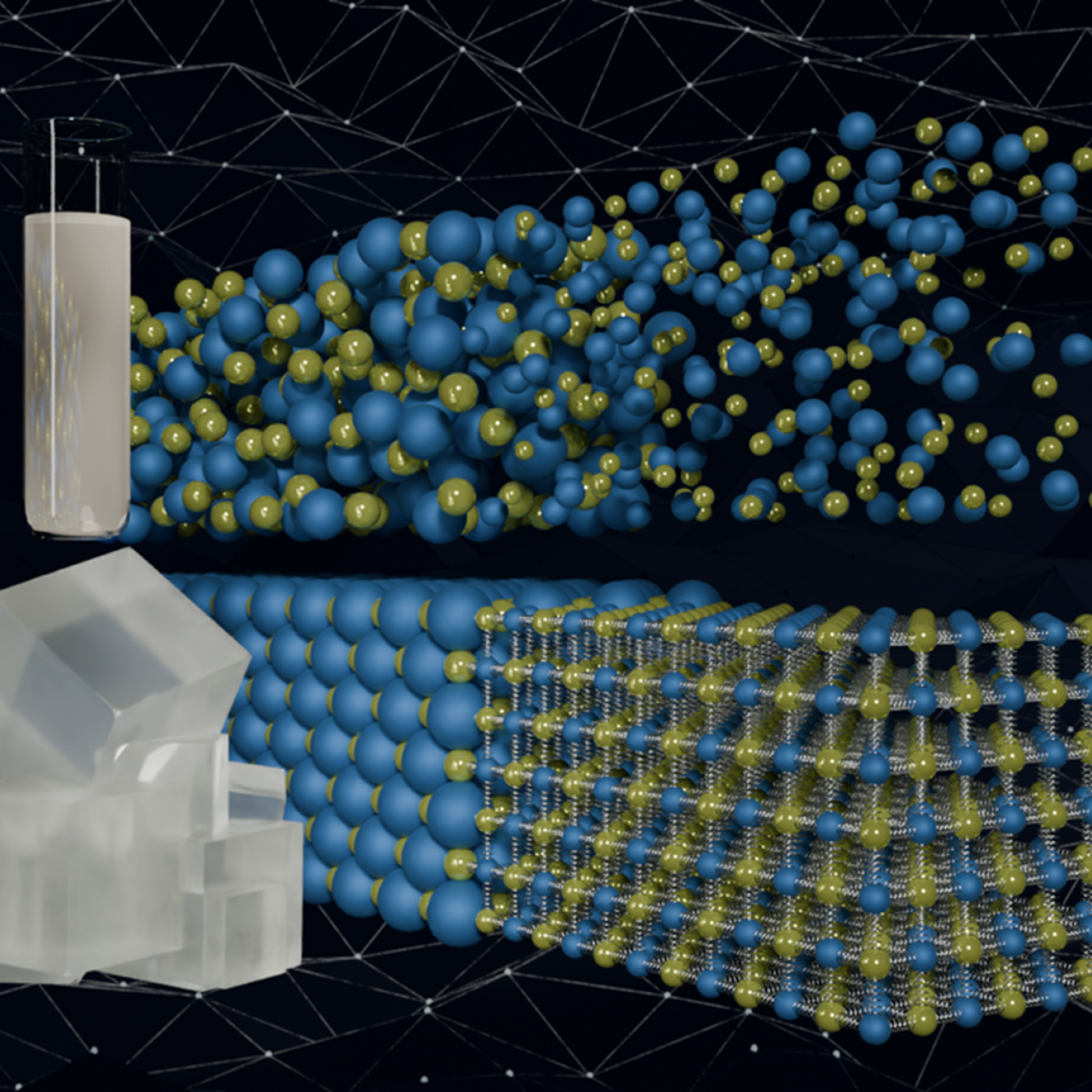
Filter News
Area of Research
News Type
News Topics
- (-) 3-D Printing/Advanced Manufacturing (48)
- (-) Clean Water (2)
- (-) Partnerships (31)
- Advanced Reactors (12)
- Artificial Intelligence (35)
- Big Data (8)
- Bioenergy (25)
- Biology (26)
- Biomedical (17)
- Biotechnology (10)
- Buildings (15)
- Chemical Sciences (35)
- Composites (12)
- Computer Science (63)
- Coronavirus (17)
- Critical Materials (11)
- Cybersecurity (17)
- Education (3)
- Element Discovery (1)
- Energy Storage (43)
- Environment (38)
- Exascale Computing (13)
- Fossil Energy (1)
- Frontier (16)
- Fusion (17)
- Grid (16)
- High-Performance Computing (32)
- Isotopes (20)
- ITER (2)
- Machine Learning (13)
- Materials (60)
- Materials Science (56)
- Mercury (2)
- Microelectronics (1)
- Microscopy (17)
- Molten Salt (3)
- Nanotechnology (29)
- National Security (18)
- Neutron Science (54)
- Nuclear Energy (28)
- Physics (26)
- Polymers (13)
- Quantum Computing (13)
- Quantum Science (31)
- Security (12)
- Simulation (10)
- Space Exploration (3)
- Statistics (1)
- Summit (22)
- Transportation (26)
Media Contacts

Recent advancements at ORNL show that 3D-printed metal molds offer a faster, more cost-effective and flexible approach to producing large composite components for mass-produced vehicles than traditional tooling methods.

ORNL, the Tennessee Valley Authority and the Tennessee Department of Economic and Community Development were recognized by the Federal Laboratory Consortium, or FLC, for their efforts to develop Tennessee as a national leader in fusion energy.

Shaun Gleason has been named director of the Partnerships Office at ORNL. Gleason has worked at ORNL for several decades, in a variety of roles, including Director of Science-Security Initiative Integration, Director of the Computational Sciences and Engineering Division and Director of Institutional Planning.

Researchers with the Department of Energy’s Oak Ridge National Laboratory and Sierra Space Corporation have developed a new silicon-carbide-based thermal protection system, or TPS, for reusable commercial spacecraft.

Researchers at ORNL are using advanced manufacturing techniques to revitalize the domestic production of very large metal parts that weigh at least 10,000 pounds each and are necessary for a variety of industries, including energy.

A team led by scientists at ORNL identified and demonstrated a method to process a plant-based material called nanocellulose that reduced energy needs by a whopping 21%, using simulations on the lab’s supercomputers and follow-on analysis.
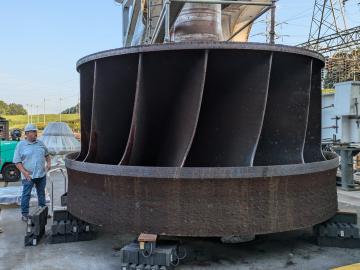
ORNL is working with industry partners to develop a technique that combines 3D printing and conventional machining to produce large metal parts for energy applications. The project, known as Rapid Research on Universal Near Net Shape Fabrication Strategies for Expedited Runner Systems, or Rapid RUNNERS, recently received $15 million in funding from DOE.
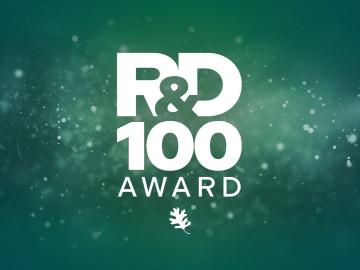
In an impressive showcase of cutting-edge innovation and scientific prowess, ORNL has been recognized as a beacon of technological excellence, receiving 14 R&D 100 Awards, announced this week by R&D World magazine.

Seven entrepreneurs comprise the next cohort of Innovation Crossroads, a DOE Lab-Embedded Entrepreneurship Program node based at ORNL. The program provides energy-related startup founders from across the nation with access to ORNL’s unique scientific resources and capabilities, as well as connect them with experts, mentors and networks to accelerate their efforts to take their world-changing ideas to the marketplace.

To better predict long-term flooding risk, scientists at the Department of Energy’s Oak Ridge National Laboratory developed a 3D modeling framework that captures the complex dynamics of water as it flows across the landscape. The framework seeks to provide valuable insights into which communities are most vulnerable as the climate changes, and was developed for a project that’s assessing climate risk and mitigation pathways for an urban area along the Southeast Texas coast.