
Filter News
Area of Research
News Topics
- (-) Advanced Reactors (8)
- (-) Clean Water (14)
- (-) Molten Salt (1)
- 3-D Printing/Advanced Manufacturing (39)
- Artificial Intelligence (46)
- Big Data (24)
- Bioenergy (51)
- Biology (59)
- Biomedical (28)
- Biotechnology (11)
- Buildings (19)
- Chemical Sciences (24)
- Climate Change (50)
- Composites (6)
- Computer Science (83)
- Coronavirus (17)
- Critical Materials (2)
- Cybersecurity (14)
- Decarbonization (46)
- Education (1)
- Emergency (2)
- Energy Storage (29)
- Environment (104)
- Exascale Computing (25)
- Fossil Energy (4)
- Frontier (24)
- Fusion (31)
- Grid (23)
- High-Performance Computing (44)
- Hydropower (5)
- Isotopes (27)
- ITER (2)
- Machine Learning (22)
- Materials (43)
- Materials Science (45)
- Mathematics (6)
- Mercury (7)
- Microelectronics (2)
- Microscopy (20)
- Nanotechnology (16)
- National Security (36)
- Net Zero (8)
- Neutron Science (47)
- Nuclear Energy (55)
- Partnerships (16)
- Physics (28)
- Polymers (8)
- Quantum Computing (20)
- Quantum Science (30)
- Renewable Energy (1)
- Security (11)
- Simulation (31)
- Software (1)
- Space Exploration (12)
- Statistics (1)
- Summit (30)
- Sustainable Energy (44)
- Transformational Challenge Reactor (3)
- Transportation (27)
Media Contacts

Anyone familiar with ORNL knows it’s a hub for world-class science. The nearly 33,000-acre space surrounding the lab is less known, but also unique.

Moving to landlocked Tennessee isn’t an obvious choice for most scientists with new doctorate degrees in coastal oceanography.
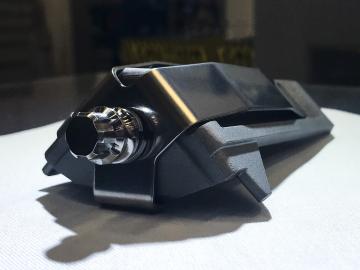
Four first-of-a-kind 3D-printed fuel assembly brackets, produced at the Department of Energy’s Manufacturing Demonstration Facility at Oak Ridge National Laboratory, have been installed and are now under routine operating

New capabilities and equipment recently installed at the Department of Energy’s Oak Ridge National Laboratory are bringing a creek right into the lab to advance understanding of mercury pollution and accelerate solutions.
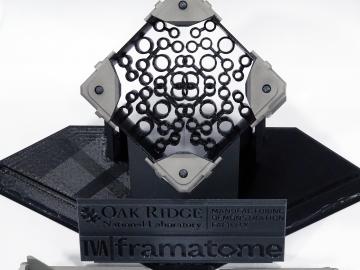
The Transformational Challenge Reactor, or TCR, a microreactor built using 3D printing and other new advanced technologies, could be operational by 2024.
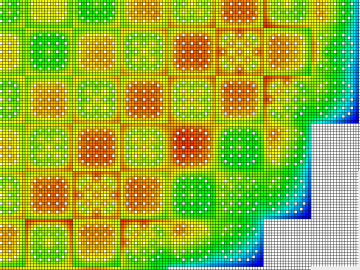
As CASL ends and transitions to VERA Users Group, ORNL looks at the history of the program and its impact on the nuclear industry.
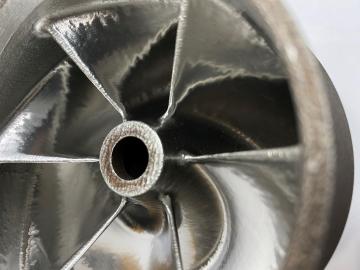
Scientists at the Department of Energy Manufacturing Demonstration Facility at ORNL have their eyes on the prize: the Transformational Challenge Reactor, or TCR, a microreactor built using 3D printing and other new approaches that will be up and running by 2023.
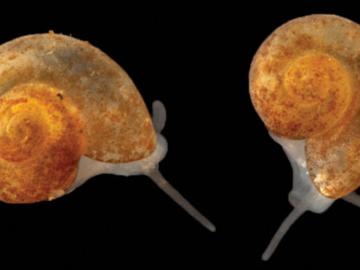
Sometimes conducting big science means discovering a species not much larger than a grain of sand.
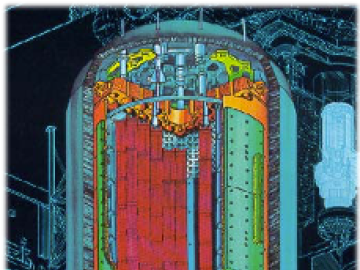
A software package, 10 years in the making, that can predict the behavior of nuclear reactors’ cores with stunning accuracy has been licensed commercially for the first time.

While Tsouris’ water research is diverse in scope, its fundamentals are based on basic science principles that remain largely unchanged, particularly in a mature field like chemical engineering.