
Filter News
Area of Research
- Advanced Manufacturing (18)
- Biological Systems (1)
- Biology and Environment (39)
- Building Technologies (1)
- Clean Energy (77)
- Climate and Environmental Systems (1)
- Computational Engineering (1)
- Fusion and Fission (4)
- Fusion Energy (7)
- Isotopes (9)
- Materials (35)
- Materials for Computing (5)
- Mathematics (1)
- National Security (4)
- Neutron Science (7)
- Nuclear Science and Technology (11)
- Nuclear Systems Modeling, Simulation and Validation (1)
- Supercomputing (23)
News Type
News Topics
- (-) 3-D Printing/Advanced Manufacturing (75)
- (-) Advanced Reactors (23)
- (-) Bioenergy (39)
- (-) Climate Change (44)
- (-) Exascale Computing (10)
- (-) Isotopes (23)
- Artificial Intelligence (42)
- Big Data (24)
- Biology (39)
- Biomedical (28)
- Biotechnology (10)
- Buildings (32)
- Chemical Sciences (38)
- Clean Water (14)
- Composites (18)
- Computer Science (96)
- Coronavirus (28)
- Critical Materials (23)
- Cybersecurity (20)
- Decarbonization (27)
- Education (3)
- Element Discovery (1)
- Energy Storage (72)
- Environment (79)
- Fossil Energy (1)
- Frontier (15)
- Fusion (23)
- Grid (35)
- High-Performance Computing (37)
- Hydropower (6)
- Irradiation (2)
- ITER (5)
- Machine Learning (23)
- Materials (94)
- Materials Science (83)
- Mathematics (1)
- Mercury (5)
- Microelectronics (1)
- Microscopy (27)
- Molten Salt (7)
- Nanotechnology (38)
- National Security (21)
- Net Zero (4)
- Neutron Science (76)
- Nuclear Energy (45)
- Partnerships (28)
- Physics (28)
- Polymers (21)
- Quantum Computing (13)
- Quantum Science (36)
- Renewable Energy (1)
- Security (12)
- Simulation (15)
- Space Exploration (13)
- Statistics (3)
- Summit (26)
- Sustainable Energy (75)
- Transformational Challenge Reactor (4)
- Transportation (60)
Media Contacts
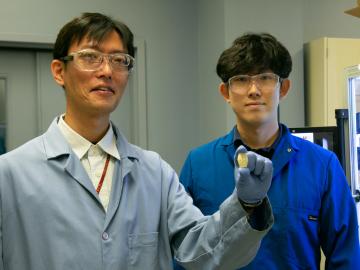
ORNL researchers have developed an upcycling approach that adds value to discarded plastics for reuse in additive manufacturing, or 3D printing.

Doug Kothe has been named associate laboratory director for the Computing and Computational Sciences Directorate at ORNL, effective June 6.
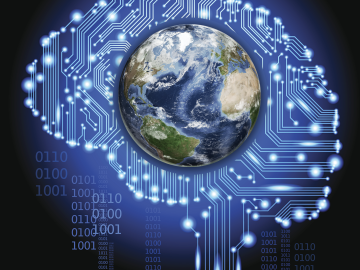
Oak Ridge National Laboratory researchers developed an invertible neural network, a type of artificial intelligence that mimics the human brain, to improve accuracy in climate-change models and predictions.
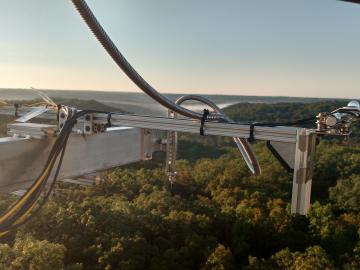
Technology developed at ORNL to monitor plant productivity and health at wide scales has been licensed to Logan, Utah-based instrumentation firm Campbell Scientific Inc.

The Frontier supercomputer at the Department of Energy’s Oak Ridge National Laboratory earned the top ranking today as the world’s fastest on the 59th TOP500 list, with 1.1 exaflops of performance. The system is the first to achieve an unprecedented level of computing performance known as exascale, a threshold of a quintillion calculations per second.
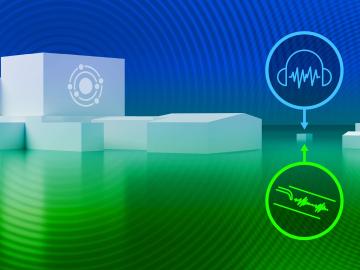
An Oak Ridge National Laboratory team developed a novel technique using sensors to monitor seismic and acoustic activity and machine learning to differentiate operational activities at facilities from “noise” in the recorded data.
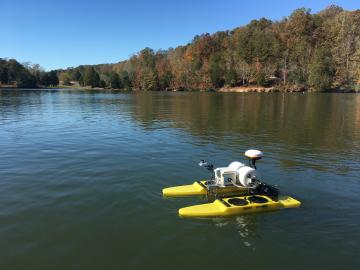
Measuring water quality throughout river networks with precision, speed and at lower cost than traditional methods is now possible with AquaBOT, an aquatic drone developed by Oak Ridge National Laboratory.

ORNL and the Tennessee Valley Authority, or TVA, are joining forces to advance decarbonization technologies from discovery through deployment through a new memorandum of understanding, or MOU.

ORNL, TVA and TNECD were recognized by the Federal Laboratory Consortium for their impactful partnership that resulted in a record $2.3 billion investment by Ultium Cells, a General Motors and LG Energy Solution joint venture, to build a battery cell manufacturing plant in Spring Hill, Tennessee.
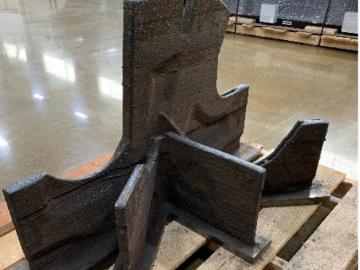
Oak Ridge National Laboratory researchers recently used large-scale additive manufacturing with metal to produce a full-strength steel component for a wind turbine, proving the technique as a viable alternative to