
Filter News
Area of Research
- Advanced Manufacturing (14)
- Biology and Environment (45)
- Biology and Soft Matter (1)
- Building Technologies (1)
- Clean Energy (108)
- Climate and Environmental Systems (2)
- Computational Engineering (1)
- Fusion and Fission (5)
- Fusion Energy (2)
- Isotopes (19)
- Materials (31)
- Materials for Computing (6)
- Mathematics (1)
- National Security (18)
- Neutron Science (8)
- Nuclear Science and Technology (7)
- Quantum information Science (1)
- Supercomputing (34)
- Transportation Systems (2)
News Type
News Topics
- (-) 3-D Printing/Advanced Manufacturing (72)
- (-) Climate Change (72)
- (-) Cybersecurity (17)
- (-) Frontier (25)
- (-) Isotopes (32)
- (-) Mercury (10)
- (-) Security (12)
- (-) Space Exploration (22)
- (-) Transportation (62)
- Advanced Reactors (21)
- Artificial Intelligence (61)
- Big Data (43)
- Bioenergy (67)
- Biology (78)
- Biomedical (40)
- Biotechnology (14)
- Buildings (38)
- Chemical Sciences (35)
- Clean Water (27)
- Composites (17)
- Computer Science (126)
- Coronavirus (28)
- Critical Materials (15)
- Decarbonization (55)
- Education (1)
- Emergency (2)
- Energy Storage (60)
- Environment (147)
- Exascale Computing (27)
- Fossil Energy (5)
- Fusion (40)
- Grid (46)
- High-Performance Computing (55)
- Hydropower (11)
- Irradiation (2)
- ITER (5)
- Machine Learning (33)
- Materials (78)
- Materials Science (79)
- Mathematics (9)
- Microelectronics (2)
- Microscopy (31)
- Molten Salt (6)
- Nanotechnology (28)
- National Security (42)
- Net Zero (10)
- Neutron Science (74)
- Nuclear Energy (74)
- Partnerships (19)
- Physics (33)
- Polymers (17)
- Quantum Computing (25)
- Quantum Science (40)
- Renewable Energy (1)
- Simulation (39)
- Software (1)
- Statistics (2)
- Summit (36)
- Sustainable Energy (92)
- Transformational Challenge Reactor (3)
Media Contacts

Brittany Rodriguez never imagined she would pursue a science career at a Department of Energy national laboratory. However, after some encouraging words from her mother, input from key mentors at the University of Texas Rio Grande Valley, or UTRGV, and a lot of hard work, Rodriguez landed at DOE’s Manufacturing Demonstration Facility, or MDF, at Oak Ridge National Laboratory.
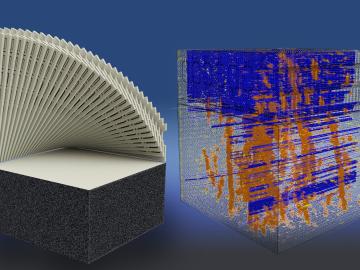
The Department of Energy’s Oak Ridge National Laboratory has publicly released a new set of additive manufacturing data that industry and researchers can use to evaluate and improve the quality of 3D-printed components. The breadth of the datasets can significantly boost efforts to verify the quality of additively manufactured parts using only information gathered during printing, without requiring expensive and time-consuming post-production analysis.

In the wet, muddy places where America’s rivers and lands meet the sea, scientists from the Department of Energy’s Oak Ridge National Laboratory are unearthing clues to better understand how these vital landscapes are evolving under climate change.
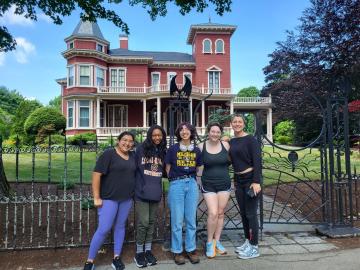
Participants in the SM2ART Research Experience for Undergraduates program got the chance to see what life is like in a research setting. REU participant Brianna Greer studied banana fibers as a reinforcing material in making lightweight parts for cars and bicycles.

Advanced materials research to enable energy-efficient, cost-competitive and environmentally friendly technologies for the United States and Japan is the goal of a memorandum of understanding, or MOU, between the Department of Energy’s Oak Ridge National Laboratory and Japan’s National Institute of Materials Science.

Researchers at ORNL have developed the first additive manufacturing slicing computer application to simultaneously speed and simplify digital conversion of accurate, large-format three-dimensional parts in a factory production setting.
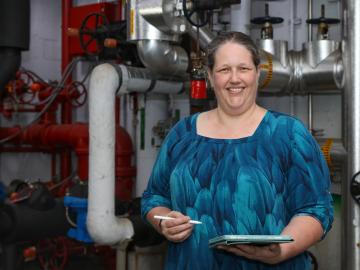
Sara Martinez ensures the safety and longevity of aging structures at Oak Ridge National Laboratory, employing her engineering expertise to protect against natural disasters and extend the lifespan of critical facilities.

Researchers at Oak Ridge National Laboratory have developed free data sets to estimate how much energy any building in the contiguous U.S. will use in 2100. These data sets provide planners a way to anticipate future energy needs as the climate changes.

When Oak Ridge National Laboratory's science mission takes staff off-campus, the lab’s safety principles follow. That’s true even in the high mountain passes of Washington and Oregon, where ORNL scientists are tracking a tree species — and where wildfires have become more frequent and widespread.

Oak Ridge National Laboratory scientists ingeniously created a sustainable, soft material by combining rubber with woody reinforcements and incorporating “smart” linkages between the components that unlock on demand.