
Filter News
Area of Research
- (-) Fusion and Fission (32)
- (-) Materials (122)
- Advanced Manufacturing (5)
- Biological Systems (1)
- Biology and Environment (102)
- Biology and Soft Matter (4)
- Building Technologies (2)
- Chemical and Engineering Materials (3)
- Chemistry and Physics at Interfaces (7)
- Clean Energy (168)
- Climate and Environmental Systems (7)
- Computational Biology (1)
- Computational Chemistry (5)
- Computational Engineering (1)
- Computer Science (3)
- Data (1)
- Earth Sciences (1)
- Electricity and Smart Grid (1)
- Energy Frontier Research Centers (7)
- Fuel Cycle Science and Technology (2)
- Functional Materials for Energy (8)
- Fusion Energy (7)
- Geographic Information Science and Technology (1)
- Isotopes (21)
- Materials for Computing (13)
- Materials Synthesis from Atoms to Systems (8)
- Materials Under Extremes (7)
- National Security (45)
- Neutron Data Analysis and Visualization (2)
- Neutron Science (72)
- Nuclear Science and Technology (27)
- Quantum Condensed Matter (3)
- Quantum information Science (4)
- Renewable Energy (2)
- Sensors and Controls (2)
- Supercomputing (153)
- Transportation Systems (4)
News Type
News Topics
- 3-D Printing/Advanced Manufacturing (7)
- Advanced Reactors (3)
- Artificial Intelligence (5)
- Big Data (2)
- Bioenergy (2)
- Biomedical (2)
- Buildings (1)
- Chemical Sciences (8)
- Clean Water (2)
- Composites (2)
- Computer Science (9)
- Coronavirus (1)
- Cybersecurity (1)
- Decarbonization (2)
- Energy Storage (7)
- Environment (8)
- Exascale Computing (2)
- Frontier (1)
- Fusion (14)
- Grid (2)
- High-Performance Computing (3)
- Isotopes (6)
- ITER (2)
- Machine Learning (2)
- Materials (19)
- Materials Science (17)
- Mathematics (1)
- Microscopy (6)
- Nanotechnology (8)
- Net Zero (1)
- Neutron Science (9)
- Nuclear Energy (26)
- Partnerships (3)
- Physics (12)
- Polymers (4)
- Quantum Computing (1)
- Security (2)
- Simulation (2)
- Space Exploration (1)
- Summit (1)
- Sustainable Energy (5)
- Transformational Challenge Reactor (2)
- Transportation (5)
Media Contacts

Two decades in the making, a new flagship facility for nuclear physics opened on May 2, and scientists from the Department of Energy’s Oak Ridge National Laboratory have a hand in 10 of its first 34 experiments.

Practical fusion energy is not just a dream at ORNL. Experts in fusion and material science are working together to develop solutions that will make a fusion pilot plant — and ultimately carbon-free, abundant fusion electricity — possible.

Friederike (Rike) Bostelmann, who began her career in Germany, chose to come to ORNL to become part of the Lab’s efforts to shape the future of nuclear energy.

To achieve practical energy from fusion, extreme heat from the fusion system “blanket” component must be extracted safely and efficiently. ORNL fusion experts are exploring how tiny 3D-printed obstacles placed inside the narrow pipes of a custom-made cooling system could be a solution for removing heat from the blanket.

A study led by researchers at ORNL could help make materials design as customizable as point-and-click.
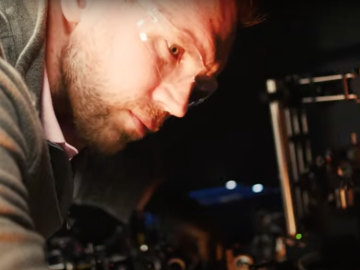
ORNL manages the Innovation Network for Fusion Energy Program, or INFUSE, with Princeton Plasma Physics Laboratory, to help the private sector find solutions to technical challenges that need to be resolved to make practical fusion energy a reality.

Neuromorphic devices — which emulate the decision-making processes of the human brain — show great promise for solving pressing scientific problems, but building physical systems to realize this potential presents researchers with a significant

A multidisciplinary team of scientists at ORNL has applied a laser-interference structuring, or LIS, technique that makes significant strides toward eliminating the need for hazardous chemicals in corrosion protection for vehicles.

The receipt of a nuclear fuel canister is boosting the research of an Oak Ridge National Laboratory team investigating methods to help the nation effectively dispose of nuclear waste for the long term.
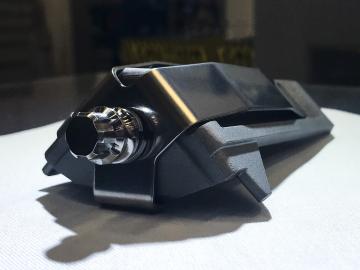
Four first-of-a-kind 3D-printed fuel assembly brackets, produced at the Department of Energy’s Manufacturing Demonstration Facility at Oak Ridge National Laboratory, have been installed and are now under routine operating