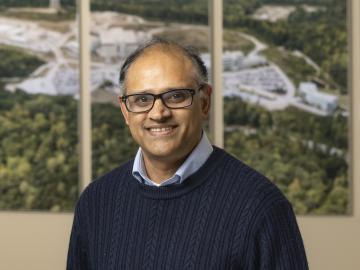
Having passed the midpoint of his career, physicist Mali Balasubramanian was part of a tight-knit team at a premier research facility for X-ray spectroscopy. But then another position opened, at ORNL— one that would take him in a new direction.
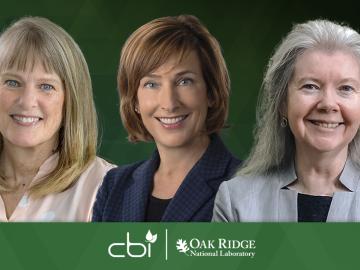
The Department of Energy’s Center for Bioenergy Innovation, led by Oak Ridge National Laboratory, recently added three new members to its board of directors: Deborah Crawford of the University of Tennessee, Knoxville; Susan Hubbard of ORNL; and Maureen McCann of the National Renewable Energy Laboratory.

ORNL researchers have identified a mechanism in a 3D-printed alloy – termed “load shuffling” — that could enable the design of better-performing lightweight materials for vehicles.

Oak Ridge National Laboratory scientists designed a recyclable polymer for carbon-fiber composites to enable circular manufacturing of parts that boost energy efficiency in automotive, wind power and aerospace applications.

Materials scientist Denise Antunes da Silva researches ways to reduce concrete’s embodied carbon in the Sustainable Building Materials Laboratory at ORNL, a research space dedicated to studying environmentally friendly building materials. Credit: ORNL, U.S. Dept. of Energy

Tackling the climate crisis and achieving an equitable clean energy future are among the biggest challenges of our time.

Oak Ridge National Laboratory researchers have developed a novel process to manufacture extreme heat resistant carbon-carbon composites. The performance of these materials will be tested in a U.S. Navy rocket that NASA will launch this fall.
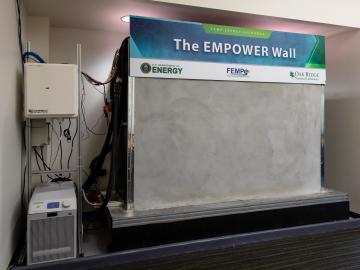
Oak Ridge National Laboratory researchers demonstrated that cooling cost savings could be achieved with a 3D printed concrete smart wall following a three-month field test.

A research team at Oak Ridge National Laboratory have 3D printed a thermal protection shield, or TPS, for a capsule that will launch with the Cygnus cargo spacecraft as part of the supply mission to the International Space Station.