
Filter News
Area of Research
News Topics
- (-) 3-D Printing/Advanced Manufacturing (37)
- (-) Fusion (30)
- Advanced Reactors (8)
- Artificial Intelligence (46)
- Big Data (22)
- Bioenergy (50)
- Biology (58)
- Biomedical (28)
- Biotechnology (11)
- Buildings (18)
- Chemical Sciences (22)
- Clean Water (14)
- Climate Change (48)
- Composites (6)
- Computer Science (82)
- Coronavirus (17)
- Critical Materials (2)
- Cybersecurity (14)
- Decarbonization (45)
- Education (1)
- Emergency (2)
- Energy Storage (28)
- Environment (101)
- Exascale Computing (25)
- Fossil Energy (4)
- Frontier (24)
- Grid (23)
- High-Performance Computing (43)
- Hydropower (5)
- Isotopes (27)
- ITER (2)
- Machine Learning (22)
- Materials (41)
- Materials Science (44)
- Mathematics (6)
- Mercury (7)
- Microelectronics (2)
- Microscopy (20)
- Molten Salt (1)
- Nanotechnology (16)
- National Security (35)
- Net Zero (8)
- Neutron Science (47)
- Nuclear Energy (54)
- Partnerships (16)
- Physics (28)
- Polymers (8)
- Quantum Computing (20)
- Quantum Science (30)
- Renewable Energy (1)
- Security (11)
- Simulation (30)
- Software (1)
- Space Exploration (12)
- Summit (30)
- Sustainable Energy (43)
- Transformational Challenge Reactor (3)
- Transportation (27)
Media Contacts
A collaboration between the ORNL and a Florida-based medical device manufacturer has led to the addition of 500 jobs in the Miami area to support the mass production of N95 respirator masks.
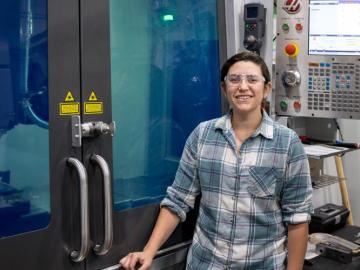
Growing up in Florida, Emma Betters was fascinated by rockets and for good reason. Any time she wanted to see a space shuttle launch from NASA’s nearby Kennedy Space Center, all she had to do was sit on her front porch.
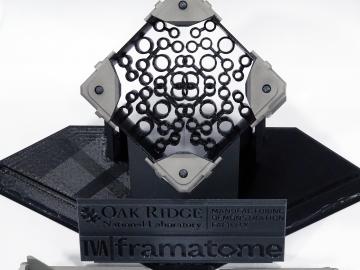
The Transformational Challenge Reactor, or TCR, a microreactor built using 3D printing and other new advanced technologies, could be operational by 2024.
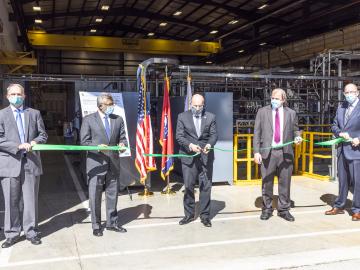
Department of Energy Under Secretary for Science Paul Dabbar joined Oak Ridge National Laboratory leaders for a ribbon-cutting ceremony to mark progress toward a next-generation fusion materials project.
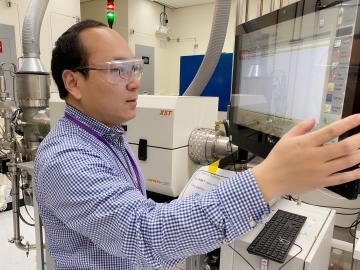
About 60 years ago, scientists discovered that a certain rare earth metal-hydrogen mixture, yttrium, could be the ideal moderator to go inside small, gas-cooled nuclear reactors.
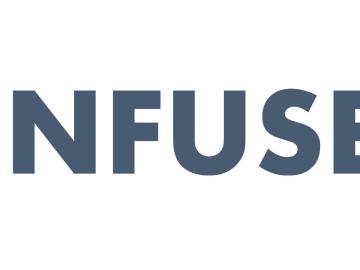
The Department of Energy announced awards for 10 projects with private industry that will allow for collaboration with DOE national laboratories in accelerating fusion energy development.

The inside of future nuclear fusion energy reactors will be among the harshest environments ever produced on Earth. What’s strong enough to protect the inside of a fusion reactor from plasma-produced heat fluxes akin to space shuttles reentering Earth’s atmosphere?
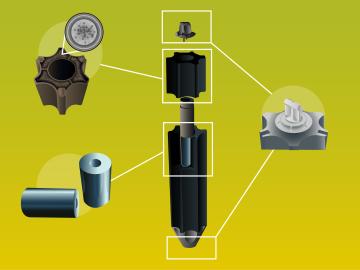
It’s a new type of nuclear reactor core. And the materials that will make it up are novel — products of Oak Ridge National Laboratory’s advanced materials and manufacturing technologies.
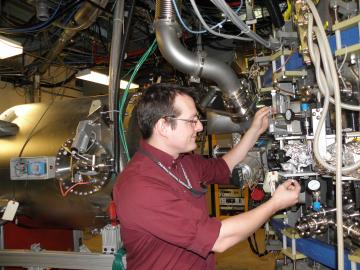
Lithium, the silvery metal that powers smart phones and helps treat bipolar disorders, could also play a significant role in the worldwide effort to harvest on Earth the safe, clean and virtually limitless fusion energy that powers the sun and stars.

Temperatures hotter than the center of the sun. Magnetic fields hundreds of thousands of times stronger than the earth’s. Neutrons energetic enough to change the structure of a material entirely.