Filter News
Area of Research
- Advanced Manufacturing (12)
- Biology and Environment (3)
- Building Technologies (1)
- Clean Energy (38)
- Fusion and Fission (4)
- Fusion Energy (5)
- Materials (17)
- Materials for Computing (3)
- National Security (2)
- Neutron Science (1)
- Nuclear Science and Technology (13)
- Nuclear Systems Modeling, Simulation and Validation (1)
- Supercomputing (3)
News Type
News Topics
- (-) 3-D Printing/Advanced Manufacturing (43)
- (-) Nuclear Energy (32)
- (-) Polymers (14)
- Advanced Reactors (15)
- Artificial Intelligence (17)
- Big Data (21)
- Bioenergy (32)
- Biology (38)
- Biomedical (19)
- Biotechnology (7)
- Buildings (27)
- Chemical Sciences (17)
- Clean Water (19)
- Climate Change (36)
- Composites (11)
- Computer Science (52)
- Coronavirus (17)
- Critical Materials (13)
- Cybersecurity (9)
- Decarbonization (23)
- Energy Storage (45)
- Environment (80)
- Exascale Computing (4)
- Frontier (4)
- Fusion (16)
- Grid (27)
- High-Performance Computing (20)
- Hydropower (8)
- Irradiation (2)
- Isotopes (14)
- ITER (4)
- Machine Learning (15)
- Materials (42)
- Materials Science (45)
- Mathematics (5)
- Mercury (7)
- Microscopy (20)
- Molten Salt (5)
- Nanotechnology (18)
- National Security (18)
- Net Zero (3)
- Neutron Science (35)
- Partnerships (1)
- Physics (20)
- Quantum Computing (5)
- Quantum Science (12)
- Security (7)
- Simulation (10)
- Space Exploration (10)
- Statistics (1)
- Summit (8)
- Sustainable Energy (57)
- Transportation (47)
Media Contacts

Oak Ridge National Laboratory scientists ingeniously created a sustainable, soft material by combining rubber with woody reinforcements and incorporating “smart” linkages between the components that unlock on demand.

Mohamad Zineddin hopes to establish an interdisciplinary center of excellence for nuclear security at ORNL, combining critical infrastructure assessment and protection, risk mitigation, leadership in nuclear security, education and training, nuclear security culture and resilience strategies and techniques.

Canan Karakaya, a R&D Staff member in the Chemical Process Scale-Up group at ORNL, was inspired to become a chemical engineer after she experienced a magical transformation that turned ammonia gas into ammonium nitrate, turning a liquid into white flakes gently floating through the air.

Chelsea Chen, a polymer physicist at ORNL, is studying ion transport in solid electrolytes that could help electric vehicle battery charges last longer.
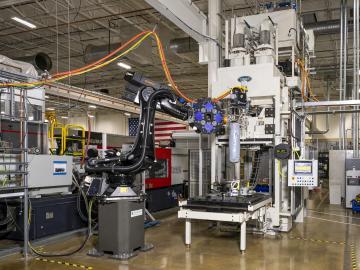
An Oak Ridge National Laboratory-developed advanced manufacturing technology, AMCM, was recently licensed by Orbital Composites and enables the rapid production of composite-based components, which could accelerate the decarbonization of vehicles
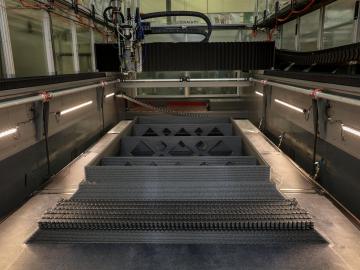
Oak Ridge National Laboratory researchers have conducted a comprehensive life cycle, cost and carbon emissions analysis on 3D-printed molds for precast concrete and determined the method is economically beneficial compared to conventional wood molds.

Chemist Jeff Foster is looking for ways to control sequencing in polymers that could result in designer molecules to benefit a variety of industries, including medicine and energy.

A new report published by ORNL assessed how advanced manufacturing and materials, such as 3D printing and novel component coatings, could offer solutions to modernize the existing fleet and design new approaches to hydropower.

Scientists at ORNL developed a competitive, eco-friendly alternative made without harmful blowing agents.

Stephen Dahunsi’s desire to see more countries safely deploy nuclear energy is personal. Growing up in Nigeria, he routinely witnessed prolonged electricity blackouts as a result of unreliable energy supplies. It’s a problem he hopes future generations won’t have to experience.