Filter News
Area of Research
News Type
News Topics
- (-) 3-D Printing/Advanced Manufacturing (43)
- (-) Materials Science (45)
- (-) Mercury (7)
- Advanced Reactors (15)
- Artificial Intelligence (17)
- Big Data (21)
- Bioenergy (32)
- Biology (38)
- Biomedical (19)
- Biotechnology (7)
- Buildings (27)
- Chemical Sciences (17)
- Clean Water (19)
- Climate Change (36)
- Composites (11)
- Computer Science (52)
- Coronavirus (17)
- Critical Materials (13)
- Cybersecurity (9)
- Decarbonization (23)
- Energy Storage (45)
- Environment (80)
- Exascale Computing (4)
- Frontier (4)
- Fusion (16)
- Grid (27)
- High-Performance Computing (20)
- Hydropower (8)
- Irradiation (2)
- Isotopes (14)
- ITER (4)
- Machine Learning (15)
- Materials (42)
- Mathematics (5)
- Microscopy (20)
- Molten Salt (5)
- Nanotechnology (18)
- National Security (18)
- Net Zero (3)
- Neutron Science (35)
- Nuclear Energy (32)
- Partnerships (1)
- Physics (20)
- Polymers (14)
- Quantum Computing (5)
- Quantum Science (12)
- Security (7)
- Simulation (10)
- Space Exploration (10)
- Statistics (1)
- Summit (8)
- Sustainable Energy (57)
- Transportation (47)
Media Contacts

Oak Ridge National Laboratory scientists ingeniously created a sustainable, soft material by combining rubber with woody reinforcements and incorporating “smart” linkages between the components that unlock on demand.

ORNL scientists develop a sample holder that tumbles powdered photochemical materials within a neutron beamline — exposing more of the material to light for increased photo-activation and better photochemistry data capture.

ORNL researchers used electron-beam additive manufacturing to 3D-print the first complex, defect-free tungsten parts with complex geometries.

Canan Karakaya, a R&D Staff member in the Chemical Process Scale-Up group at ORNL, was inspired to become a chemical engineer after she experienced a magical transformation that turned ammonia gas into ammonium nitrate, turning a liquid into white flakes gently floating through the air.
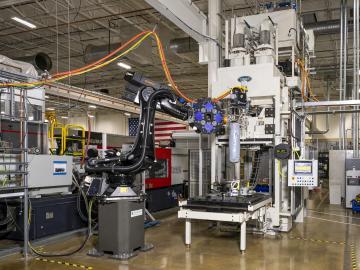
An Oak Ridge National Laboratory-developed advanced manufacturing technology, AMCM, was recently licensed by Orbital Composites and enables the rapid production of composite-based components, which could accelerate the decarbonization of vehicles
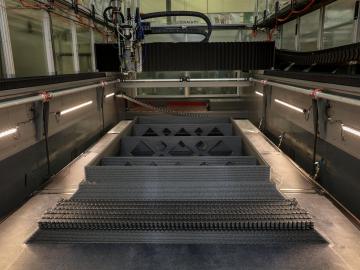
Oak Ridge National Laboratory researchers have conducted a comprehensive life cycle, cost and carbon emissions analysis on 3D-printed molds for precast concrete and determined the method is economically beneficial compared to conventional wood molds.

Madhavi Martin brings a physicist’s tools and perspective to biological and environmental research at the Department of Energy’s Oak Ridge National Laboratory, supporting advances in bioenergy, soil carbon storage and environmental monitoring, and even helping solve a murder mystery.

In the search for ways to fight methylmercury in global waterways, scientists at Oak Ridge National Laboratory discovered that some forms of phytoplankton are good at degrading the potent neurotoxin.

When reading the novel Jurassic Park as a teenager, Jerry Parks found the passages about gene sequencing and supercomputers fascinating, but never imagined he might someday pursue such futuristic-sounding science.

A new report published by ORNL assessed how advanced manufacturing and materials, such as 3D printing and novel component coatings, could offer solutions to modernize the existing fleet and design new approaches to hydropower.