
Filter News
Area of Research
News Type
News Topics
- (-) 3-D Printing/Advanced Manufacturing (43)
- (-) ITER (4)
- (-) Mercury (7)
- Advanced Reactors (15)
- Artificial Intelligence (17)
- Big Data (23)
- Bioenergy (33)
- Biology (39)
- Biomedical (19)
- Biotechnology (7)
- Buildings (28)
- Chemical Sciences (19)
- Clean Water (19)
- Climate Change (37)
- Composites (11)
- Computer Science (53)
- Coronavirus (17)
- Critical Materials (13)
- Cybersecurity (9)
- Decarbonization (24)
- Energy Storage (45)
- Environment (80)
- Exascale Computing (4)
- Fossil Energy (1)
- Frontier (4)
- Fusion (16)
- Grid (28)
- High-Performance Computing (20)
- Hydropower (8)
- Irradiation (2)
- Isotopes (15)
- Machine Learning (16)
- Materials (42)
- Materials Science (46)
- Mathematics (6)
- Microscopy (20)
- Molten Salt (5)
- Nanotechnology (18)
- National Security (19)
- Net Zero (4)
- Neutron Science (35)
- Nuclear Energy (34)
- Partnerships (1)
- Physics (20)
- Polymers (14)
- Quantum Computing (5)
- Quantum Science (12)
- Security (7)
- Simulation (11)
- Space Exploration (10)
- Statistics (1)
- Summit (8)
- Sustainable Energy (58)
- Transportation (47)
Media Contacts

Oak Ridge National Laboratory researchers have demonstrated that a new class of superalloys made of cobalt and nickel remains crack-free and defect-resistant in extreme heat, making them conducive for use in metal-based 3D printing applications.
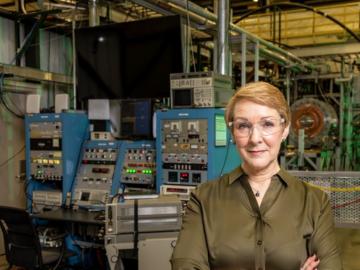
From the helm of a one-of-a-kind organization that brings nuclear fusion and fission expertise together to pave the way to expanding carbon-free energy, Kathy McCarthy can trace the first step of her engineering career back to

Collaborators at Oak Ridge National Laboratory and the University of Tennessee Health Science Center are developing a breath-sampling whistle that could make COVID-19 screening easy to do at home.
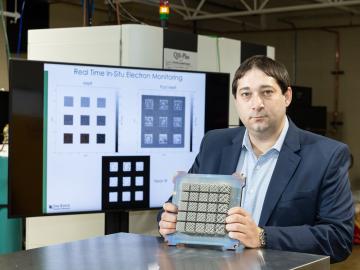
Growing up in the heart of the American automobile industry near Detroit, Oak Ridge National Laboratory materials scientist Mike Kirka was no stranger to manufacturing.
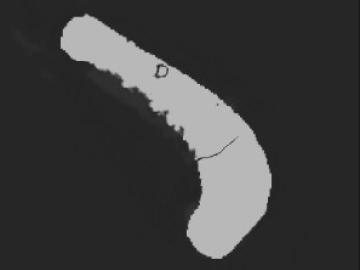
Algorithms developed at Oak Ridge National Laboratory can greatly enhance X-ray computed tomography images of 3D-printed metal parts, resulting in more accurate, faster scans.
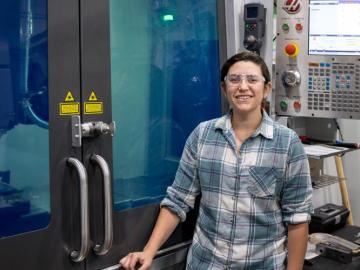
Growing up in Florida, Emma Betters was fascinated by rockets and for good reason. Any time she wanted to see a space shuttle launch from NASA’s nearby Kennedy Space Center, all she had to do was sit on her front porch.

Scientists at Oak Ridge National Laboratory and the University of Tennessee designed and demonstrated a method to make carbon-based materials that can be used as electrodes compatible with a specific semiconductor circuitry.
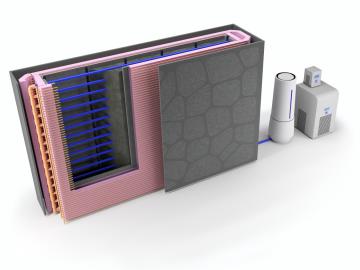
Oak Ridge National Laboratory researchers used additive manufacturing to build a first-of-its kind smart wall called EMPOWER.
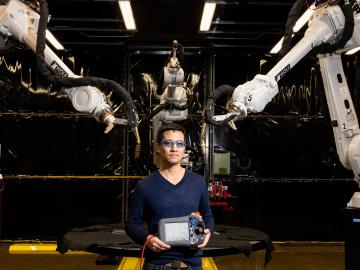
Peter Wang is focused on robotics and automation at the Department of Energy’s Manufacturing Demonstration Facility at ORNL, working on high-profile projects such as the MedUSA, a large-scale hybrid additive manufacturing machine.
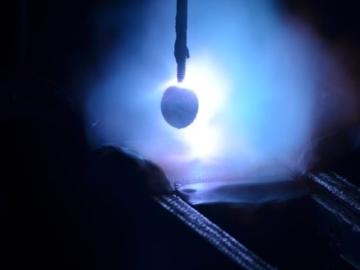
Researchers at Oak Ridge National Laboratory demonstrated that an additively manufactured polymer layer, when applied to carbon fiber reinforced plastic, or CFRP, can serve as an effective protector against aircraft lightning strikes.