Filter News
Area of Research
News Topics
- (-) Advanced Reactors (8)
- (-) Molten Salt (1)
- (-) Polymers (7)
- 3-D Printing/Advanced Manufacturing (34)
- Artificial Intelligence (43)
- Big Data (21)
- Bioenergy (48)
- Biology (56)
- Biomedical (28)
- Biotechnology (10)
- Buildings (17)
- Chemical Sciences (21)
- Clean Water (14)
- Climate Change (46)
- Composites (5)
- Computer Science (80)
- Coronavirus (17)
- Critical Materials (1)
- Cybersecurity (14)
- Decarbonization (43)
- Education (1)
- Emergency (2)
- Energy Storage (28)
- Environment (100)
- Exascale Computing (24)
- Fossil Energy (4)
- Frontier (23)
- Fusion (28)
- Grid (23)
- High-Performance Computing (42)
- Hydropower (5)
- Isotopes (25)
- ITER (2)
- Machine Learning (21)
- Materials (39)
- Materials Science (41)
- Mathematics (5)
- Mercury (7)
- Microelectronics (2)
- Microscopy (20)
- Nanotechnology (16)
- National Security (33)
- Net Zero (8)
- Neutron Science (46)
- Nuclear Energy (52)
- Partnerships (13)
- Physics (26)
- Quantum Computing (17)
- Quantum Science (27)
- Renewable Energy (1)
- Security (10)
- Simulation (29)
- Software (1)
- Space Exploration (12)
- Summit (30)
- Sustainable Energy (42)
- Transformational Challenge Reactor (3)
- Transportation (27)
Media Contacts

Researchers tackling national security challenges at ORNL are upholding an 80-year legacy of leadership in all things nuclear. Today, they’re developing the next generation of technologies that will help reduce global nuclear risk and enable safe, secure, peaceful use of nuclear materials, worldwide.
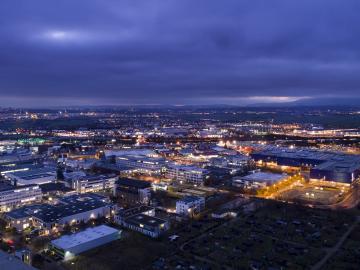
Scientists at Oak Ridge National Laboratory and six other Department of Energy national laboratories have developed a United States-based perspective for achieving net-zero carbon emissions.

Tomonori Saito, a distinguished innovator in the field of polymer science and senior R&D staff member at ORNL, was honored on May 11 in Columbus, Ohio, at Battelle’s Celebration of Solvers.

Chemist Jeff Foster is looking for ways to control sequencing in polymers that could result in designer molecules to benefit a variety of industries, including medicine and energy.

Chemical and environmental engineer Samarthya Bhagia is focused on achieving carbon neutrality and a circular economy by designing new plant-based materials for a range of applications from energy storage devices and sensors to environmentally friendly bioplastics.
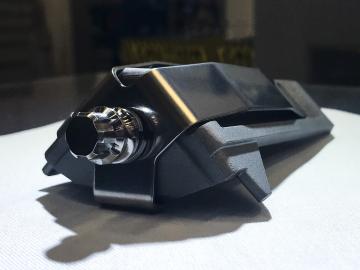
Four first-of-a-kind 3D-printed fuel assembly brackets, produced at the Department of Energy’s Manufacturing Demonstration Facility at Oak Ridge National Laboratory, have been installed and are now under routine operating

When COVID-19 was declared a pandemic in March 2020, Oak Ridge National Laboratory’s Parans Paranthaman suddenly found himself working from home like millions of others.
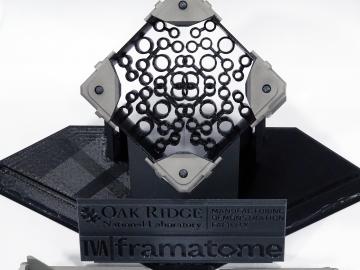
The Transformational Challenge Reactor, or TCR, a microreactor built using 3D printing and other new advanced technologies, could be operational by 2024.
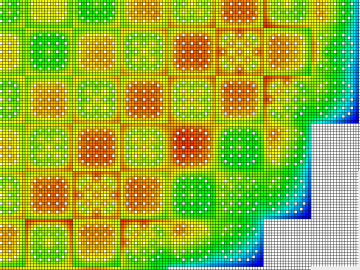
As CASL ends and transitions to VERA Users Group, ORNL looks at the history of the program and its impact on the nuclear industry.
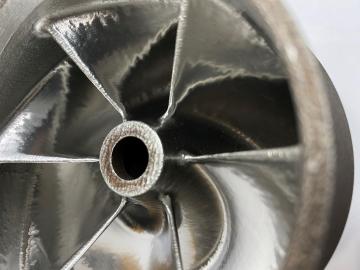
Scientists at the Department of Energy Manufacturing Demonstration Facility at ORNL have their eyes on the prize: the Transformational Challenge Reactor, or TCR, a microreactor built using 3D printing and other new approaches that will be up and running by 2023.